No Quick Fix: Construction Companies Improve Employee Standards And Go Modular To Fight Labor Crisis
The construction industry faces a significant shortage in the workforce. Simply, there is more work than there are skilled laborers.
In a recent survey by the Associated General Contractors of America, 76% of respondents said their firms plan to hire more hourly craft workers in the next year. However, 80% of the firms noted trouble filling the positions.
"In the U.S., and in Houston, there are more job openings than people looking for jobs," Construction Career Collaborative Executive Director Chuck Gremillion said. "We have to compete for this talent."
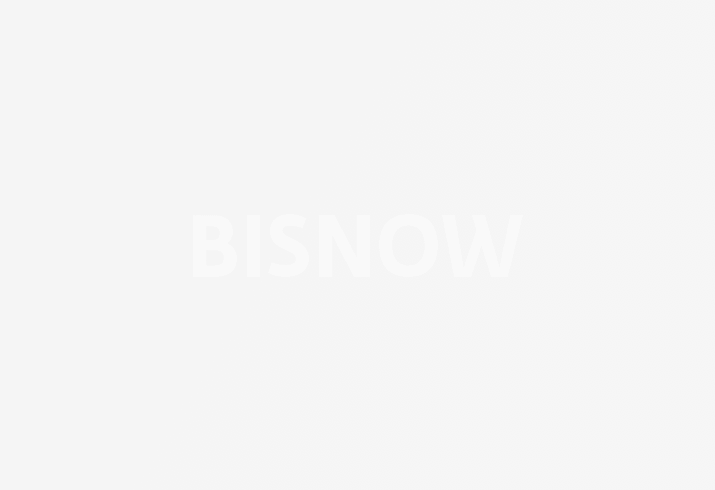
In Houston, the issue is exacerbated due to the strong local economy and population growth that is accelerating the construction pipeline. The work isn't slowing down, and the buildings still need to be completed.
There is no quick solution to the construction worker shortage, Gremillion said.
Houston-based construction companies are joining collaborative training and workforce alliances and incorporating innovative new technologies to combat the industry's labor shortage. Together, the initiatives strengthen the industry by creating a sustainable workforce and supporting ancillary systems like prefabricated material construction.
Learn more about how Houston companies plan to take on development while tackling the construction labor shortage at Bisnow's Houston 2019 Forecast on Nov. 27.
Set Higher Standards
In the face of a depleted workforce and rising construction costs, a segment of the Houston construction industry has doubled down on enhancing the quality of employees.
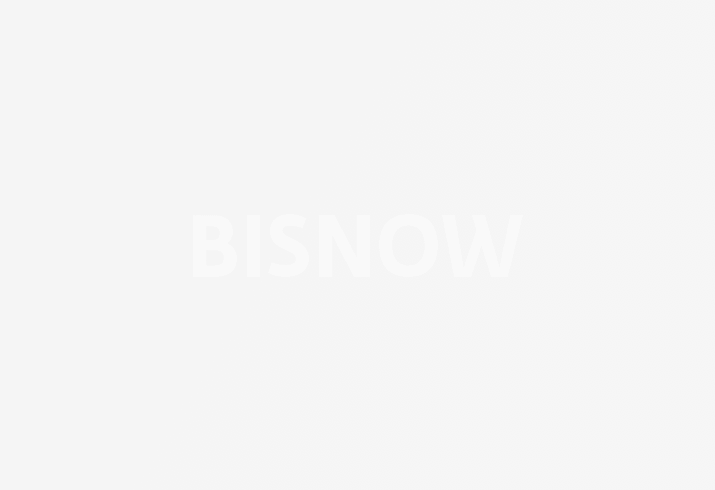
Houston-based companies Marek Family of Cos. and Gilbane Building Co. are among the 360 local companies that have earned the Construction Career Collaborative, or C3, accreditation. The intensive process measures companies' commitment to strengthening the labor force through employment practices, safety and skill training programs.
C3-accredited employers must offer hourly wages and overtime pay, hold Occupational Safety and Health Administration safety credentials, provide craft and safety training and cover all employees with workers’ compensation insurance. All craft workers must complete the OSHA 10-hour course, while field supervisors are required to have the OSHA 30-hour course.
C3-accredited employers have noted an increase in safety and reduction of time lost at project sites, Gremillion said. The incident rate at C3 projects is 0.81%, which is nearly four times better than the national average. Members also record loss of time that is 20 times better than the national average, based off U.S. Bureau of Labor Statistics data.
Chamberlin Roofing & Waterproofing, a C3 partner, measures the success of the training program based on the dollar amount of yearly rework or callbacks. Prior to 2008, the company, which was making 25% of its current revenue, was losing $2M a year on rework costs.
Since launching its training program, the cost of callbacks in the last five years has dropped to about $350K/year, which frees up more money for its $385K/year training budget. Last year, the Chamberlin University-Apprenticeship I Program noted a 90% employee retention rate compared to 72% companywide.
Not all companies set and meet those standards, and that is one of the problems, Gremillion said.
But if the industry — owners, general contractors and specialty contractors — wants a strong pipeline, it must be willing to treat employees better, he said.
One of those ways includes setting higher salaries. Hourly earnings in the industry averaged $30.21 in October, a 3.9% boost from a year earlier and the steepest one-year raise since June 2009.
"Contractors are raising pay faster than at any time since the recession to attract workers from other industries as well as new entrants, yet many firms report they continue to have difficulty filling positions," AGC Chief Economist Ken Simonson said in a release.
Increasing The Interest From Students
Compensation is only part of the sell, Gremillion said. Students and people switching careers want a sustainable career path with benchmarks for promotion. Companies must identify the skill competencies within each role and structure the training programs to reinforce those skills, he said.
Marek Family of Cos. Chief Operating Officer Mike Holland blames the nationwide push to send students to four-year colleges and universities rather than trade schools. There has been a host of initiatives recently to encourage students to master the craft, technical and professional skills.
He recruits for high schools and college students to enter the blue-collar craft industry through mentorship and speaking engagements.
“Not everyone needs to go to college,” Holland said, who is speaking at Houston 2019 Forecast event Nov. 27. “People think that is the only way to get ahead.”
After the midterm elections last month, the AGC called for Congress to double, over the next five years, federal investment in career and technological education.
"Our economy is producing too many underemployed college graduates and too few people with the skills needed to pursue high-paying construction careers," AGC CEO Stephen Sandherr said in a release.
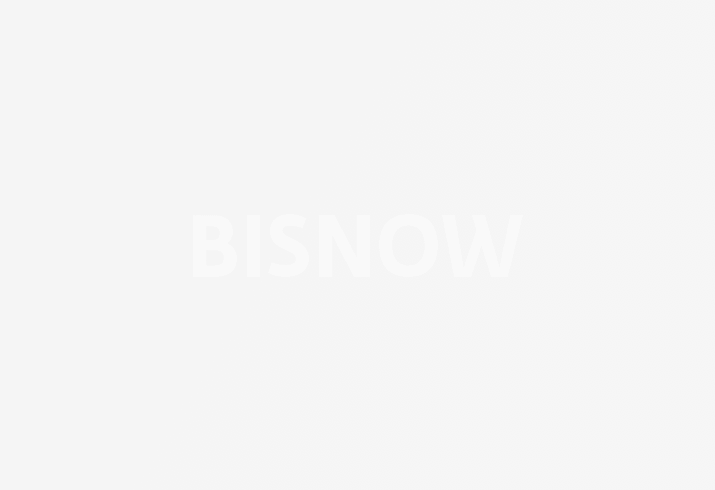
Prefabricated Material Construction
DPR Construction is taking a different approach. Through its subsidiary Digital Building Components, the company has begun constructing properties using prefabricated materials. The technology cuts back on labor and saves time, though the pricing is about the same, said DPR Construction Project Executive Greg Trujillo, who is also speaking at Bisnow's Houston 2019 Forecast Nov. 27.
The company used prefabricated materials to build a rehabilitation center in Midtown. It is also considering the technology for the new hotel construction pipeline in Houston.
For DPR, the next step in prefabricated materials is to include the electricity and plumbing framework during the pre-installation process, which would reduce time, cost and labor needs.
In particular, the pre-installation can help offset the insufficient number of electricians, plumbers and mechanical contractors — the biggest strains on the industry, according to Trujillo.
As the energy capital of the world, the labor shortage of those roles in Houston is even more pressing than in other areas because the construction industry is fighting to keep or attract skilled craftsmen who would also work in offshoring drilling or other energy-related jobs.
Challenged by the construction labor shortage, Houston-based companies outline future development plans in the hotel, office, retail, multifamily and mixed-use at Bisnow's Houston 2019 Forecast on Nov. 27.