Shifting Supply Chains Make It A ‘Fascinating Time’ For Growing Houston-Region Ports
Texas is gaining what California is losing in more ways than just population.
Port Houston’s container traffic in 2022, 4 million twenty-foot equivalent units, made it the fifth-busiest port in the U.S. by TEU volume, according to a new report from Savills. That's up from sixth-busiest in 2021. Houston also retained its No. 1 spot for waterborne tonnage volume.
Now experts say industrial development needs to step it up to keep pace with the growth — if the region can keep most of the traffic redirected to the Gulf during last year's supply chain snarls.
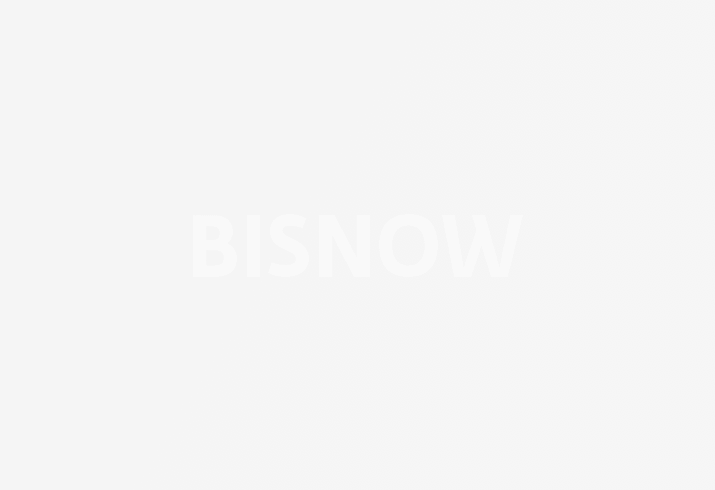
TEU volume increased 7.5% from 2012 to 2021. Then, “amid West Coast congestion and labor bottlenecks,” volume nearly doubled to 15.1% from 2021 to 2022, the report states.
Container traffic dropped off slightly at the top of this year, raising the question of whether Houston will be able to retain the traffic it captured from California.
“There is some debate about how much it's going to bounce back to the West Coast,” said Mark Russo, senior director and head of industrial research for Savills. “But I think there'll be a degree of stickiness there in Houston.”
It isn’t all sticking immediately, though, which is for the best as the port and its industrial partners catch up after last year's breakneck pace. The Savills report shows congestion on the West Coast reached a peak in late April 2022, when the Oakland port reached a median wait time of 33.7 days. Houston’s wait time, which hovered between three and seven days for most of last year, was 8.5 days at the time.
In July, Port Houston’s median wait time reached a peak of 16.2 days. The report also shows spikes to about 14 days in August and October, though it leveled off to between four and five days from November on.
At the busiest time, 97% of the port’s land storage space was taken up by containers, Port of Houston Authority Commission Chairman Ric Campo said, adding it was important that it did not get to 100%.
“We did things like increase the cost for people to let boxes sit on our sites,” he said. “We were the low-cost provider, so you have a situation where a lot of people use the port to store stuff. Unfortunately, that's not a good thing.”
That helped ease up the use of industrial storage sites on port property, but more is needed. To that end, there is $2.1B worth of infrastructure projects underway at the port, Campo said. Of that, $1.1B is going to deepen and widen the ship channel, and another $1B is going toward land side investments, including container facilities, cranes and a wharf system expansion.
It’s important to invest more than it might seem necessary, considering people at the port six years ago would likely not have believed container volume could have doubled by now, Campo said.
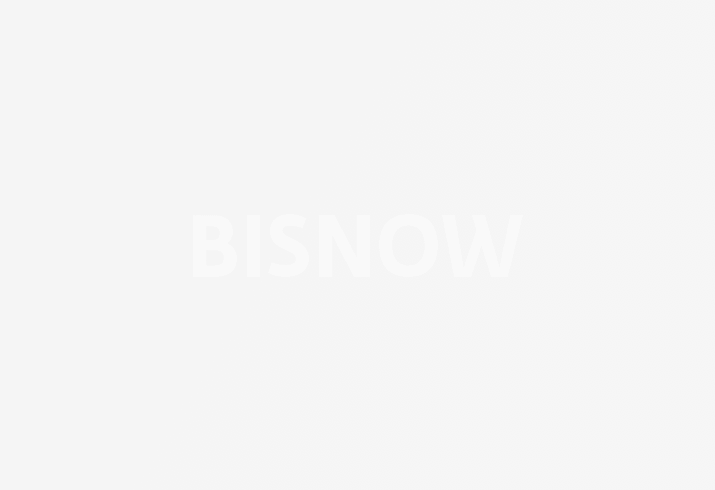
“We have to stay ahead of investing in infrastructure so that we don't have a situation where all of a sudden, we're stuck and we don't have the ability to move products through,” Campo said.
As far as external industrial development, “I think it is keeping pace. But everything’s full,” Campo said. “So I think that there's definitely growth to be had.”
There’s only so much land adjacent to the port, said Ed Emmett, a fellow in energy and transportation at the Baker Institute and a former Harris County judge.
“I think more and more, you're gonna see those warehouse distribution centers move inland a little bit,” Emmett said. “We're already seeing it. If you drive out on I-10 West, and I drive out there probably at least once a month, it seems like every month I go out there, there's a new big distribution center going up.”
Distribution centers are another thing moving from California to Texas, said Richard Quarles, executive vice president within JLL Houston’s industrial services group.
Last year, there was a high-end furniture retailer “getting stuck in the water” while trying to get into Long Beach or the Port of Los Angeles, he said.
“They were having the hardest time with it and decided ‘Wait a second.’ They looked at their numbers, they looked at the cost of transportation to get product to Houston over the water,” he said. “Next thing you know, they opened up a 150K SF distribution center in Houston.”
As companies come to look at the Houston area, they realize it makes sense to shift more of their distribution here than originally planned, Quarles said. He’s seen companies go from wanting 300K to 400K SF when originally planning a Houston location, then bumping that up to 700K SF by the time they sign a lease.
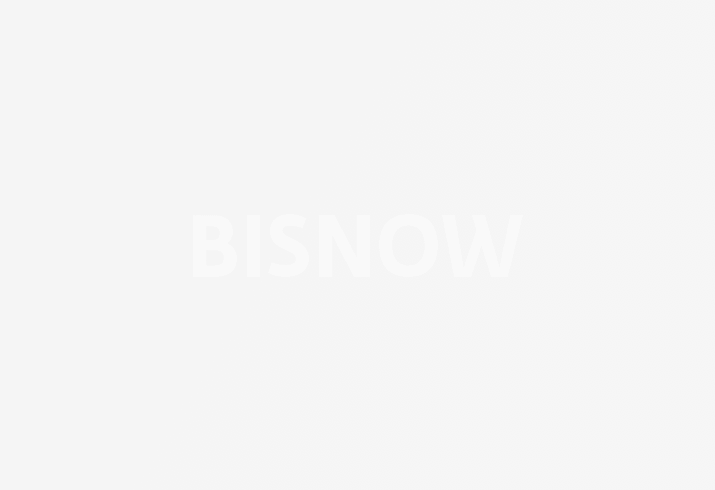
“When they evaluate transportation costs, labor costs and then real estate costs, Houston is a great fit,” he said. “They're like, ‘Wait, we knew we needed about 250K SF to 300K SF to serve Houston. But we also need to look at diversifying our supply chain. Instead of bringing it to LA and to Dallas, why not serve Dallas out of Houston?’ You're seeing an elevation of the role that Houston plays in any given distributor's goods and their supply chain network.”
New-to-market tenants comprised 14% of Houston leasing activity, or 13M SF of 92M SF, in 2021 and 2022, according to JLL data provided to Bisnow.
There were 36.3M SF of industrial groundbreakings in Houston in 2022, the data shows, though Quarles expects that number to drop to about half in 2023 due to the general slowdown of the CRE market, he said.
Container volumes at Port Houston in January slipped 1% from the previous January, though port officials cited Macy’s new 900K SF distribution center set to open in southern Tomball and other industrial development coming online as a reason the container import outlook remains strong.
Aside from the congestion at West Coast ports last year, traffic patterns shifts are reflective of a larger trend of diversifying the supply chain across the country, Campo said. Part of that is due to the Panama Canal becoming wider and deeper in 2016, allowing for larger ships to pass through and reach the East Coast more quickly.
"So yes, last year, our container volume was up," he said. "It's basically a continuing of the longer-term trend, which has been that shipping has diversified more around the country rather than being in one specific space, specifically the West Coast."
Manufacturing is diversifying, too, with China losing some of its manufacturing dominance. East Asian destinations, including China, Taiwan, South Korea and Japan, make up 39% of the port’s import and export traffic, followed by 25% European/Mediterranean, 21% Latin America and 12% Middle Eastern, Campo said.
“Latin America and East Asia have been growing pretty dramatically over the last few years. Europe has come up a bit,” he said. “Manufacturing that's moving around the country and around the world is generally moving to East Asia or Latin America.”
A trend of nearshoring, or bringing product manufacturing closer to customers, is bringing more manufacturing to Mexico, The New York Times reported, pointing to Chinese manufacturers setting up shop in the country closest to its main customer base in the U.S.
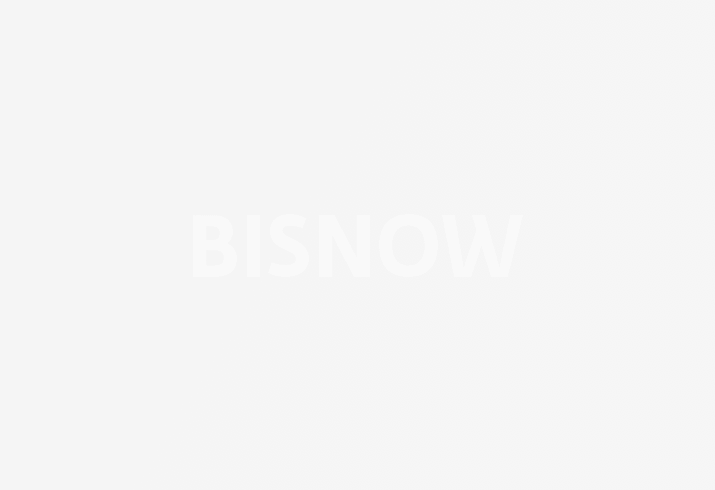
Port Freeport, a smaller but growing port about 60 miles south of Houston, saw 30 million tons of cargo move through last year, and is capturing new traffic from south of the border. It has a $295M deepening and widening project happening that should be completed this year, giving it the deepest port in Texas at 56 feet.
The port imports vehicles and heavy equipment from Korea, Japan, Australia, India and Mexico, Port Freeport CEO Phyllis Saathoff said.
“The market from Mexico has been a growing one for us,” Saathoff said. “Especially this past year when there were the threats of rail strikes, some of the manufacturers opted to shift to short-sea shipping to not get caught up in a situation where they couldn’t get their vehicles to market.”
Volkswagen Group of America announced in October 2022 that it is making Port Freeport its Gulf Coast hub for future operations. It will import about 140,000 vehicles per year, primarily from its factories in Mexico. It is building a facility near the port that is set to be complete in early 2024.
“[Industrial development] interest has increased as we've continued to announce progress on our berth and progress on the channel,” Saathoff said.
Shipping companies don’t start and stop services on a whim, Campo said, adding that most have a route of eight to 14 ports that they regularly move through in a circular motion. That means traffic at Port Houston should remain strong.
“They don't really change the routes very much,” he said. “At least until they think that they can get a better route.”
It becomes “purely a supply chain logistic question,” Emmett said. If a ship comes through the Suez Canal, there is debate on whether it’s more convenient to land in Savannah and transport product by rail or truck across the east, or stay on the water and head to Houston. That decision could bring more traffic going forward, he said.
“It's going to be a fascinating time,” Emmett said.