One of Boston's Most Complex Construction Sites
The $500M, 680k SF Building for the Future being developed by Brigham & Women’s Hospital is the largest project under construction in Longwood Medical Area. Like many big things, it's also incredibly complex. At Bisnow’s Construction & Development Summit, we're going to find out how Suffolk Construction is pulling off the project in the tightest of circumstances. Join us April 30, 7:30am, at the Sheraton Boston. Register.
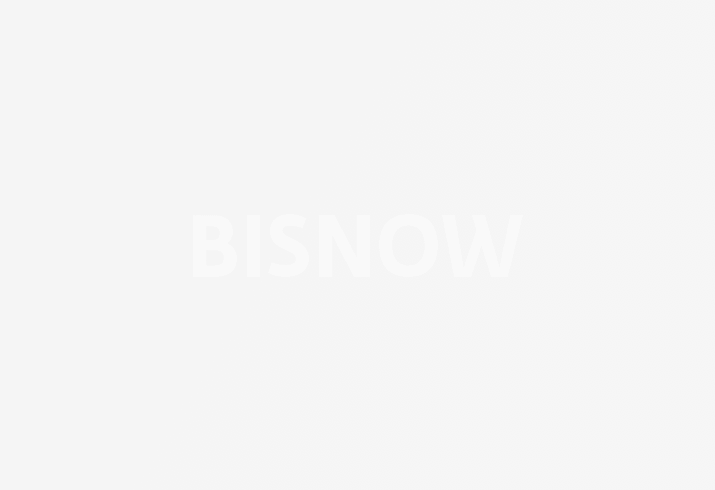
When it opens in fall 2016, Brigham & Women’s will, for the first time, house under one roof clinicians and researchers dealing with neurological disorders, explains Brigham & Women's VP of finance and real estate Vincent McDermott (a panelist at our event, here with senior financial analyst Rob Bentinck-Smith). Through easier, more frequent interaction, they hope to more rapidly discover new medicines and therapies. For instance, they'd like to develop one pill to treat some patients who now undergo multiple, time-consuming rounds of infusion therapy, Vinnie tells Bisnow.
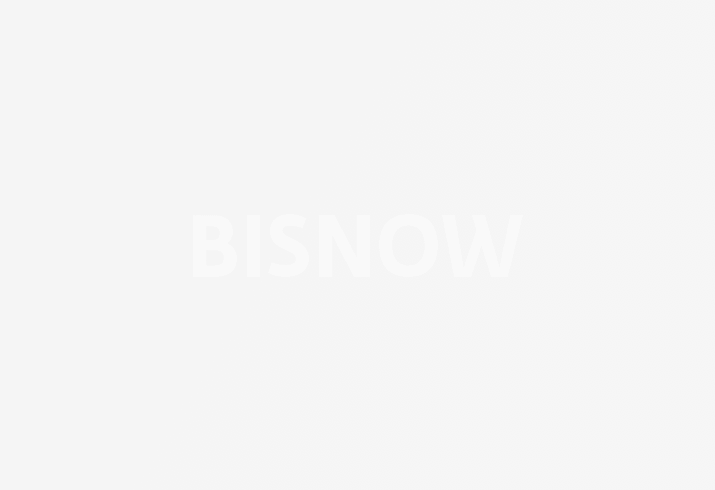
Many professionals are currently scattered around the hospital’s 2M SF, nine-acre campus. But the new building will bring together scientists researching neurological issues in wet labs, dry labs, and clinicians who are treating patients. A large common cafeteria, a roof garden and other collaborative places will enhance the probability that they’ll inform each other's work. Patients with restricted mobility will no longer have to travel several blocks to go from an exam room to an imaging suite.
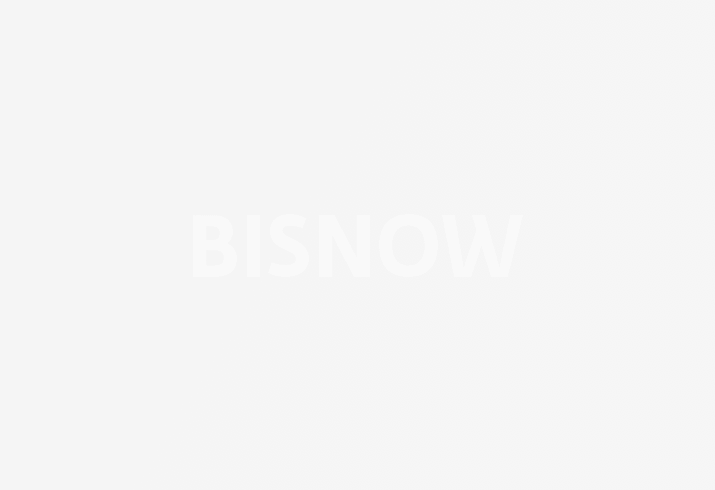
The building's design imparts the message that there’s something special inside, says Steve Dempsey, director of planning and construction. The glass-and-metal clad exterior expresses discovery with its judiciously placed green and blue metal fins shimmering in the daylight. Much of the curtain wall is already visible thanks to Suffolk Construction's “up-up” technique. Usually, the core of a building that houses the intricate MEP systems is built first, followed by the shell. Here, the two elements are going up simultaneously. “Up-up” construction is shaving two months off the 36-month schedule to help compensate for the time lost during the Terrible Winter of 2015, Vinnie says. The lean construction approach is also saving time.
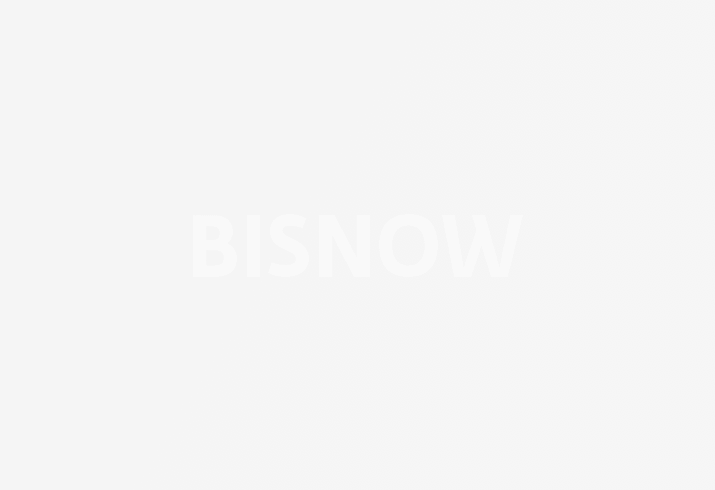
Floors 1-8 are finished, and concrete is being poured on the the last one, No. 14. The construction manager, engineers, the architect and owners’ rep all have on-site offices so they're face-to-face to make decisions fast. When Brigham decided to add an extra floor, they could move quickly to accommodate the change, says construction manager Suffolk Construction’s senior project manager Jason Seaburg (an event panelist). They worked with the structural engineer to redesign the foundations, which were to slated to be poured within six weeks of the request, he recalls.
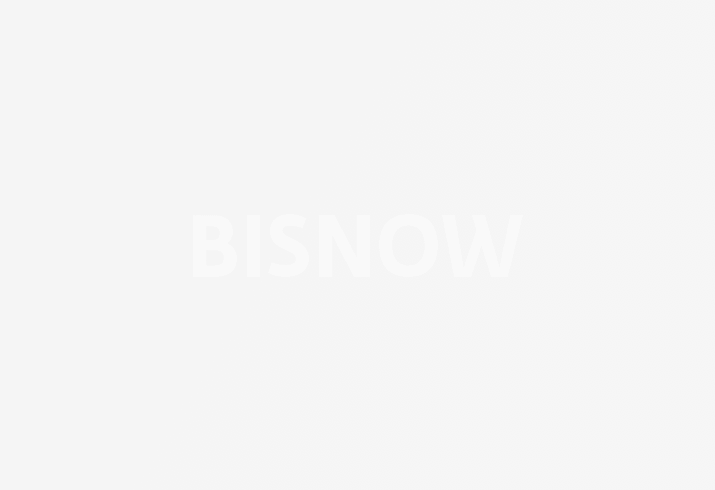
Besides snowfall, other challenges include working on a residential street where the crew has to control the dust, noise and lights. Upon request, the team provides neighbors with light blinding shades. Sharing the Brigham site is the Tenants of Harvard, a 140-apartment multifamily building for which prep work just started. To make room, the Brigham crew moved its construction trailers and is managing to work around them in tight quarters. In the Brigham building, a sensitive underground MRI suite shares a floor with the 400-car parking garage. To avoid disrupting the imagery, NBBJ designed extra thick concrete walls with lead shielding.
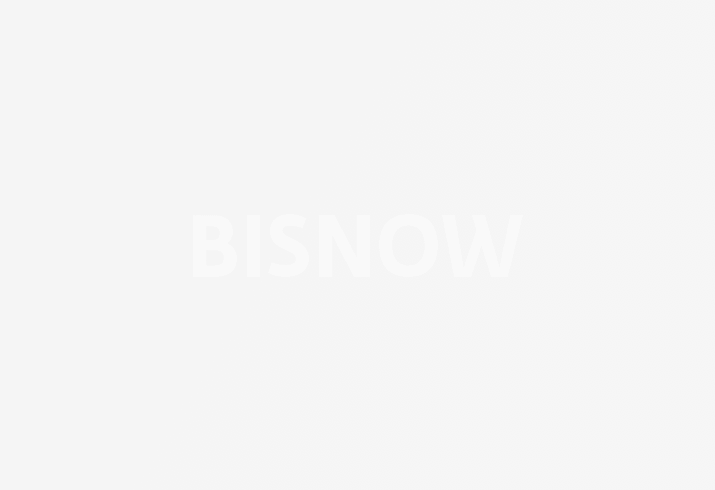
For Suffolk Construction, the biggest challenge is that the Boston market has more construction underway and planned for the next three to five years than it’s had in the past 35 years, Jason tells us. It’s a struggle to find qualified subcontractors. Five years ago, Suffolk might have received seven qualified bids for a job; now it gets just two or three. The key to adjusting is taking the lean construction approach. By having the entire project team assembled, co-located and collaborating from day one, the Building for the Future crew was able to design a sprinkler system that is inside the structural steel. That allowed the sprinkler engineer to get onto the site and work undisturbed and fast before the more heavy duty MEP crews arrived.
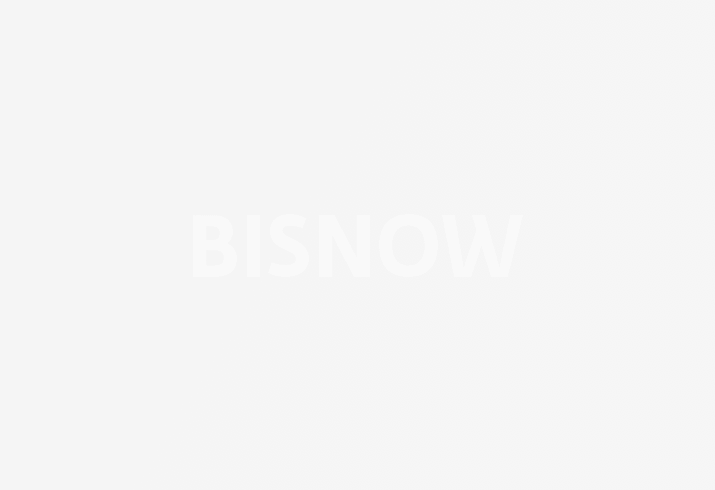
Just a few blocks away in the quickly transforming Fenway, tenants will soon move into yet another new multifamily building: The Abbey Groups’ 342-apartment Viridian on Boylston Street. The 18-story high-rise has been designed to further the “urban village plan” created by neighborhood groups and city planners who wrote new zoning for the area several years ago, says architect and Bruner/Cott principal Jason Forney (an event panelist). The Viridian joins several other recent residential, hotel, retail and office projects that are replacing the parking lots and old, low-rise structures that once dominated the neighborhood’s main arteries.
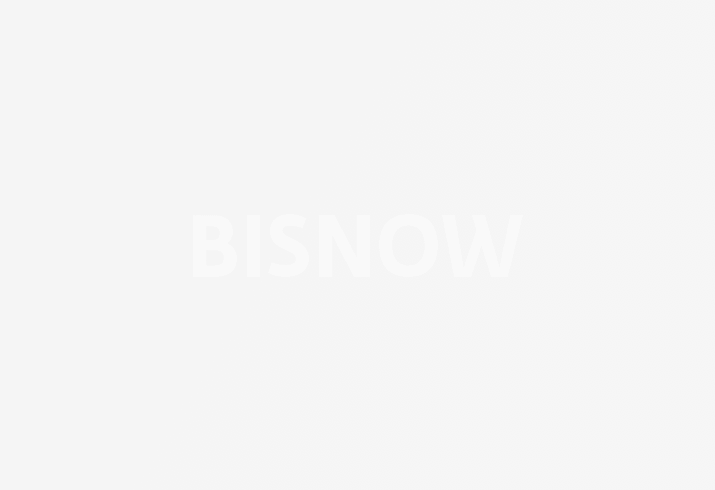
The Viridian is tall, slender, contemporary and is introducing 350 linear feet of ground floor, 10k SF of retail and the Fenway Community Center. It has parking for 180 bikes and only 295 cars. The tall terra cotta clad high-rise, LEED Gold designed, has modest-size apartments. But many have floor-to-ceiling glass sliders and Juliet balconies so residents can connect with the outside community, where they’ll find a cornucopia of live/work/play attractions, including Frederick Law Olmsted’s beautiful Fenway parkland. Jason and the other expert panelists will have a lot more to say at Bisnow’s Construction & Development Summit. 7:30am, April 30, at the Sheraton Boston. (Sign Up Here.)