Change Your Thinking From First Cost to Total Cost
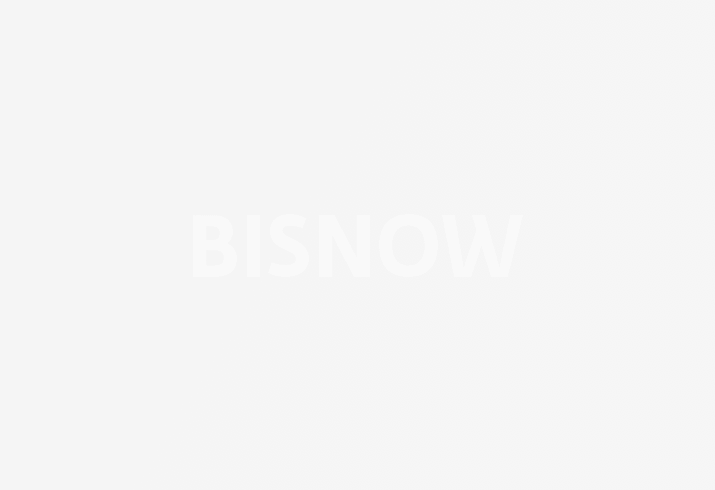
Consider the total life cycle cost of a building: That’s the enticement—and reality—for many industrial project owners rethinking their approach to capital investment decisions. This flies in the face of the traditional approach, in which the focus is on the initial cost of construction (including the cost of the building itself, the land, finance fees, design development fees, and furniture, fixtures and equipment). JE Dunn industrial group VP Brent Strength says that the more contemporary formula is to focus more broadly on the total cost of ownership (TCO) because initial costs are only a fraction of the total cost of building ownership. TCO gives owners a huge advantage in weighing a wide range of options, including major systems and equipment purchases and the amount and types of glass they install. This is particularly relevant to industrial and manufacturing buildings, which can often have a higher cost of ownership due to building size and the energy consumption required for operation and manufacturing processes. These buildings often have more sophisticated systems, so the maintenance and repair cost evaluation is important. Tapping into the company’s database of construction knowledge, energy modeling programs and industry maintenance data, JE Dunn has developed a TCO tool to analyze construction, maintenance, operating, replacement and energy costs. The tool can be expanded to analyze day-to-day workflow in a facility, and the impact that different design schemes can have on worker productivity. This tool is directly linked to ASE, JE Dunn’s proprietary conceptual estimating software. During the design stage, it can evaluate various options and provide real-time input on both initial cost and TCO. To find out more about our Bisnow partner, click here.