At Skender's New Modular Building Factory, Apartments Roll Off The Assembly Line Like Cars
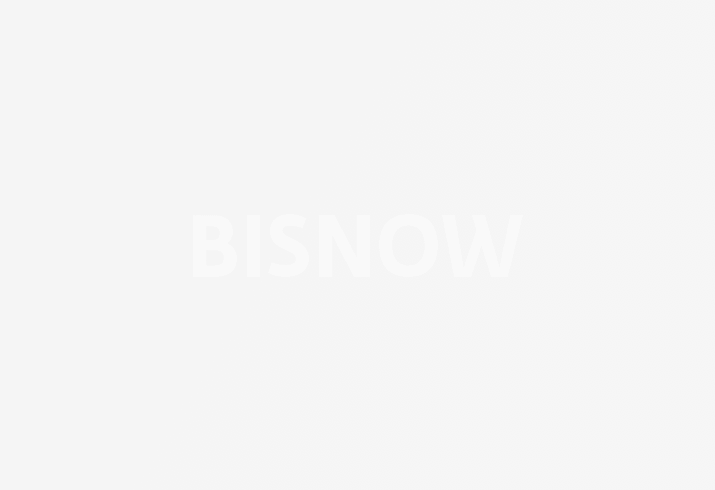
In November, the world got its first glimpse of a modular housing prototype from Skender, a Chicago-based construction firm. The module was remarkably complete. It included a kitchen, a bathroom, a sitting room and a bedroom, all within a steel frame. Its exterior, rough with insulation, matched the sparse surroundings of the as-yet empty factory around it. For a moment, it was one of a kind.
With Skender’s new manufacturing facility fully operational, dozens like it will soon start rolling off the assembly lines. On May 28, Chicago Mayor Lori Lightfoot joined Skender CEO Mark Skender and other community and business leaders for the ribbon-cutting of the new factory on Chicago’s Southwest Side.
"The new Skender advanced manufacturing facility is a win-win for Chicago, generating job growth on the Southwest side while advancing a creative solution to address the affordable housing shortage,” Lightfoot said. “We will work with residents, community leaders and developers across the city to ensure every Chicagoan has a safe and affordable place to live. The addition of new modular units will improve access to sustainable housing, prevent homelessness and ensure that as Chicago grows, all of our neighbors can afford to grow, too.”
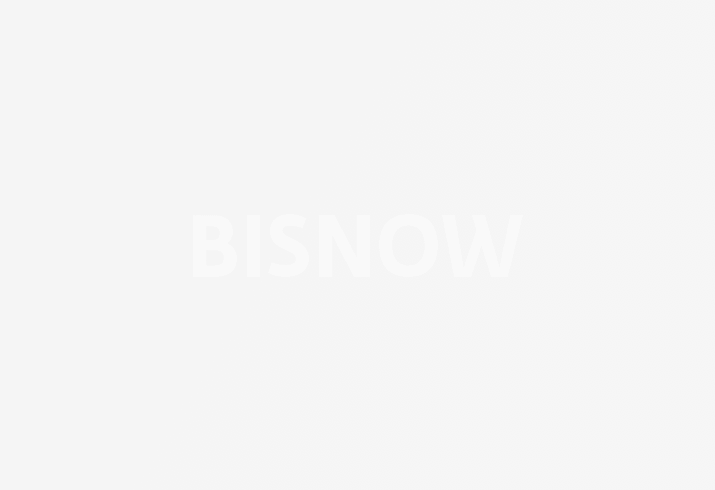
Though the factory’s first two assembly lines will reach peak productivity by July, Skender plans to triple its modular building program over the coming years.
“We have enough space at the facility for six assembly lines running simultaneously, each potentially building a different kind of modular unit,” Skender President of Manufacturing Pete Murray said. “We’re not just looking at complete structural units for multifamily housing and hospitality. The factory will also make slide-in pods, such as exam rooms for healthcare projects.”
The modular units are similar to LEGO building blocks. Once they have been built and fitted out with windows, sinks and cabinetry, they are shipped directly to a build site, where they are stacked and affixed to their neighbors.
Normally, the arduous processes of wiring, plumbing, drywalling and finishing a multifamily building would have to be done on the building site itself and would require a slew of skilled trade workers. By bringing those processes onto the factory floor, Skender estimates it can save 15% on costs compared to traditional construction, and cut timelines by around 40%.
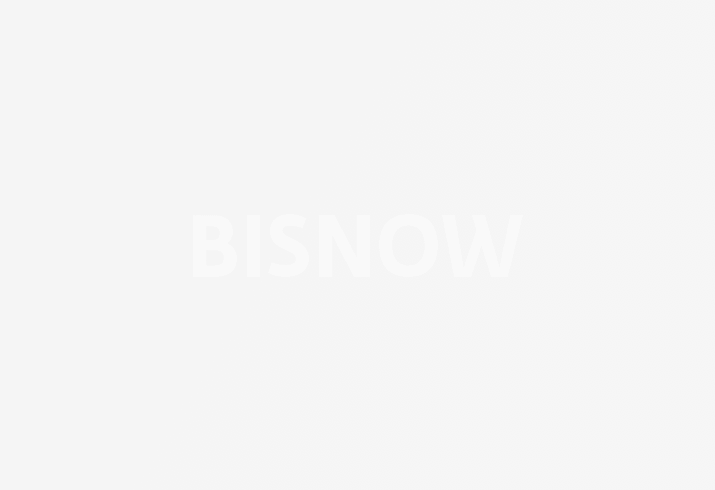
Those estimates will be put to the test as Skender begins manufacturing modules for its first project, 10 three-flat buildings for Sterling Bay. The first of these buildings will take just nine weeks to manufacture, stack and finish for occupancy, which Murray said is approximately 80% faster than a conventionally built three-flat.
Skender will also be manufacturing a seven-story, 140-unit multifamily building in Chicago’s West Loop, as well as affordable housing units for the new Garfield Green development, a mixed-income housing project in East Garfield Park. Garfield Green was the winning entry of the international C40 Cities competition, an initiative to combat climate change, and the development is led by national nonprofit Preservation Of Affordable Housing.
Once a crane lifts each module, it takes around 40 minutes to affix the unit to its neighbors and link up its utilities. If the weather holds, the 140 units should be in place in under three weeks, Murray said.
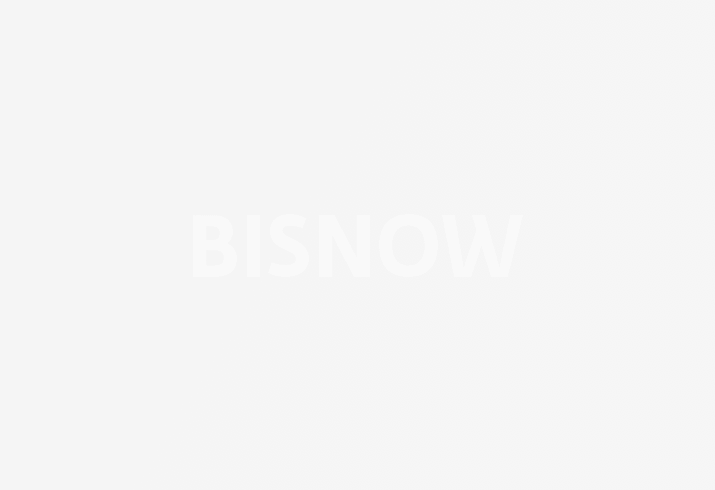
The assembly line itself consists of five different bays. In the first, Skender fits out and welds a steel skeleton for each module. The second is for installing mechanical, electrical and plumbing. Drywalling and finishes are added in the third and fourth bays, while the fifth prepares each module for transit with vibration reduction and shrink wrap.
At its outset the assembly line will be overseen by a dedicated team of assembly workers, but as Skender refines the building process and grows the number of lines, the process will become increasingly automated.
“The team that is doing the welding and the drywalling are going to become the team that oversees the automation process as we grow our modular practice,” Murray said.
Murray said the company will remain rooted in its core construction business, which includes conventional tenant interiors, healthcare, office, hospitality and multifamily. He added that building out the team for the modular factory has helped Skender grow its core strengths as a design-build firm.
“Especially when it comes to adding new technologies, modular can help developers stay on the cutting edge,” Murray said. “Our goal is to give developers as many options as possible.”
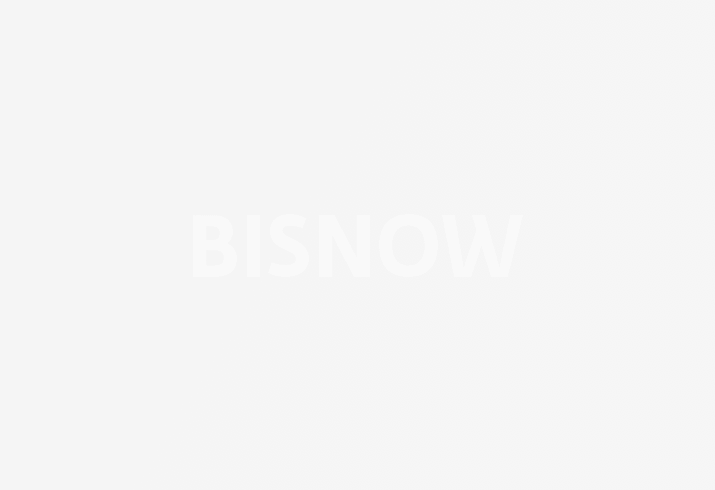
In preparation for its modular offering, the company last year acquired Ingenious Architecture, a design team that Murray said will bring creativity and expertise to modular and traditional construction practices.
“Everyone at Skender is so proud of the modular product, and it really is something unique and novel,” Murray said. “This is the culmination of a lot of work and investment. I’ve been in the manufacturing industry for 25 years, and for me, the factory is one of the most exciting projects I’ve worked on.”
This feature was produced in collaboration between Bisnow Branded Content and Skender. Bisnow news staff was not involved in the production of this content.