Keeping Life Sciences Sites — And Tenants — Safe Through Collaboration And Attention To Detail
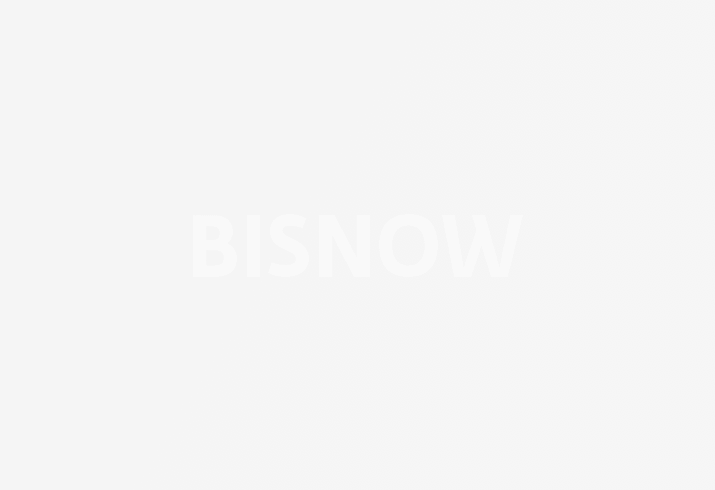
Life sciences construction and redevelopment projects are among the most complex in commercial real estate. Unlike traditional office projects that are focused primarily on the best use of space and boosting tenant satisfaction, building a lab requires a host of unique design, equipment and safety considerations.
This is why it is important to partner with a general contracting firm that understands the particular challenges of life sciences construction and the communication and collaboration needed to help them succeed.
“With life sciences construction, each job is unique,” said Andy Gibbons, project executive at Chicago-based contractor Leopardo Construction. “We expect our team members to truly understand owners and what's important to them because ultimately it’s about building the project collectively as a team.”
Leopardo used this collaborative approach for a 25K SF life sciences expansion project that was completed in April. Valent Biosciences came to Leopardo over a year ago with the plan to expand its life sciences campus in Libertyville, Illinois.
The biotech company knew that it could trust Leopardo with this complex project because it had worked with the team in the past on a 70K SF laboratory and office build-out. This massive lab space featured fume hoods, exhaust devices, lab fixtures and casework, biological safety cabinets, sterilizers, drying racks and more, the installation of which was all facilitated by Leopardo.
Leopardo also had preexisting relationships with the current project’s architect and engineering firms.
“We have extensive experience with life sciences projects that we drew upon to help this particular project succeed, and Valent wanted to continue to build on our past relationship,” Leopardo Senior Project Manager Camille Trausch said.
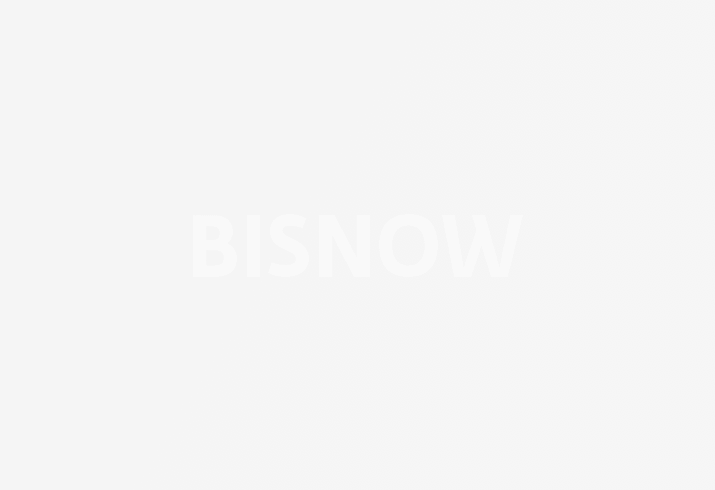
There were several unique challenges to this project that the Leopardo team had to tackle, including ensuring that the expansion matched the existing facility. This required procuring specific building materials, a process that has become increasingly complex because of pandemic-driven supply chain disruptions and long lead times. By working with its estimating and pre-construction teams and staying in regular contact with all project stakeholders, Leopardo was able to get materials ordered ahead of time and within the client’s budget, Trausch said.
Additionally, Leopardo had to perform the expansion work with limited disruption to the current tenants, including those who do not work with Valent.
“We communicated a daily plan with the building owners and stakeholders to ensure that everyone stayed happy — including tenants Valent had no involvement with,” Gibbons said. “A little bit of extra communication and collaboration goes a long way in these situations.”
While all life sciences projects have unique safety considerations due to the nature of lab work and the equipment they require, the Leopardo team had to be especially careful on this site to protect the current tenants.
The Leopardo safety team made weekly visits to the site, as they do with all the company’s projects, and sent a report detailing any of the low, medium and high-security risks that needed to be addressed. Meanwhile, the on-site team held daily safety meetings and developed a site-specific safety plan and utilized weekly toolbox talks that were used to ensure everyone was secure, Trausch said.
Gibbons said that when it comes to safety, it all comes down to proper planning. This is how Leopardo earned its record-low experience modification rate, which is a data-driven calculation used to determine an insurance premium for construction companies.
“With a multi-tenant facility, our top goal is always public safety, and keeping both the tenants and the people passing by the facility as safe as possible,” Gibbons said. “We did this with public barriers, clear signage and other markers to make sure people stayed out of the construction zone.”
Leopardo’s self-performance team performed the following scope of work: demolition, rough and finish carpentry, framing, drywall, taping and painting. Trausch said that Leopardo is uniquely positioned to handle these types of life sciences projects, which is why clients continue to trust them to deliver the work on schedule and within budget.
“Our self-perform teams have worked in both the Valent space and broader facility itself in the past,” she said. "We find having self-perform crews on site greatly enhances the project including quality of work, increased safety measures, and providing schedule flexibility. Our communication and attention to detail drive positive results.”
This article was produced in collaboration between Leopardo and Studio B. Bisnow news staff was not involved in the production of this content.
Studio B is Bisnow’s in-house content and design studio. To learn more about how Studio B can help your team, reach out to studio@bisnow.com.