Headwinds Are Forming For Boston's Life Sciences Developers
Developers in the nation’s hottest life sciences market face a new slew of challenges as tenant requirements have evolved in the past few years.
Companies fueled by billions in private and public funding are rapidly expanding, forcing developers to buy into Boston’s struggling office market to undertake conversion projects, and more mature pharmaceutical companies seeking manufacturing requirements are driving competition in the competitive industrial market.
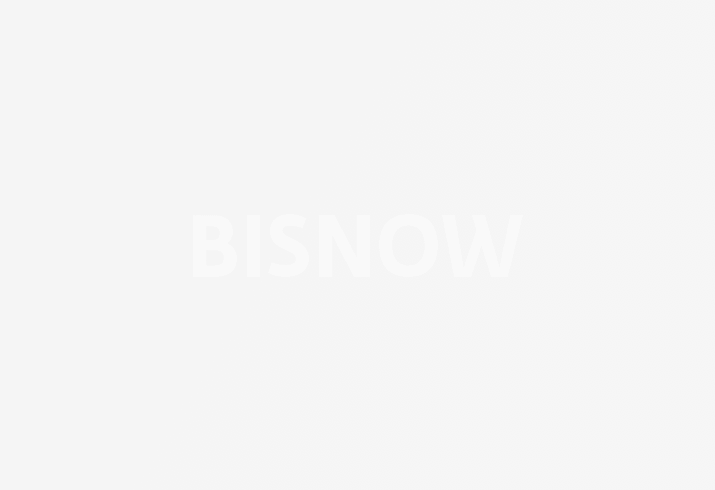
The rapidly changing market dynamics have forced developers to tread carefully into speculative development, consider tenants’ unique infrastructure needs and weigh competition with e-commerce players’ deep wallets, experts said on Bisnow’s Boston Life Sciences Forum this week.
Boston’s life sciences pipeline, which doubled in the past decade to 30M SF, may increase by as much as 50% in the coming years, researchers estimate. While some prominent developments have secured leases for deliveries in the next two years, other major builds in and around Boston are rising speculatively, a tricky proposition for developers, SMMA Senior Associate Adrian Walters said.
“We used to think of flexibility as plug-and-play casework,” Walters said. “People have sort of marched along those sort of avenues for the last 20 years. Now, we need to think about entire floors or entire facilities to be reconfigurable in a much tighter time frame than we previously encountered.”
A wave of office-to-lab pivots has washed over Boston since the coronavirus pandemic hit, including at both ground-up and existing buildings. Lab requirements like taller ceiling heights have meant some projects have to compromise on rentable floor space. Boston Global Investors’ 10 World Trade Boston spec project pivoted to include lab space last summer, removing one floor from its interior.
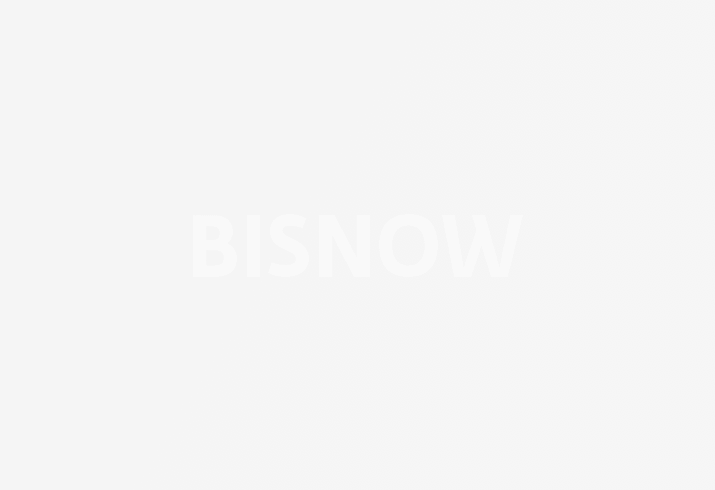
Lab incubators have had to remain at the forefront of changing demands and have adapted with Lego-like setups in which tenants can customize workbenches and suites, LabCentral CEO Maggie O’Toole said. The 100K SF Cambridge incubator can accommodate up to 100 startups or 500 scientists.
“Companies can only stay in our space for two to three years,” she said. “At first, that was something people balked at. The reality is what they found, as they grow and the technology changes, the footprint with what they start out with is vastly different than what they need in six months, 12 months, two or three years.”
Life sciences projects have significant water and power requirements, which developers must keep in line with local municipal sustainability goals. Conversions with local utilities become paramount in the development process, WSP Group Senior Vice President Scott Robbins said.
"You also have to have resilience,” Robbins said. "If the grid goes down, you want your buildings to still operate. You have to have a backup plan for that.”
The demands are relatively stable in biomanufacturing, where companies seeking to produce their advanced medicines in their backyard have sought large, single-story shells, such as former warehouses, to reposition.
The new market has seen ambitious ground-up campuses like King Street’s 47-acre Devens site, but even as developers are seeking to build critical biomanufacturing supply, they have formidable competition for limited land.
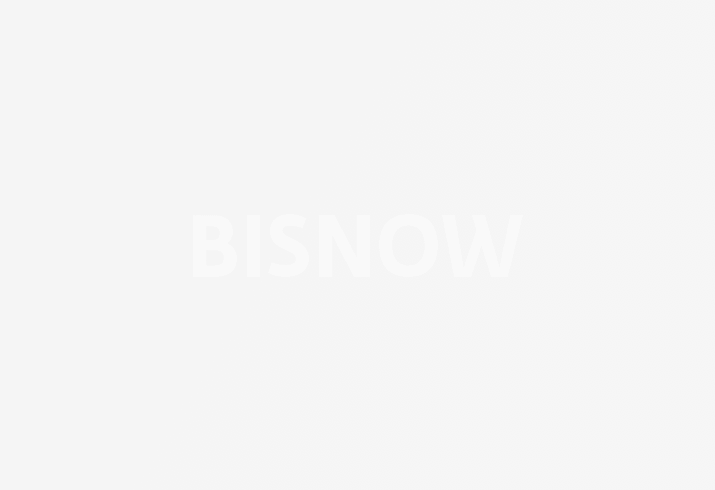
“Amazon is gobbling up so much industrial that there’s competing forces,” King Street Properties Managing Director Robert Albro said. “We’ve looked at land and we’ve looked at existing buildings where the competing use, often Amazon, is willing to pay more. There’s a dynamic there.”
Biomanufacturing requirements do appear to enjoy goodwill from communities that prefer to avoid the headaches of an e-commerce warehouse, which can bring with it increased traffic and 24-hour operations.
“E-commerce brings a lot of traffic like 18-wheelers, and those aren’t well-received,” Griffith Properties principal Marci Loeber said on the event. By building biomanufacturing, “you’re reducing traffic, you’re reducing the public, sort of, trying to appeal it. Time is money. You don’t need the parking, you don’t have the traffic. Traffic pre-Covid became an issue.”
The desire from cities is evident in the Massachusetts Biotechnology Council’s Bio Ready Communities rating, a list of 84 municipalities ranked from bronze to platinum in terms of lab development-friendly zoning, permitting and other factors. Chelmsford, a newcomer to the market, was recently elevated to platinum, while suburbs Danvers and Randolph have applications for new MassBio ratings pending, MassBio President Kendalle O'Connell said.
GMP facilities, which largely sit outside of the Interstate 495 belt approximately an hour's drive from Boston, have moved closer to the lab cluster in Cambridge but have done so in facilities rarely larger than 100K SF, even when backed by deep pockets.
Developers behind one of Boston's most sought-after sites, the 20-acre Widett Circle, are reportedly in negotiations with both Amazon and at least one biomanufacturing requirement — showing that both of the growing property types are getting more urban, more expensive and, maybe one day soon, much taller.
“Will there be multi-story biomanufacturing? Probably,” King Street's Albro said. “Someone’s going to want it desperately in an urban market, and they’ll figure out a way to do it. But you don’t see much of it right now.”