Beyond The Pane: The Engineer Behind Some Of The U.S.’ Most Impressive Glass Structures
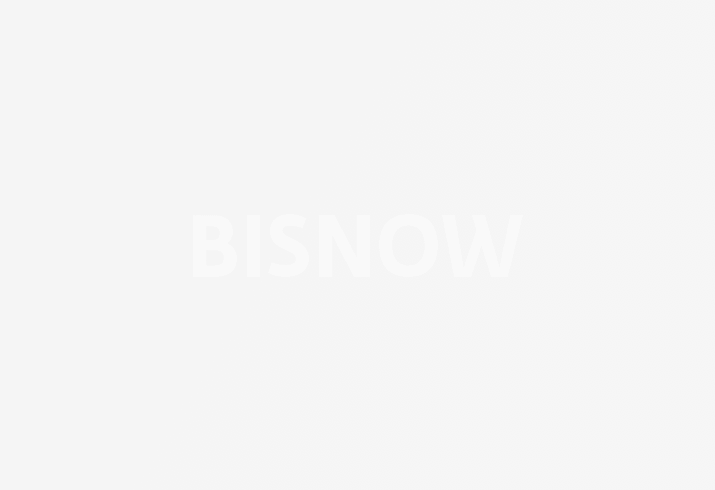
A glass walkway suspended hundreds of feet above the ground. Cylindrical aquarium viewing walls made of glass and holding back tons of water. Glass staircases that appear to float in midair.
If you're an architect or a designer planning something ambitious with glass, your first call very well might be to Terry McDonnell.
Though McDonnell has engineered plenty of well-known skyscrapers, train stations and amusement parks, he's made a niche for himself in the world of structural glass. He's worked on iconic structures such as Chicago's Willis Tower and Seattle's Space Needle.
When architects imagine innovative ways to use one of the most beautiful and versatile building materials available to them, McDonnell helps make their ideas real.
“I enjoy structural engineering because I get to tell people, ‘Yes, you can do that,’ about some of their wildest dreams,” said McDonnell, who recently joined the structural engineering and building envelope teams at Chicago-based firm Klein & Hoffman. “Every day, we work diligently and responsibly to figure out how to get project solutions to 'yes.'”
Bisnow chatted with McDonnell about some of his iconic projects, what he’s working on now and the role glass will play in the future.
Bisnow: How did you become a nationally recognized expert on glass? Did you originally set out to master this one material?
Terry McDonnell: It was a combination of fortuitous coincidence, a gradual building from one opportunity to another and my constant interest in the material. My first glass project as the engineering lead was the Ledge at Willis Tower. The Ledge is a set of four glass rooms projecting outward from the side of a skyscraper over 1,300 feet above the ground.
I remember on that project, our team performed calculations using the national building codes from four other countries, because the U.S. did not have a standard for structural glass walkways at that time. My eyes were further opened during some of the testing we performed when I saw the high strength glass could achieve with some sophisticated design and fabrication methods.
Three or four similar glass walkway projects later, I was introduced to a committee that is preparing a comprehensive structural glass standard by a colleague. This group is a subcommittee within ASTM, the American Standards of Testing and Materials International. I have been actively participating in this committee since 2014.
This participation opened up a communication to all sorts of clients that wanted to incorporate glass in thrill-seeking structures or study glass configurations resisting extreme loading conditions.
I became a person that architects, contractors, attorneys, universities and even other engineers contact to responsibly evaluate glass challenges incorporate glass into more heroic walkways, balustrades, staircases, entire entryways, really anything you can imagine.
Bisnow: Would you say you have a favorite project that you’ve worked on?
McDonnell: One of my favorites was a grand entryway at 160 Elgin St. in Ottawa. It's a three-story insulated, curving, glass fin wall that comprises the entire east elevation of the building. At the third level, the insulated glass transitions to a laminated glass windscreen for a fully occupied rooftop.
The architect challenged us to find glass manufacturers and fabricators that could deliver extra-large glass panels that would be heat-treated, laminated on both sides, insulated, curved, accept a low-emissivity coating and accept a silk-screen frit pattern.
This amount of post-processing to float glass is unique and if one is not diligent, can quickly elongate the construction schedule or result in undesirable quality. We did enough pre-planning to support both the architect and building owner so they had a choice between supply chains that could deliver for the project.
Another memorable experience was the work I did on Tilt, which is the John Hancock Center's response to the Ledge. Tilt is as much an amusement park ride as it is a structure. My role included reviewing and rethinking the fundamentals of that project so improvements in the kinetic parts of the structure and the glass makeup could be realized by the design team.
Bisnow: So you just joined Klein & Hoffman a few months ago. What are you looking forward to working on?
McDonnell: We're working on a few full-scale glass wall replacements at high-end office complexes within the Chicago area. I'm also supporting efforts for the Belle Isle Aquarium in Detroit to create larger and more unique viewing areas of their aquarium tanks.
I have also started working on more traditional building renovation and repair projects with clients that I have known for a long time. It does not matter if the project involves glass or any other building material, we are here to solve problems, and the more challenging the problem, the more suited we are to support that client.
Finally, I am continuing to work with the ASTM structural glass subcommittee to complete the standard we have been working on for so long. The committee's goal is to provide the building community with transparent metrics, no pun intended, that can be relied upon when utilizing glass as a structural building material.
Bisnow: What are you hoping to get out of your work with ASTM?
McDonnell: We hope these standards will provide guidance for those who want to explore using glass in new and interesting ways. When there are more successful projects using structural glass, we hope everyone will become comfortable with the material.
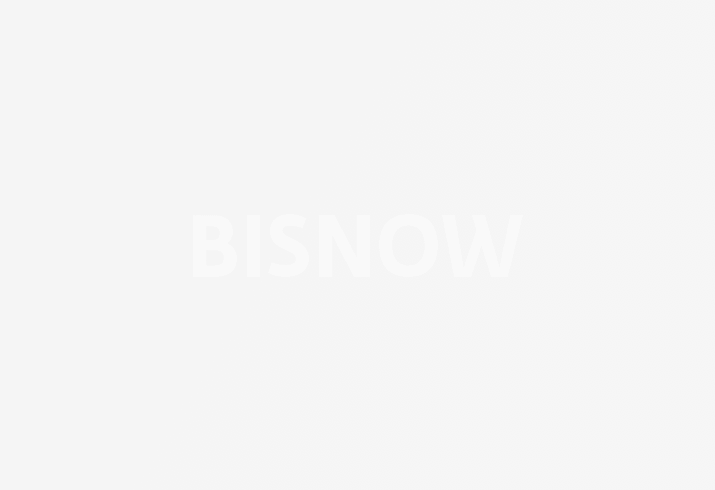
Bisnow: What still excites you about what you do?
McDonnell: The people I work with every day. From the grateful clients, to the chemists at material laboratories, to all my new colleagues at Klein & Hoffman. I am blessed to meet new people every week and discuss their ideas, goals and dreams. When those discussions are compatible, we get to work together for weeks, sometimes years, on a path that will turn their ideas into physical forms, or fix the latest attempt made at a new unproven or unreliable concept.
I also think that glass is at a point where it may experience a technological leap as a material. For instance, I have been in groups starting to discuss how can we use borosilicate glass, trade name Pyrex, or alkali-aluminosilicate glass, known as gorilla glass in fire protection and structural applications. We also discuss how we can use interlayers and films to reduce the likelihood of fractures. There are so many things we can use to enhance glass as a material within our problem-solving toolkits. I'm glad I'm with K&H to be a part of these opportunities.
Bisnow: In the design world, are there prejudices about glass that you’re trying to dispel?
McDonnell: Not only are there prejudices, sometimes there is fear. With other materials, a failure might be preceded by a large deflection, whereas with glass, the failure is sudden and often accompanied by a complete loss of load carrying capacity. I cannot change this basic material behavior, but I can provide designs that influence when the failure may take place and limit the failure to only a portion of the design.
By working with sophisticated fabricators and material suppliers and by using laminations, appropriate analysis, and other approaches within engineering mechanics, I can achieve glass-based systems that will perform similarly, if not as reliable, as other structural building materials. Over time, I hope my work and the ASTM committee's work will provide both more comfort, and more economy so an idea today will become a built success tomorrow.
Part of my job on this committee is to prepare a commentary to help others understand the background of the standard. The committee hopes that when the standard is published it will go a long way toward creating greater understanding of glass as a building material.
This feature was produced in collaboration between the Bisnow Branded Content Studio and Klein & Hoffman. Bisnow news staff was not involved in the production of this content.