‘The Possibilities Are Endless’: Building Momentum For A Fast-Evolving Life Sciences Industry In DFW
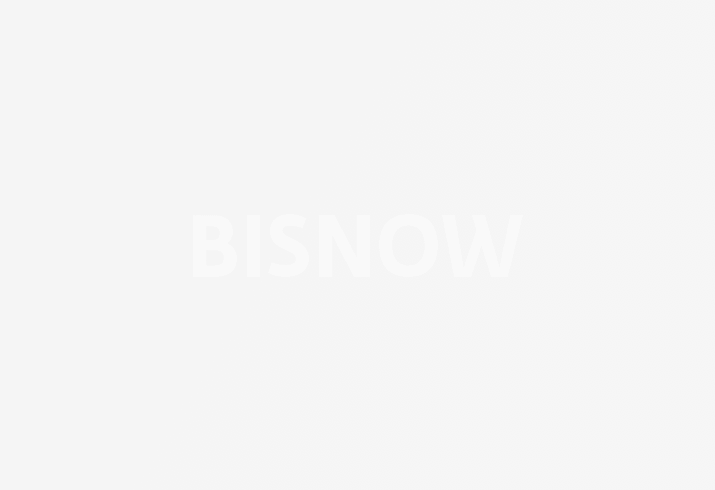
Texas is one of the leading biotech and life sciences states in the U.S., with a growing workforce of more than 116,000 employees at 7,462 companies. The Dallas-Fort Worth area, in particular, employs 26,000 people in this sector, an increase of more than 17% since 2019.
Commercial contractor DPR Construction, which has more than a decade of experience building in the DFW area, sees the region’s potential and is optimistic about its impact on the life sciences industry.
“As one of the leaders in staying connected to the evolving complexities of this highly technical industry, we’re excited to see DFW emerge as the next big hub,” DPR Preconstruction Lead Dan Seiler said.
Seiler brought his expertise and observations to Bisnow's Future of DFW Life Sciences Summit at the Texas Research Quarter innovation district in Plano on Aug. 27. He was among panelists discussing design and construction trends in the life sciences sector.
Bisnow spoke with Seiler about those trends in DFW, what to consider before designing life sciences facilities and how DPR is looking to the future.
Bisnow: What are some life sciences trends you're seeing in DFW?
Seiler: Companies need amenity-rich spaces on campuses that can compete with the tech sector to attract top talent.
Besides cutting-edge research and manufacturing areas, we are seeing designs for facilities including employee wellness additions like gyms, cafeterias, dynamic collaboration spaces and outdoor terraces.
Another big trend is the implementation of sustainability measures as many established biopharma companies need to reflect their corporate sustainability goals in the design and construction of their facilities.
Bisnow: What are key things to consider before designing and constructing life sciences facilities, and why has DFW become a prime location?
Seiler: A significant consideration is location because different county zoning requirements and permitting timelines can result in challenges in speed-to-market goals as well as power supply to the site.
The power density for life sciences facilities can be twice or more than that of a typical commercial office building. If the site doesn’t have adequate power, the timing to get what is needed to be delivered can impact the construction schedule.
Some of these challenges can work to DFW’s advantage when attracting companies to the area. For example, we had a client relocate their project to the DFW area specifically because of the municipality's commitment to expediting the zoning and permitting processes. Moreover, because DFW has been strong in development over the past years, there is also the opportunity to convert existing inventory that could be a great candidate for office-to-lab or [Current Good Manufacturing Practice] conversion.
DPR is also highly connected within a local network of industry-experienced service providers and partners that can be leveraged to streamline the delivery of life sciences facilities.
Bisnow: What projects are on the horizon for DPR that will meet the unique demands of life sciences tenants?
Seiler: We have a couple of office-to-lab conversion projects in the queue with confidential clients. They include augmenting the existing power, structural retrofit to accommodate the increased live load demand associated with R&D labs and enhancing the mechanical systems to meet the needs of wet lab users.
We are also looking into ways that prefabrication can improve these projects to benefit speed-to-market as well as improve quality, safety and man hours in a labor-demand market, by constructing key elements off-site in a controlled environment and installing more efficiently.
Bisnow: As the life sciences sector evolves in DFW, how will DPR Construction continue to stay ahead of the game?
Seiler: One of the biggest challenges we all are facing in the biopharma industry is finding ways to get that new drug or product to the market and customers faster. We’ve learned that sometimes, while the technology and the innovation are there, the process can still take a long time.
I’m confident that DPR’s extensive expertise, in collaboration with supply chain partners, can streamline a typically long procurement process to get facilities up and running faster. Using our existing relationships and data, we’re focusing on constantly improving our approach to supply chain management, which we believe will be a driver for allowing new biotechnology breakthroughs to be more accessible to patients nationwide.
I believe that the possibilities are endless in Texas. We have everything we need to be the next biopharma hub in the U.S., and DPR is partnering with the right players to make that goal successful, including our economic development groups, industry organizations like BioNTX and specialized design and construction partners throughout North Texas.
Bisnow: What inspired you to attend Bisnow’s DFW Future of Life Sciences Summit?
Seiler: While at DPR we know that it takes a technical builder to deliver a best-in-class biopharma facility, the work also calls for, beyond that, the significant collaboration between all entities, including in the Texas life sciences ecosystem. That includes customers, designers, service providers, investors, educational institutions, economic lenders and industry organizations.
The summit [allows] the companies representing all these facets of the industry to connect and learn about what’s next in the building and development of best-in-class life sciences facilities, and most importantly, drive the industry forward together.
This article was produced in collaboration between Studio B and DPR Construction. Bisnow news staff was not involved in the production of this content.
Studio B is Bisnow’s in-house content and design studio. To learn more about how Studio B can help your team, reach out to studio@bisnow.com.