Supply Chain Snarls Prompt Companies To Expand Distribution Networks, And Houston Is Reaping The Benefits
Given manufacturing delays, labor shortages, transportation bottlenecks and skyrocketing consumer demand, the global supply chain has been in disarray for more than 18 months. And with major ports on both coasts now struggling with unusually high levels of congestion, Gulf Coast port cities like Houston are reaping the benefits.
Record volumes of cargo are flowing through Port Houston while the industrial market is on track to experience its strongest year ever for absorption. The surge comes as supply chain clogs create headaches for retailers and their suppliers and firms respond by expanding and diversifying their U.S. distribution networks.
“[California ports] are landlocked in, bottom line, and Houston is not. So it really becomes a competitive advantage that we have this space,” University of Houston instructional assistant professor Margaret Kidd said.
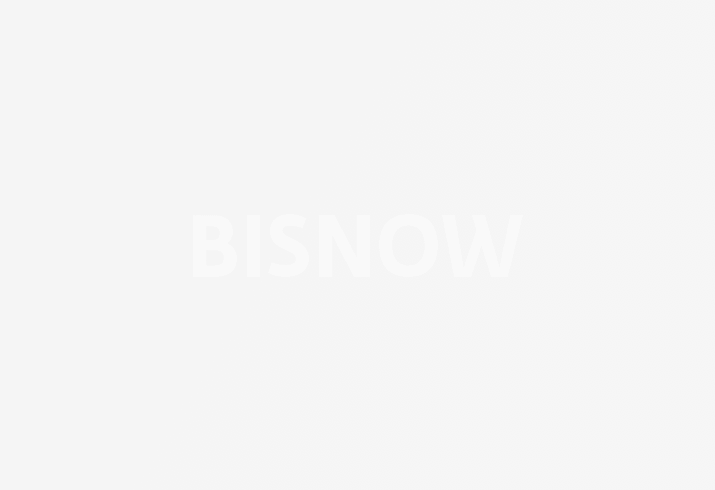
August was Port Houston’s best month on record for cargo volumes. The port handled 320,086 twenty-foot equivalent units, or TEUs, an increase of 29% compared to August 2020. Year-to-date, Port Houston also reached 2,225,500 TEUs in August, up 16% from the same period last year.
Like other U.S. ports, imported cargo volumes have been growing throughout the year. But unlike the Port of Long Beach and the Port of Los Angeles in California, the Port of Houston has not been suffering from crippling bottleneck problems, and the greater Houston region has been able to meet the growing demand for warehouse space.
Port Houston Chief Commercial Officer John Moseley told Bisnow that new importers to the Houston region are looking to expand their U.S. distribution networks in light of the tough conditions facing ports on the West Coast.
“Combining that with consumer spending and retailers building up their inventory to meet that demand is driving these record levels through Port Houston,” Moseley said.
Port Houston’s cargo volumes are growing at a faster rate than some other ports, indicating a growing shift in where imported goods are flowing. Moseley noted that aside from international firms, the port has also been talking to several U.S. big-box retailers looking to change their own distribution networks and import through Houston for the first time.
“You do see a number of companies that are actually opening up new warehouses here, that complement their existing networks,” Moseley said.
The slippage of goods from West Coast ports to Gulf Coast ports actually began about 10 years ago, driven by congestion and labor issues, according to Kidd. However, that trend has rapidly accelerated over the past 18 months because of the coronavirus pandemic and global supply chain problems.
“When you consider that 40% of all Asian containers to the U.S. go to LA-Long Beach, you just have a giant recipe for disaster,” Kidd said. “That volume cannot be handled. And so, certainly Port of Houston and other ports in the U.S. have been beneficiaries of some additional trade coming here.”
Port Houston is still dealing with challenges, like occasional wait times for cargo ships, extended dwell times for trucks, and availability of both chassis and truck drivers. While those things may have an impact on efficiency and productivity, it’s still light compared to the challenges faced by other major ports.
Notably, ships rarely have to wait long to dock at Port Houston, which is a reflection of its infrastructure and capacity, according to Moseley. He said the port has been continuously adding container yard space and wharf space for decades, spending about $200M on infrastructure every year.
“We’re not immune to the same supply chain issues that are taking place in other ports around the country, we're just doing a little bit better, I'd say,” Moseley said.
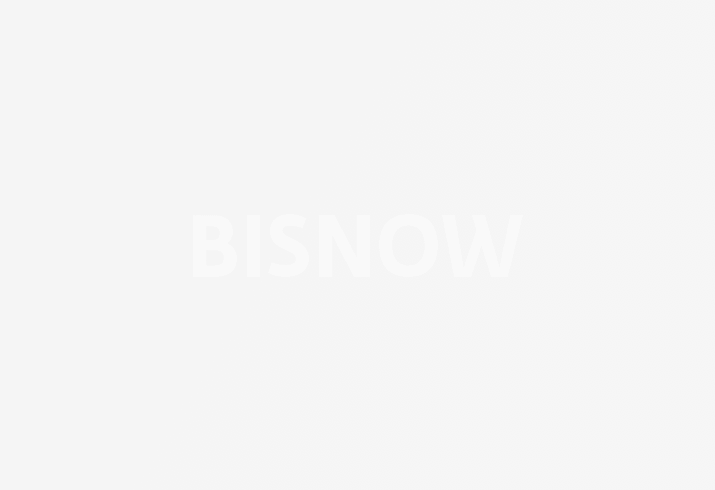
The change underway in U.S. distribution networks is having a tangible impact on Houston’s industrial real estate landscape. In 2020, Houston absorbed more than 17M SF of industrial space, and as of Q2 2021, had already absorbed 11.4M SF, according to Transwestern market data. In comparison, the city has averaged around 11M SF of absorption annually over the past decade.
CBRE Senior Vice President Faron Wiley said 2021 is shaping up to be the best year on record for industrial absorption in Houston. The demand is welcome, as more than 30M SF of inventory were delivered in 2020 alone, leaving the market with a short-term glut of supply. Wiley said that from a tenant standpoint, the timing could not be better.
“There were very good options for tenants and users. Lots of variety at value price and cheaper than what they were seeing in other markets,” Wiley said.
The demand for warehouse space in the greater Houston region is primarily being driven by demand for e-commerce and consumer goods. That has led to a significant number of third-party logistics firms looking to set up shop in Houston.
3PL firms usually prefer to stay near Port Houston, as it makes them more attractive to potential customers, Wiley said. They also tend to look at spaces between 100K SF and 400K SF, though the majority have ended up leasing at the upper end of the range or even higher, he added.
At the beginning of the year, Wiley told Bisnow that he had seen an uptick in activity from Chinese 3PL companies that already have a base in California. In some cases, those firms operate as the logistics arm of major consumer goods manufacturers in China, handling the U.S. distribution of e-commerce product.
Wiley said the expansion of 3PL firms to the Houston area, including international operators, appears to be a long-term trend, with some opting to actually buy real estate around Port Houston rather than just lease.
“If you're coming from the coasts, you look at Houston, and the buildings, from a value standpoint, are a bargain,” Wiley said.
In contrast, Wiley said, U.S. companies that import goods from overseas and are expanding their networks in the greater Houston area have more likely opted for warehouse locations further from the port, with a greater emphasis on racking and storage than speedy throughput. Areas like Katy and Brookshire, west of Downtown Houston, have been popular for that purpose.
Another popular area with retailers is the 15,000-acre TGS Cedar Port Industrial Park in Chambers County, which is situated across the Houston Ship Channel from the Bayport and Barbours Cut Container Terminals. The industrial park is home to distribution centers for major retailers like Walmart, Floor & Décor, Ikea and Home Depot.
Just last week, TGS Cedar Port Partners announced that it had broken ground on the largest industrial speculative building in Houston to date, totaling 1.2M SF. It reflects the trend of industrial distribution buildings getting bigger, which Wiley said he expects to continue.
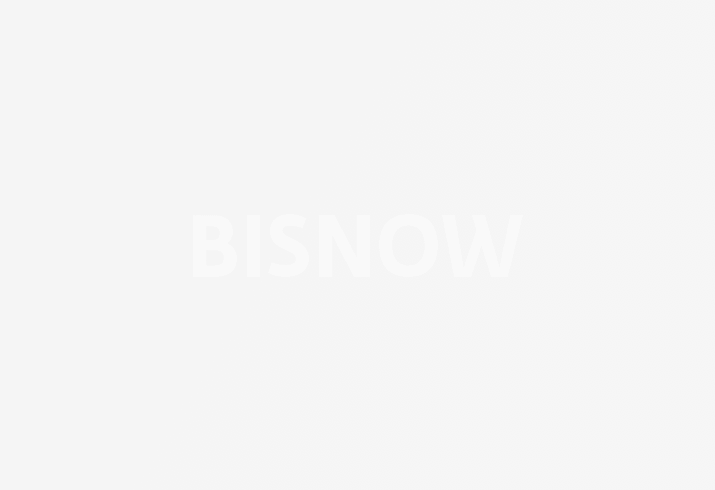
Kidd, Moseley and Wiley all say that as more firms look to reconfigure their distribution networks, Port Houston is likely to continue seeing an upward trend in cargo volumes, which would continue to drive demand for industrial real estate in the greater Houston region.
“I wouldn't call it stealing, but it is a diversion, it is a conversion of freight that was moving to a warehouse [on] the West Coast,” Moseley said.
Wiley said Houston is not necessarily taking market share from other ports. Rather, the overall market is rapidly getting bigger due to sky-high demand for e-commerce and consumer goods. In short, there’s a bigger pie for everybody.
“There's way more to go around, and frankly, LA can't serve them all," Wiley said.