Will Falling Shipping Costs Hurt Baltimore’s Port-Centric Industrial Boom?
The cost of shipping goods has fallen dramatically over the course of this year. While lower prices are generally positive for businesses and consumers, they may be a bad sign for fast-developing industrial markets in port cities like Baltimore.
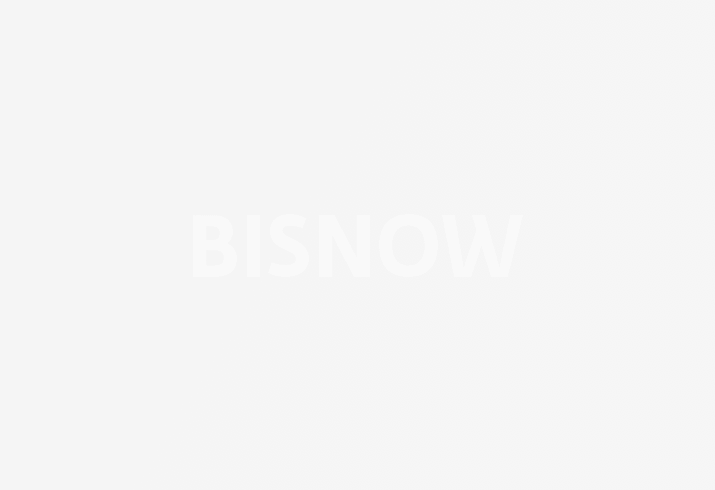
The cost to ship a 40-foot container from Asia to the East Coast fell by two-thirds from April to November, according to Freightos. In October, the volume of U.S. container imports fell 13% year-over-year, according to the logistics research firm Descartes Systems Group.
The falling cost and volume of shipping reflects a drop in consumer demand for goods because of a slowing economy, according to both research reports. This comes as millions of square feet of industrial space are under construction that depend on high demand for goods.
The industrial sector, locally and nationally, thrived during the pandemic because businesses like Amazon invested heavily in warehousing and distribution. Firms leased and purchased major properties in order to have products on hand to avoid supply chain disruptions caused by the pandemic.
Industrial developers have responded by ramping up construction of new projects to meet the demand for space. In the Baltimore market, over 6.7M SF of industrial was under construction as of the third quarter, a 31% increase from last year, according to JLL.
Much of the demand for industrial space in the Baltimore region has been driven by its position to key logistics hubs, such as Baltimore Washington International Airport, the Port of Baltimore and Interstate 95. A slowdown in the amount of goods shipping through those hubs has the potential to create less demand, causing rents to drop and vacancy to rise.
But those potential impacts aren't being felt in the market today, said industrial developer Jim Lighthizer, a principal at Chesapeake Real Estate Group.
“There’s demand out there and virtually no available space,” Lighthizer said. “The shipping costs and supply chain [disruptions] they helped during Covid, but we have not seen any drop in demand or increase in inventory in the last couple of months because of the [falling] shipping costs.”
“For the commercial real estate world, we’re much more a function of the economy as a whole,” added Lighthizer, who serves on NAIOP’s national forum of industrial developers.
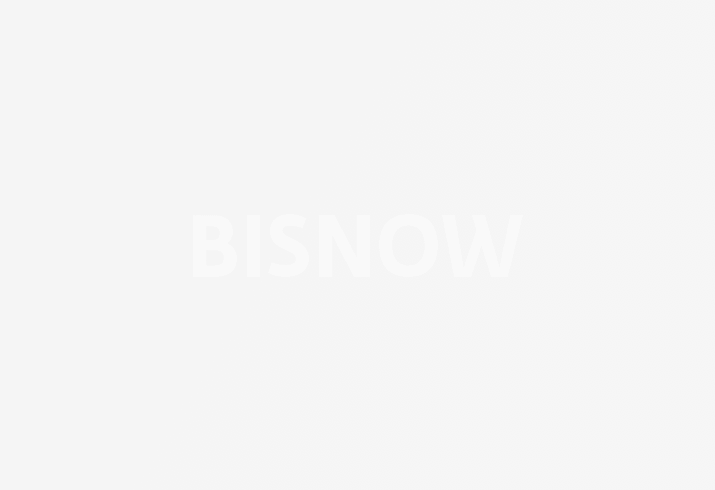
JLL’s latest report on the Baltimore industrial market found tenants absorbed more than 2.5M SF throughout the first three quarters of 2022. As a result, it found warehouse and distribution vacancies in the region fell to 3.8%, and the average asking rent increased by nearly 8%.
Yet there’s concern that the red-hot market for industrial properties may be headed for a cooldown. The Wall Street Journal reported in October that commercial developers are becoming more cautious about starting new projects due to increased borrowing costs and falling shipping prices.
While falling shipping prices may present risks for the industrial market, the ability to buy commodities like steel and timber at lower costs can help builders hindered by the high price of construction.
During Bisnow’s State of Baltimore County event in October, developers said they were considering pausing new projects to see what happens with construction costs. Builders on the panel opined about the high cost of building materials and labor.
Greenberg Gibbons CEO Brian Gibbons said he remained skeptical that construction prices will ever return to pre-pandemic levels. Construction prices, he said, have never declined during decades as a developer.
"Frankly, that's what the Fed is trying to do with all the interest rates going up is trying to slow down construction with the hopes of bringing costs down," Gibbons said.
Lee & Associates President Allan Riorda, in a recent e-newsletter, wrote those falling shipping costs likely portend an overall easing in inflation. But that outcome depends on supply chain bottlenecks loosening.
Locally there are still plenty of supply chain disruptions giving local developers and property owners headaches, Riorda told Bisnow.
One current source of frustration, he said, is ongoing delays in steel manufacturing. Local developers and property owners face inordinately long waits to install dock doors because the springs used in the mechanisms that open dock doors at warehouse and distribution facilities are made of steel.
“Fortunately, with buildings, you do have a pretty good heads up when you’re going to need those things,” Riorda said.
Those supply chain kinks also impact the commercial real estate industry by creating conflicts with leases.
An example of how those supply chain hiccups impact leases, Riorda said, is if a hypothetical company signed a lease in October at a new building. In order to operate in the new space, the company would need custom-built racks installed prior to moving in.
Those racks would be scheduled to arrive in time to be installed before the tenant’s lease starts in January. But if a supply chain kink pushed the delivery back to March, that would leave the business owner and the property owner in a stitch because the tenant can’t move until those racks are installed.
“It creates some real issues as it relates to a tenant's timeline,” Riorda said.