Speed-To-Market Challenges Twofold For Life Sciences Developers In Boston
Speed-to-market is king in Boston’s severely undersupplied life sciences market, leading developers to take leaps of faith in the construction process as they rush to meet the region’s overwhelming demand.
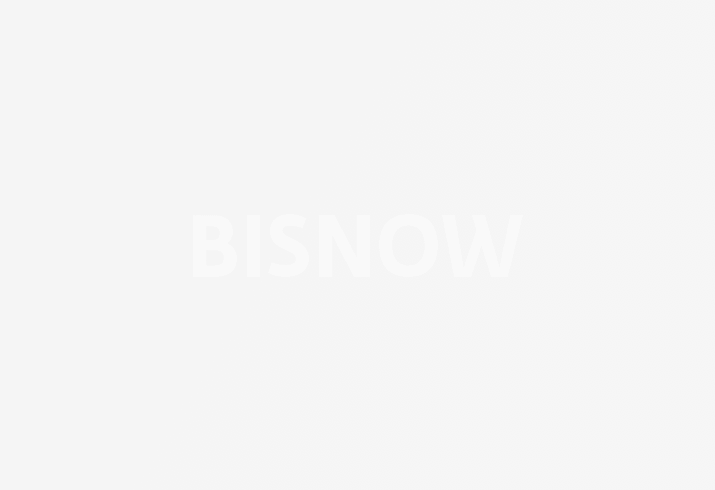
Lab and research and development builders are facing the industrywide challenges of the global supply chain’s disruptions, including high construction costs and long lead times. Life sciences developers also face thorough, lengthy permitting processes, forcing some to commit to purchasing materials earlier than ever.
“We’re seeing a lot of the projects taking the risk of ordering the materials and advancing the design right through the permitting process so you can get on the ground quickly,” SGA partner and Director of Architecture John Sullivan said last week at Bisnow’s Greater Boston Lab and Manufacturing Facilities event.
The Boston market for life sciences spaces is as tight as can be, with labs 99.9% occupied in the urban core, according to CBRE research. Deliveries through the rest of the year are 98% pre-leased, and developers are working to deliver 10M SF of new and repositioned products by 2024. Developers can achieve average asking rents regularly above $100 per SF in Boston and Cambridge, according to CBRE, still making the projects a lucrative play.
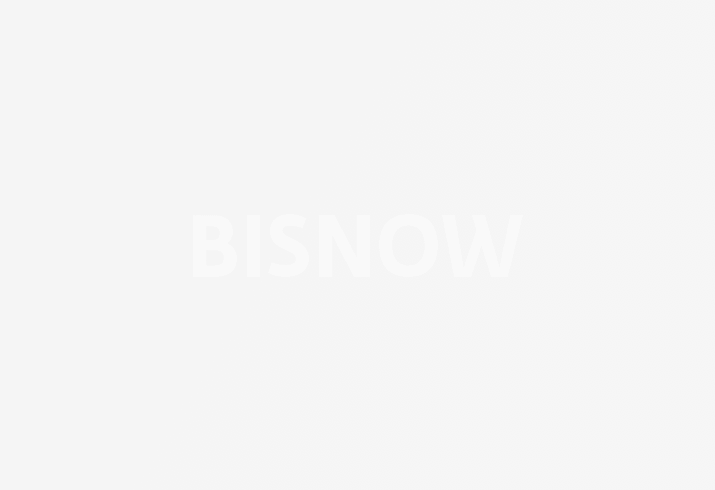
The industry isn’t immune to the global supply chain’s impact on construction materials. What once was a 35-day cycle to get materials distributed from ports to builders has turned into a 78-day cycle because of a backlog of container ships at the nation’s busiest ports, Canton, Massachusetts-based Timberline Construction CEO Steven Kelly said.
“The commodities have been very volatile,” he said. “We’ve got contractors submitting the bid saying they’ll only honor it for five days.”
The delays are affecting materials as simple as wood doors, which can take between 24 and 36 weeks to deliver. They are also impacting critical HVAC components that help achieve labs’ greater air circulation requirements; HVAC materials can take up to six months to deliver, panelists said.
Even a matte black paint delivery from Texas for a Timberline client has been slowed because of the state’s recent storms, Kelly said. The sophisticated technologies and heavy infrastructure required to produce today’s complex, small molecule medicines have also complicated matters. Getting ahead of the delays is crucial, prompting developers to order materials much earlier in the construction process than when they were readily available in the past.
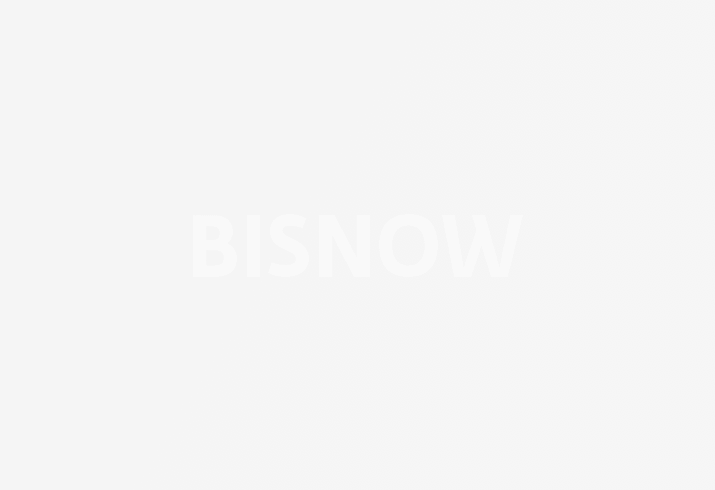
"Our equity partners understand this is a risk point,” Jumbo Capital Vice President Nick Trocki said. “It’s time to release materials, it’s time there’s a point of no return. You can’t have buyer’s remorse.”
Boston-based The Davis Cos. in the past two to three years started ordering lab benches for spec developments, something the developer would never have considered previously, The Davis Cos. Senior Vice President of Asset Management and Director of Leasing Duncan Gilkey said.
“They’re not cheap,” Gilkey said. “But the reality is these startup tenants didn’t realize, as great as a spec suite it is, they’ve moved in, and their vendor says it’s 18 weeks, they’ve just started paying rent with no benches.”
Construction surprises can also arise in the popular office-to-lab conversions swarming the urban submarkets consisting of millions of SF of office space. Experts called on builders to take the time to get it right or even develop a master plan instead of rushing for a demolition permit to meet the immediate industry demand.
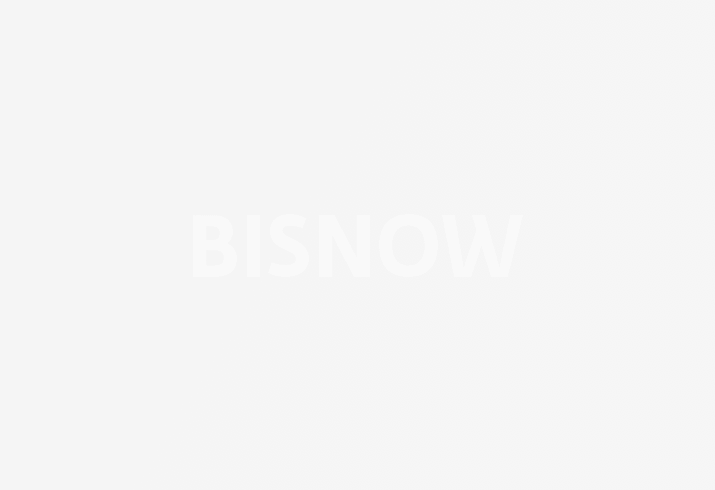
Oxford Properties has taken a thorough look at its proposed lab conversion of a former WeWork space at its 145K SF 745 Atlantic Ave. office downtown. The developer is analyzing the types of ventilation, power and loading docks it can install in the office building and determining how it can deliver space as tenants’ leases expire.
“Can you do a floor-by-floor conversion in a building?” Haverty said. “It is not worth the brain damage that happens as a result of it.”
The in-depth permitting process remains a challenge with municipalities and communities that aren’t always keen on new lab and R&D projects. In Boston, city councilors this past summer held a committee hearing to address residents’ anxiety over the rising projects in the Fort Point Channel and the Seaport neighborhoods. At least one project's developer has sued the city’s Zoning Board of Appeal over its rejected life sciences conversion in a residential neighborhood.
Suburbs, though traditionally hesitant about life sciences, have begun to turn the page, as in Newton’s approval of an Alexandria Real Estate Equities-owned lab project earlier this year. At the time, life sciences experts including Alexandria Executive Vice President and Regional Market Director Hunter Kass called on an easing of permitting and approvals. To ease tensions, Gilkey suggested tenants as the best advocates for projects.
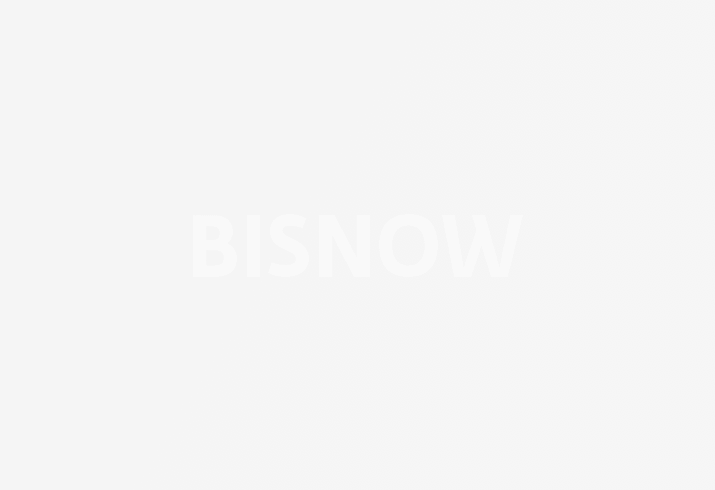
“We can position it in terms of something that’s comfortable and provide look books of spaces,” TRIA Architects Associate Principal and Director of Integrated Design Edwin Hargrave said. “To take that element of fear out of it, it looks more like a college lab rather than something that they’re imagining from a science fiction movie.”
Once construction and permitting are complete, tenant risks remain the largest factor in life sciences real estate dealings, Greystar Managing Director of U.S. East Development Gary Kerr said. The venture capital-backed biopharmaceutical and biotechnology firms deal in complex sciences and developers need to understand a company’s business plan and how they plan to spend their tenant improvement allowances.
“It’s also, unfortunately, a business where there may be a great lease deal, but you’re going to have to pass on it because the ultimate residual value is not there,” Kerr said. “That’s really tough when you’re a leasing broker.”