Assembly Lines Could Be Key To Housing Affordability
As developer Adam Berger was striking out on his own several years ago, he was looking for a niche to fill. He was acutely aware that metro Denver has a severe lack of housing affordability and attainability, so he set out to solve the problem through developing a modular housing product.
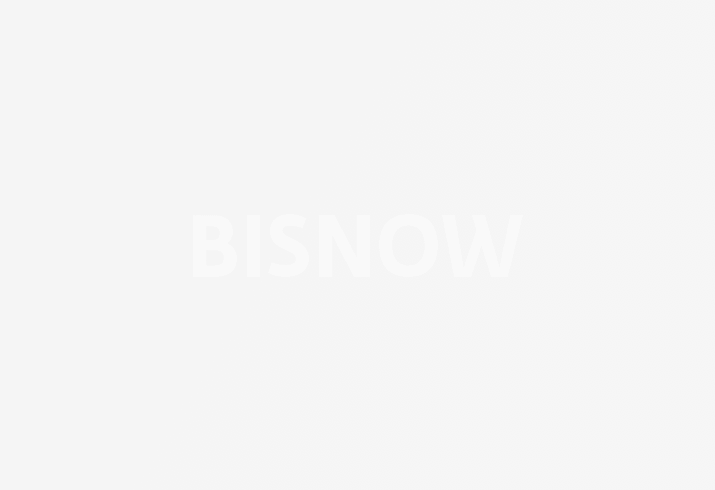
“I had seen modular being applied in different markets and wondered why it wasn’t being applied in the urban metro market,” said Berger, who will be a panelist at Bisnow’s The Denver Disruption: Future of CRE Tech event Nov. 14.
Berger, founder of Adam Berger Development, didn’t let the generally accepted maxim that modular housing should be dedicated to low-income or rural markets stop him. Instead, he started searching for infill sites to build modular duplexes to prove the product would be attractive to everyone searching for a house.
But first, he had to design an appealing product for an infill market.
“There wasn’t any good design out there because no one was doing it,” Berger said. “I studied what was going on in Europe because they’re actually doing it there.”
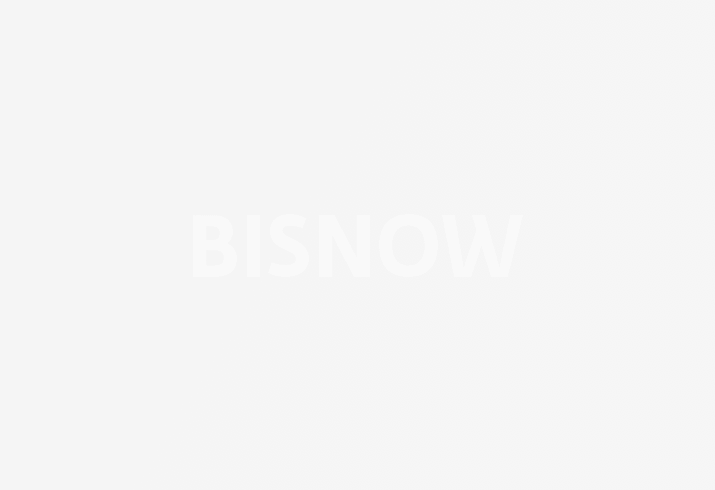
So far, Berger has built one duplex using modular technology — the first unit sold within five days. Now, Berger has a site near the light-rail station in Lakewood under contract where he plans to build four more duplexes. He is also designing townhome products, which he is planning as both for-sale and rental units.
The technology to build modular structures has existed for decades, Berger said, but it has only been applied to the low end of the market. He had to find a manufacturer who was willing to build the product he had in mind.
“I had to design it, and not every manufacturer is interested in building this kind of product,” Berger said. “Their wheelhouse is building a double-wide in a rural setting. I had to find someone interested in the infill market.”
Berger is talking with nonprofit organizations that focus on affordable housing to determine their interest in modular products. He plans to try using conventional financing to build them so he can deliver the units faster than if he were to rely on the grants and other funding available to affordable housing projects.
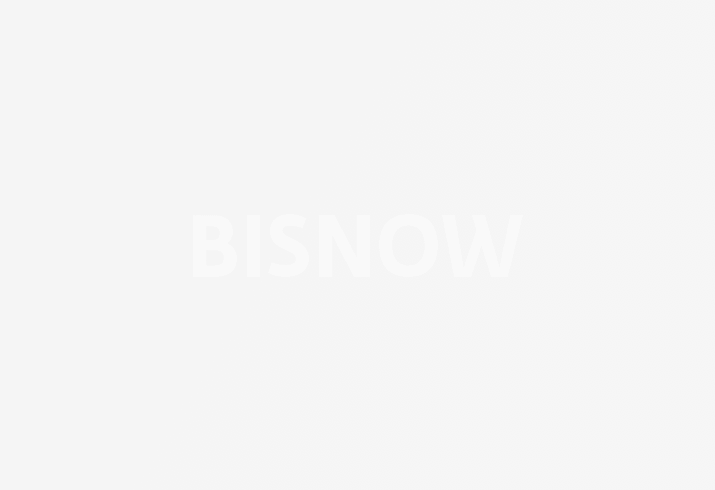
Building modular homes is faster than building traditional stick-built houses, and Berger said metro Denver’s lack of skilled labor is not as much of an issue as it is for homebuilders, even though they benefit from economies of scale.
“If you’ve got a large homebuilder that’s building 50 to 100 homes at a time, that’s 50 homes to frame and 50 homes to drywall,” Berger said. “You’re creating an on-site assembly line that’s subject to weather.
“The other way to do it is to create an assembly line off-site, which is what modular construction is. First they build the floor, then the walls, then the electrical. As it moves down the assembly line, they’re adding all the different components of the home to a box. It’s in a controlled environment. You basically have salaried employees working for you and not moving from job to job.”
Hear more from Berger and others who are changing the way properties are built, shared and connected at The Denver Disruption: Future of CRE Tech event Nov. 14 at the Hilton Denver City Center.