Modular Healthcare Construction Picking Up As On-Site Labor Gets More Challenging
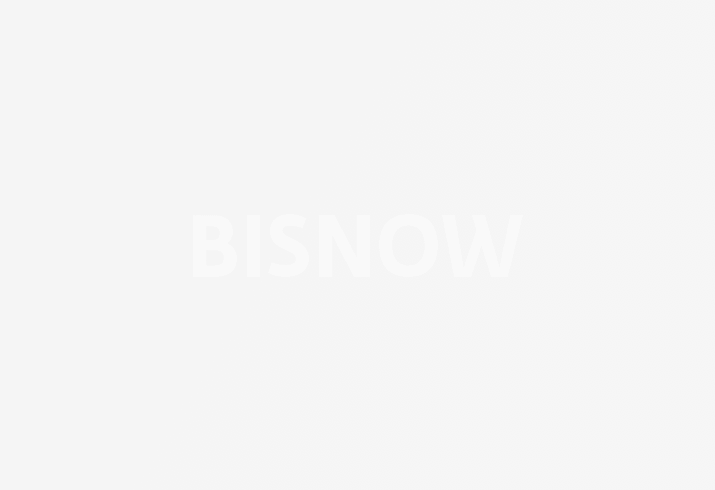
Like everything else, the healthcare construction industry has changed in many ways as a result of the coronavirus pandemic.
According to Gary Hamilton, a senior vice president at design firm WSP, cost-conscious potential clients routinely ask him how he plans to use prefab and modular construction when they interview him.
“Modular construction has been more [prevalent] in the West Coast," Hamilton said on Bisnow's Innovations in Healthcare Construction webinar this week. “Since the onset of the pandemic, a lot of owners are talking about prefab.”
Shortages of skilled labor have led to the construction of more pieces of buildings away from construction sites. Fewer construction workers on-site also lessens the burdens of social distancing that companies are practicing to prevent outbreaks of the virus that has left more than 200,000 Americans dead.
“That is something that’s going to be commonplace going forward,” said Hamilton, who oversees WSP's healthcare business in the Northeast.
Brian Garbecki, vice president and director of national healthcare at Gilbane Building Co., said many healthcare construction projects were upended when the coronavirus pandemic struck earlier this year.
“If the project was in the early stages of planning, some projects did go on hold,’” he said. “If the project was in the later stages of planning and the earlier stages of design, there was maybe a slight pause. Some of them went forward with modifications to address some of the issues related to COVID.
“If the project was further along in design or further along in construction, they didn’t miss a beat,” he added.
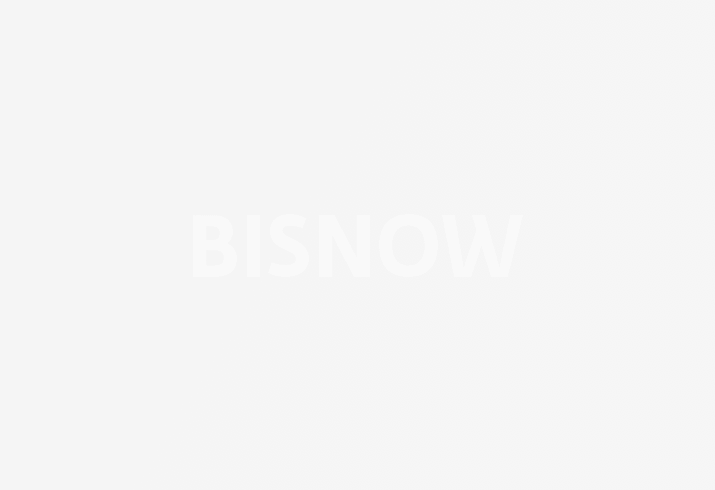
Gilbane has kept busy during the health crisis. The company converted a civic center in the Detroit area to a 1,000-bed hospital for COVID patients. It also transformed a Boston hospital slated to close to a 300-bed facility for the homeless and built a 20-bed ICU pandemic unit in Maryland in 120 days.
“There are a lot of different things that came out in the past six months that will be helpful going forward as we recover from the COVID situation," Garbecki said.
For hospital operators like Jacksonville, Florida-based Baptist Health, the last few months have been especially trying because models for the pandemic had dire forecasts for deaths and hospitalizations later found to be inaccurate.
“The models had numbers that were much higher than we experienced, and we are thankful for that, but we were responding to [those] early numbers,” said Kimberly Hansen, who oversees design and construction at Baptist Health. “We were looking across our system for where we had isolation rooms.”
Local officials also asked Baptist about its surge capacity, causing the company to convert every available inch of space to patient care, including the staff cafeteria, which had already been closed, Hansen said.