Roofing Contractors Forced To Navigate Today’s ‘Upside-Down’ Supply Chain
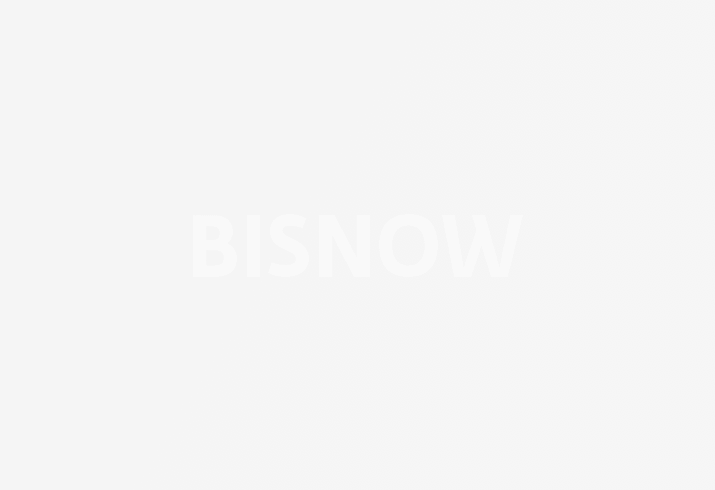
David Rabin, vice president at family-owned A-1 Roofing, has been building and fixing commercial roofs for more than 30 years. As careers go, that is plenty of time to see trends come and go. However, the past several months have brought changes to his industry that are unlike any he has ever seen.
Aside from the occasional snowstorm that might wreak havoc on the area’s low-slope commercial roofs, work for A1 and other Chicago-area roofers had been fairly predictable over the years. If A-1 needed roofing materials, such as the popular membrane thermoplastic polyolefin — known as TPO — the wait from order to delivery was typically a matter of weeks. That gave roofing contractors plenty of time to plan their work and offer customers a firm price estimate and work timetable — with minimal project delays.
But that began to change this spring, when it became clear that events taking place miles away from the Windy City were impacting the supply of roofing materials. These included Texas petrochemical plants that were knocked offline by extreme weather, compounded by a nationwide trucker shortage.
“If we order material in October, the manufacturers are telling me it will be June or July when I can have it,” Rabin said. “That's the farthest out I've ever seen anything in my life. I mean, usually it's two, three or four weeks at the most. Now, we're dealing with six or seven months.”
That delay, even though it is out of Rabin’s control, understandably doesn't always sit well with building owners. It makes life difficult for designers and engineers, too.
“We're in this really interesting kind of upside-down world now,” said Jason Wilen, a senior associate with building restoration experts Klein & Hoffman, a frequent A-1 partner. “TPO has typically been one of the most popular roof membranes, but suddenly it and other roof membranes are much more difficult to get."
The situation is so dire, in fact, that the National Roofing Contractors Association has been lobbying the federal government to step in to address what the group called “a cascading chain of events beyond the control of our industry.”
That lack of control is a major headache for companies like A-1 and Klein & Hoffman that increasingly find themselves in the uncomfortable position of explaining to clients why roof jobs probably will take longer to complete and be more costly than initially expected.
“What we struggle with most is that a lot of the roof assessments we do are performed far in advance,” said Allysia Youngquist, associate principal at Klein & Hoffman. “Typically, it's a year or two later until a client will initiate the program and then we have to tell them that costs have since risen 20% to 30% year-over-year. When you're writing an assessment in today's dollars, that cost increase has a pretty gruesome impact on your estimate.”
Supply chain issues have, of course, impacted the availability and cost of building materials other than roofing membranes, such as metal components. According to the NRCA, the cost of construction materials rose nearly 28% between April 2020 and August 2021. During the same period, the price index for contractors’ bid prices grew only 5.2%, indicating they are absorbing the bulk of the price growth themselves.
A-1 and Klein & Hoffman have been trying to help clients work around these issues by doing things like installing temporary roofs. But the companies are limited by the fact traditional roof membranes might not be available and substitutions may face challenges with code compliance or insurance company requirements. Chicago, in fact, tightened its roofing codes for factors such as wind uplift resistance just before the coronavirus pandemic hit, Wilen noted.
“That was interesting timing, where the codes became more stringent at the same time that material shortages were coming into effect,” he said. “So now we have fewer tools, but higher standards that we have to meet.”
Although building owners need to be resigned to delaying full roof replacements, contractors can still address emergency situations.
“A roofing contractor might not be able to get large quantities of insulation and other materials, but they may have small quantities on hand in their warehouse,” Wilen said. “If the immediate leak or issue can be solved and we know the rest of the roof system is in satisfactory condition, a wait-it-out strategy can work to push back full replacements until a time when materials are more available.”
As for when the supplies will become more available, observers expect shortages to continue at least through 2022. Until then, Rabin is counseling his clients to be patient.
“I tell them to get in line, that's the most important thing, because ultimately they're going to build, ultimately they're going to need a roof, and they have to get under a roof to go inside to complete their building,” he said.
This article was produced in collaboration between Studio B and Klein & Hoffman. Bisnow news staff was not involved in the production of this content.
Studio B is Bisnow’s in-house content and design studio. To learn more about how Studio B can help your team, reach out to studio@bisnow.com.