Building A Sonic Sanctuary: Conquering The Obstacles Of Studio Construction
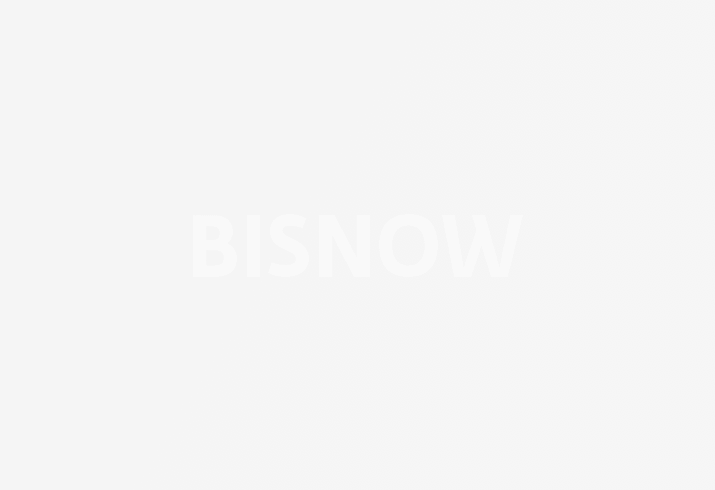
The studios where music, movies, podcasts and news broadcasts are produced come in different shapes and sizes, but they all have one thing in common — they must be meticulously soundproofed. The slightest interference from outside noise can render an entire recording session unusable, wasting time and money and leading to costly delays.
Building these studios requires a strong knowledge of potential challenges and a team with the experience and skills to overcome them. Clune Construction, a Chicago-based general contracting firm with offices in Dallas, Los Angeles, New York, Phoenix, San Francisco and Washington, D.C., has decades of experience constructing these intricate projects and understands what it takes to create these unique spaces.
“You need to have the right team who understands how these complex rooms come together and can work with the client to meet their design requirements,” said Clune Project Executive and Vice President Paul Holzschuh, who has more than 20 years of studio construction experience. “There are several do’s and don’ts that go into these projects. It all comes down to picking the right team of craftsmen, and Clune knows what to look for.”
Holzschuh said that building a studio is often times referred to as building a “room within a room.” The team first starts with the framing and then hangs multiple layers of drywall on one side to isolate the studio and eliminate the transfer of any type of noise. This type of construction includes a critical air gap between the two sets of walls that aren't connected to each other by any materials to ensure no external noise is transferred. As a result, installing electrical and HVAC features that these rooms require can be particularly challenging.
Additionally, every aspect of the project, from the drywall to the doors, needs to be carefully selected with the space’s unique use in mind. For example, Holzschuh said Clune regularly uses acoustical doors that are specified to achieve a certain sound transmission class rating. These doors are installed on cam lift hinges that help create an acoustical seal of the doors when they are closed, so when someone enters the studio, it is as though they are entering an isolation tank.
The team also utilizes materials such as isolated concrete slabs, fabric panels and insulation to create the ideal recording space. How much of each material is used varies greatly based on each space’s unique design, he said.
“We like to be a true partner with designers,” Holzschuh said. “This way we can share our vast experience in this sector with them and involve our trade partners to help think outside the box. This helps us solve challenges and ensure that any modifications we make do not impact the design or the performance of the room.”
For one high-profile Los Angeles-based project, Clune conducted rattle tests. A consultant was brought in, and low bass frequencies were played within the space. The consultant would then hang a small flag whenever they detected rattling. The team then went in to determine the source of the vibration, be it ductwork, framing materials or conduit, and make adjustments accordingly. This process was repeated until the space was rattle-free.
“This happened in multiple phases,” Holzschuh said. “We would build something, they would do some tests, highlight some things and then we'd address them. The next week, we would build some more, and they would test again. This was a weekly cycle that went on three or four times. It was an amazing process that highlighted some interesting issues that we would never need to address on more traditional projects.”
Clune Project Manager Kevin Steger spoke about the firm's construction of the Marquee Sports Studio in Chicago, the exclusive local television station for the Chicago Cubs. This project faced several challenges. Along with being in the heart of Chicago’s bustling Wrigleyville, just steps from all the noise and crowds of Wrigley Field, it was located next to an active fire station. Additionally, the building had an existing steel infrastructure that the team had to work around, and several steel posts and outriggers had to be incorporated into the studio’s design.
“We had to incorporate the sound levels of the sirens that would be within 5 feet of the building,” Steger said. “We built a sound wall on the outside of the perimeter of the studio, and there were operable windows that we had to seal shut.”
The team put sound blankets on the walls for additional sound reduction and then sprayed them with K-13 insulation for more acoustical treatment. The final product consisted of several layers of sound attenuation, including a roof deck and a sound ceiling with isolation clips to limit any noise from above. A unistrut system housed all of the power and data for the cameras and a lighting grid where the studio’s lighting could be housed.
“In studios, it gets very hot because there is so much light,” Steger said. “On top of that, we’re building a soundproof box, so no air can escape. Getting the air in and out of that space is critical to be able to condition it properly. This is why we added a rooftop unit as the studio’s dedicated air service.”
Steger said the project’s sound consultant was very concerned that the outside noise from the neighborhood would leak into the studio. While they were inspecting the space, however, the fire station got a call, and as the trucks drove by, the studio remained silent.
Holzschuh said that in the end, while the projects can be complex, their success boils down to having the right people by your side.
“Clune’s been doing these projects since we opened our doors, and we have the right team to overcome whatever challenges come our way.”
This article was produced in collaboration between Clune Construction and Studio B. Bisnow news staff was not involved in the production of this content.
Studio B is Bisnow’s in-house content and design studio. To learn more about how Studio B can help your team, reach out to studio@bisnow.com.