Quality Is Critical To Realise The Potential Of Modern Methods Of Construction
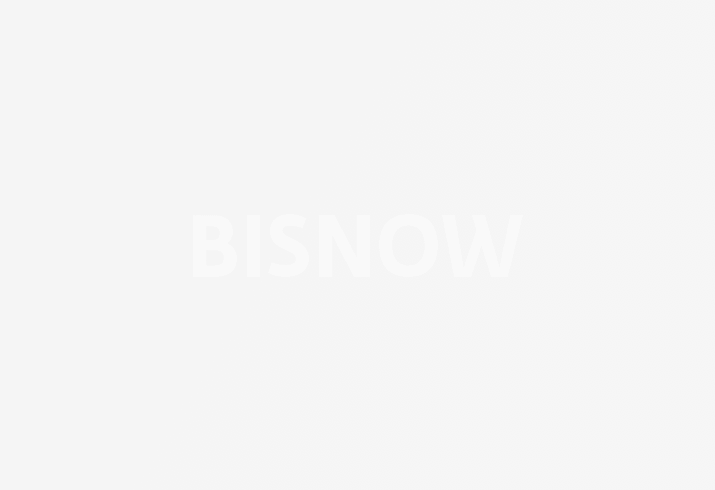
Before the pandemic, the UK was facing a housing crisis. Today, amid the pandemic, that crisis isn’t set to be eased soon. During the first UK-wide lockdown many construction companies and housebuilders brought sites to a standstill. Rules were later clarified to enable work to commence, but the pipeline of new homes for the year was still impacted. The government’s target to build 300,000 homes a year by the mid-2020s doesn't appear close.
Modern Methods of Construction could be one answer. While investors may be held back by historical stigmas, factories around the country are rapidly growing their manufacturing capabilities and, where standards are met, excellent homes are being produced.
“In recent times MMC have moved from being something out of a science fiction novel to a reality, particularly in the construction of units such as student accommodation and hotels,” Aldermore Bank Commercial Director for Commercial Real Estate John Carter said. “MMC is not something to overlook and could provide a significant opportunity, as long as certain standards and criteria are met.”
The Nuts And Bolts Of MMC
Many people think of modular housing when the term MMC is used. This is part of MMC, but the wider term refers to the off-site manufacture in a factory of either key components of a building, known as a panelised system, or whole sealed units ready up to the point of fittings such as wiring and plumbing. Flat pack components or whole units are then transported to the prepared building site and put in place.
There are many benefits to MMC. For example, homes can be completed more quickly than traditional building; or construction won’t be held up by poor weather or building errors. Costs can be lower if waste is reduced and less labour is required.
In terms of labour, MMC could plug a looming shortage. According to the Construction Industry Training Board, if the UK is to meet the government’s housebuilding targets using traditional construction methods, the sector’s workforce would need to grow by 40%. In reality, the workforce is shrinking as more people retire than join. MMC, which requires fewer skilled workers in a factory setting compared to on a building site, could reduce the necessary workforce size.
Green Credentials
Many of those involved champion MMC’s sustainable credentials, such as low waste levels, use of fewer materials such as water or cement, and lower energy costs.
“Sustainable developments that meet the needs of the present without compromising the ability of future generations to meet their own needs are challenging in a sector which, by its nature, is a big user of natural resources,” Carter said. “Yet many MMC techniques can bridge the gap between sustainability and construction practices.”
Carter said that one way developers are becoming more sustainable is their use of cross-laminated timber instead of concrete, a practice common in MMC. CLT is a structural, prefabricated panel used to form environmentally sustainable walls, roofs and floors with excellent soundproofing, airtightness and fire safety properties. Importantly, CLT also effectively absorbs carbon dioxide from the atmosphere and can be constructed off-site. The first major CLT building in London was the Stadthaus in Hoxton, which is one of the tallest residential timber structures in the world. It took four carpenters just 27 days to assemble the building.
Improved technology in MMC is improving long-term sustainable credentials further. Some developers are building homes that are carbon neutral and in some cases carbon positive. For example, UK residential developer and tech company Etopia has partnered with Samsung to create an initial 6,000 super eco-friendly modular homes in the UK over the next five years.
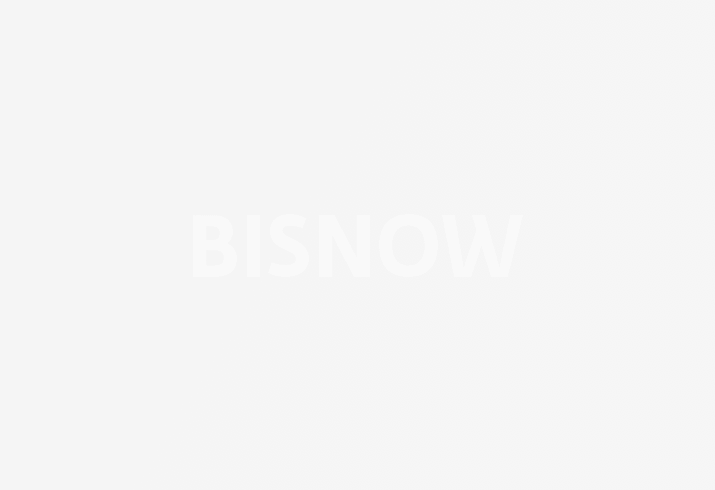
Slowly Dipping A Toe
The government has pledged its support for MMC. In 2019, Housing Minister Esther McVey announced plans to create a centre of excellence for MMC in the North of England and for Homes England to provide £38.2M to help build 2,000 new homes using the practice. In September 2020, the government announced that a fifth of homes built through its £12B affordable homes programme would engage MMC. So, with the government onside, what’s holding MMC back?
“To some development finance lenders, MMC is still relatively unfamiliar so they tend to take a conservative approach when deciding whether to invest in such projects,” Carter said. “Yet the primary consideration for any lender should be the quality of the project. Any build must be of high quality in order to meet and retain its value against which funding can be advanced.”
Investing in MMC certainly requires the lender or developer to put aside stigmas that if something takes less time to build, it is of a lesser quality. According to Carter, these perceptions trace back to the quality of prefabricated post-war emergency housing, which was notorious for being built to a substandard level. Of course, technology has come a long way since then, as have the standards to which developers must conform.
“For Aldermore, accreditation under the Build Offsite Property Assurance Scheme is a critical requirement for us when considering any MMC project for development finance," Carter said. "BOPAS is a risk-based evaluation scheme which demonstrates that a property will stand the test of time for at least 60 years — thereby showing that a development meets quality and sustainability considerations. We may also look for other warranties too, such as NHBC certificates for residential properties.”
As MMC is still new, the business model is evolving. Manufacturing off-site takes a certain volume to be profitable, for example, so there could be a challenge deploying MMC on smaller sites.
However, there’s little doubt that MMC’s growth will accelerate. Touting such benefits, it could answer many of the UK’s housing problems, for the affordable housing sector in particular. As Carter said, though, speed must be tempered by strict quality levels for MMC to pose a truly sustainable solution.
This article was produced in collaboration between Aldermore Bank and Studio B. Bisnow news staff was not involved in the production of this content.
Studio B is Bisnow’s in-house content and design studio. To learn more about how Studio B can help your team, reach out to studio@bisnow.com.