'The Hysteria Is Real': Developers Say Creativity Is King Amid Ongoing Supply Chain Woes
It is no secret that Dallas-Fort Worth’s commercial real estate market is booming. But it would likely boom even louder if it weren’t for two pesky issues stalling momentum in the Metroplex and beyond: supply chain cramps and skilled labor shortages.
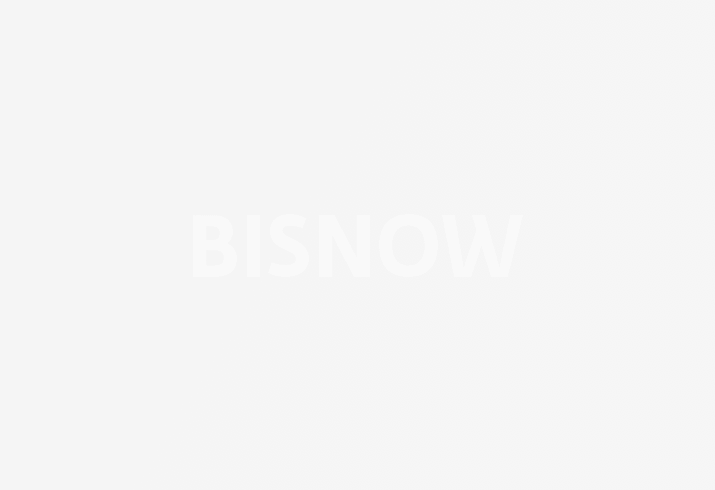
The show must go on, so developers across asset classes have discovered inventive ways to circumvent these problems, according to panelists at Bisnow’s Dallas State of the Market Feb. 25.
“The supply chain hysteria is real,” said Robert Young Jr., executive managing director of Weitzman. “It’s not just steel, it’s not just hard goods material — it’s the cup that handles that beverage that the customer wants.”
Katie Willis, senior vice president and construction partner for multifamily developer JPI, said her company has no issue with paying a premium on materials when they can get them. But with product orders stretching into 2023, JPI has turned to direct purchasing and sourcing to bypass long lead times.
“We had several buildings last year that we couldn’t turn over because they didn’t have paint,” she said. “So it’s been very eye-opening and very surprising.”
One of the ways developers are looking to deliver projects faster is by sourcing more materials domestically. Prior to the pandemic, many of the materials used by Thakkar Developments came from China, but that has changed as developers look to minimize scheduling delays.
“We look very closely to American-manufactured products, because time is of the essence,” CEO Poorvesh Thakkar said. “If [projects are] not done on time, we lose a lot of money in the project. So time is a very important, critical aspect.”
Steven Upchurch, principal and co-managing director at Gensler, said American manufacturers are responding accordingly.
“They've really stepped up the game [in terms of] what types of products they're delivering to our designers and architects for selection and substitution,” he said. “We're seeing a lot of substitutions on products … so they’re having to act fast, and the easiest, quickest way to get it here is from the U.S.”
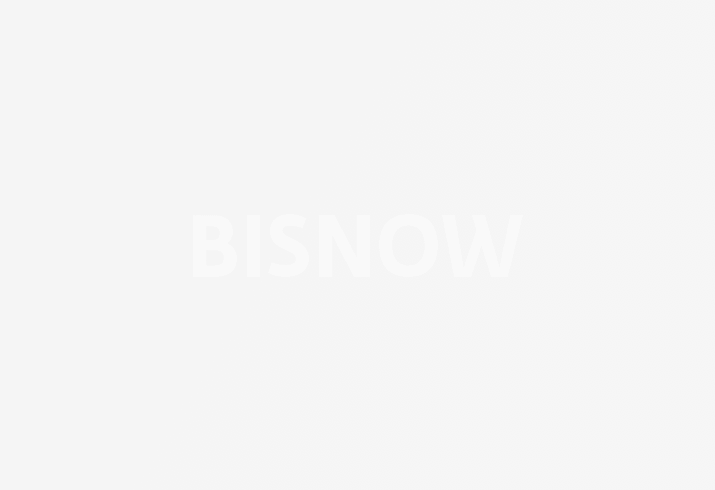
Substitutions have become increasingly prevalent as developers grapple with the surge in prices and lead times on commonly used materials. Kevin Kramer, project executive at DPR Construction, said his company recently substituted a steel frame with a concrete frame on a six-story office building that Billingsley Co. is developing in Cypress Waters.
“Just because we could do it faster … and save a couple months on the schedule and delivery … it ended up being a wash on their costs,” he said.
The number of laborers has also fallen short of demand, making it even more difficult for developers to deliver products in a timely manner. In response, many in the construction industry are turning to prefabrication. Kramer said cutting down on on-site labor has helped his DPR save time and money.
“It's even more important to work with contractors early on, and to the extent that you can incorporate prefabrication [and] modularize as much as you can — taking that labor off the job site is just hugely critical,” he said.
Gensler used modular construction during a recent project that provided a 600-room hospitality complex for American Airlines employees. Upchurch said the pandemic briefly paused construction, but once it resumed the prefabricated pods were on-site and ready to be installed.
“We're seeing a lot of our clients coming to us, especially in hospitality, looking for modularization wherever we can create it for their projects and help save on the labor on-site,” he said.
Demand issues will likely be exacerbated by the recent passage of the federal government's infrastructure bill, which will sink trillions of dollars into the nation’s roads and bridges, said Heath Johnson, senior vice president of Cousins Properties. There are only so many contractors and materials to go around.
“I don't know how that plays out,” he said. “But that's going to be, in my view, just more upward pressure on pricing.”
Despite all of these difficulties, the shortage of materials and workers appears to have only slightly dented DFW’s thriving pipeline of projects. JPI, for example, is expected to have more than 8,000 apartment units under construction this year.
“We have more capital investors than we have opportunities for them,” Willis said. “So that's a great position, but it's also driving us to want to go faster, quicker [in terms of] how much more product we can put on the ground.”