3D Printing Poses Real Threat To Supply Chain And The Real Estate That Supports It
With a simple press of a button, one of Whitebox Real Estate co-founder and President Grant Pruitt's foreign-based clients can manufacture a product thousands of miles away in the U.S. using 3D printing technology.
That may be bad news for industrial real estate, particularly along the coasts.
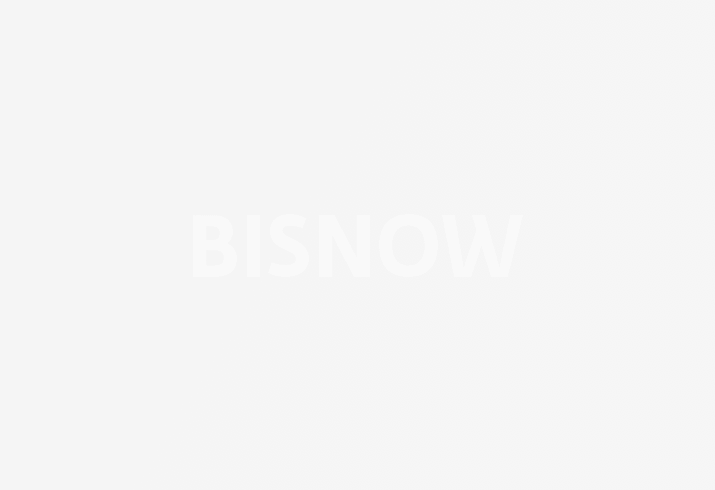
Pruitt's client is an adopter of 3D printing, a solution that allows manufacturers in any part of the world to use computer-assisted technologies to design a product and then instruct remote 3D printing machines to build it out from raw materials.
This is a game-changer, giving foreign manufacturers the potential to bypass arduous import processes by digitally transmitting their designs to printers on American soil.
But for industrial and logistics-centric real estate professionals, 3D printing, along with artificial intelligence and autonomous logistics solutions, poses a real threat to the old world order of supply chain management and the real estate that supports it.
"The biggest disruption is going to be in the demand for industrial space, and I venture [there will be] a lack of demand in some of the traditional markets on the coast," Pruitt said.
Pruitt doesn't see 3D printing disrupting supply chains or real estate for another five to 10 years. But, he said, with fewer products having to ship through U.S. seaports, coastal cities will lose their competitive advantage when it comes to preferred locations for warehouses and supply-chain related facilities.
Pruitt, who has watched at least one foreign client choose DFW for its 3D printing location, believes any technology that removes international shipping from the equation gives Texas and other central U.S. markets a leg up on the competition.
"I think we are just starting to see the effects of the disruption right now, and I see it as a positive in that it greatly increases the demand for industrial space in North Texas because we are smack dab in the center of the country," Pruitt said.
And from smack dab in the middle of the country, 3D printed projects have about an equal distance to travel to reach every part of the U.S. — a selling factor that could become more pronounced if 3D printing allows more products to bypass the import process at coastal areas altogether.
Still, demand for industrial space is not going away because of new technology, Pruitt said.
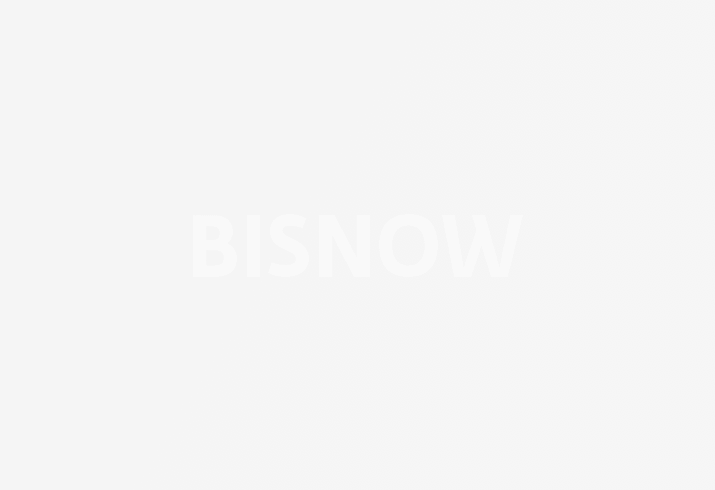
"I think it's going to increase the need for warehouse space just like Amazon increased the need for warehouse space," he said.
"I don't know how [the warehouse] is going to look in the future, because you may go to a 'printing facility' that's a printing facility/distribution warehouse facility, and it's going to be filled with printers on one side and then have outbound inventory racked and stacked on the other side."
What is expected to change more rapidly as companies rely more on 3D printers, warehouse robots and artificial intelligence is the type of CRE industrial product demanded by tenants, Cushman & Wakefield said in a new report titled Tech Disruptors and the Supply Chain.
"Clearer differentiations in asset quality are likely to emerge as some technologies — such as advanced automation/robotics — require higher ceilings and very flat floors," according to Cushman & Wakefield.
Pruitt agrees that robots, 3D printers and other AI technologies in the logistics space will force industrial space designers to change their configurations in the coming decades.
"They are talking about the flatter surfaces and higher clear heights because with a robotic picking system, you can go higher and you can get narrower on the racks [when stacking], but in order to guide those systems, you are going to need a flat floor," Pruitt said.
The big question is not whether the market has industrial space, but whether the current inventory has the right amenities and configurations for these advanced technologies.
Right now, not so much.
Cushman & Wakefield reported half of the industrial inventory developed to support U.S. logistics comes with clear heights under 28 feet even though advanced automation and robotics generally require clear heights in the 32-foot to 36-foot range. Cushman puts the ideal warehouse clear height in the 36-foot to 40-foot range to avoid obsolescence.
The ideal industrial building of the future also includes 5G connectivity, thicker load-bearing walls, higher power offerings and wider columns and bay spacing, Cushman said.