Evolution Of E-Commerce Influencing Industrial
E-commerce continues to stimulate demand for industrial and warehouse space, as does a steadily growing manufacturing sector. This combination is augmented by the improving economy and a lack of existing high bay facilities, producing tremendous potential for this asset class and propelling it to unanticipated levels of development.
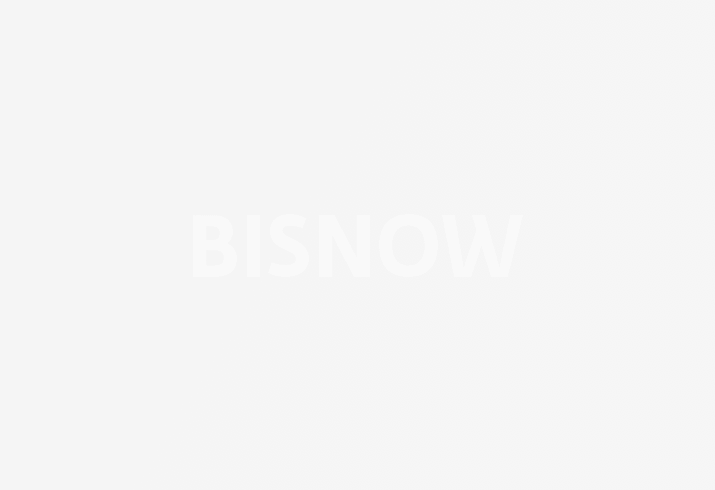
E-commerce is growing at rates that greatly exceed the economy’s overall growth, checking overbuilding and corollary supply gluts, and keeping vacancy rates low.
Today’s increasingly sophisticated e-commerce operations require vast networks of warehouses that serve as inventory stores and fulfillment centers catering to the short delivery windows companies must offer to stay competitive.
Consequently, there is significant migration in this asset class, from low-rent rural areas to pricier suburban locations, to meet same-day and two-day delivery expectations. This move boosts land and rent prices but simultaneously reduces transportation costs, a key concern for GourmetGiftBaskets.com, which engaged PROCON to design and build the 105k SF facility pictured above. GourmetGiftBaskets' explosive growth in recent years has necessitated larger, strategically located, high-efficiency facilities to answer it needs while minimizing overall operating costs.
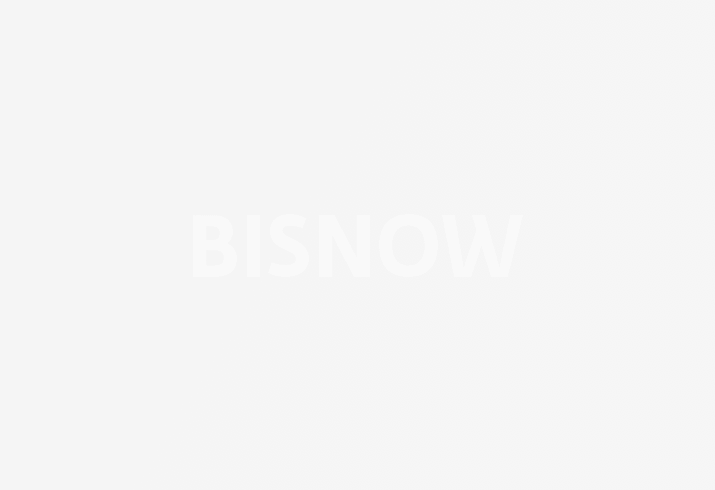
High bays are needed to accommodate the taller racking systems that allow greater storage capacity and the higher degree of automation and mechanization seen in internal logistics at warehouses like the one installed for packaging solution company Rand-Whitney (above). 100k SF facilities or bigger are becoming common, due to the inbound, outbound and return volumes they handle.
30% of the goods people order online are returned, compared to the 5% merchandise return rate at brick-and-mortar shops, and e-retailers are trying to consolidate space to maximize efficiency.
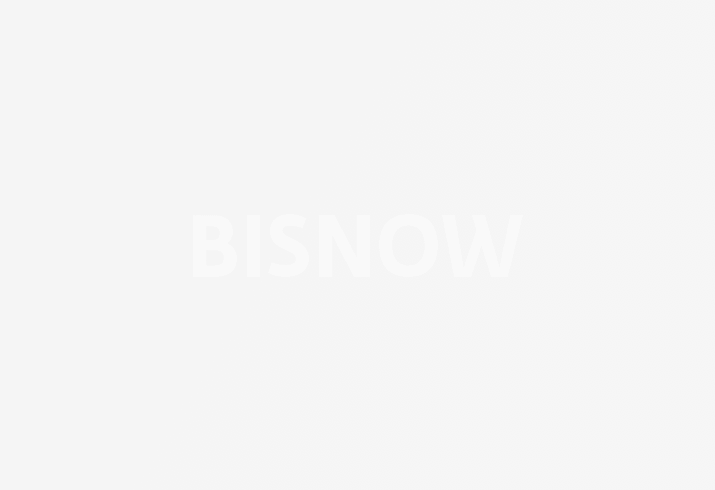
Firms also want more energy-efficient, better-insulated buildings equipped with advanced heating and cooling systems and automated LED lighting that assist in lowering operating cost.
Coordinating architects, multiple engineers, construction workers and auxiliaries is not an easy task. Many businesses are looking to simplify project management, from inception to completion, by enlisting horizontally integrated firms like PROCON that encompass all necessary components.
The assimilation of the horizontal integration paradigm of architects, engineers and construction management professionals on one team ensures all constituents are communicating and proceeding in a timely manner. It also unburdens the developer of the task of assembling and managing a more complex team as well as the risk of extra costs from change orders caused by flawed assumptions.
This efficient single-source delivery system also allows for a quicker completion. The 234k SF Exel facility (above) was completed in one year with an eight-month construction schedule.
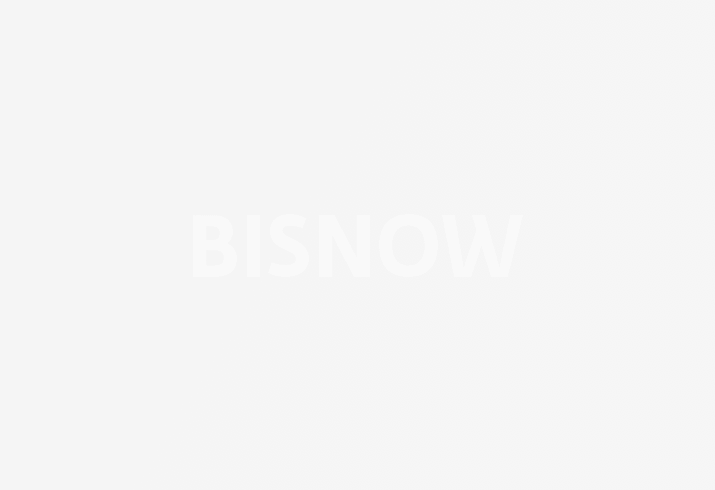
30-year PROCON employee and director of business development Paul Roy has witnessed firsthand the evolution of the single-source delivery system, from the days of large pre-engineered steel warehouses to today’s high bay logistic/fulfillment facilities with sophisticated systems, like the conveyor network at Rand-Whitney (above).
“It is amazing to see how much this building type and delivery has changed,” he tells us. “We have shortened our construction schedules and are delivering high-quality, energy-efficient buildings that are extremely attractive and welcome additions to the towns they are developed in.”
To learn more about PROCON, click here.