Why Early Design Engagement With A Manufacturer Creates Buildings People Want
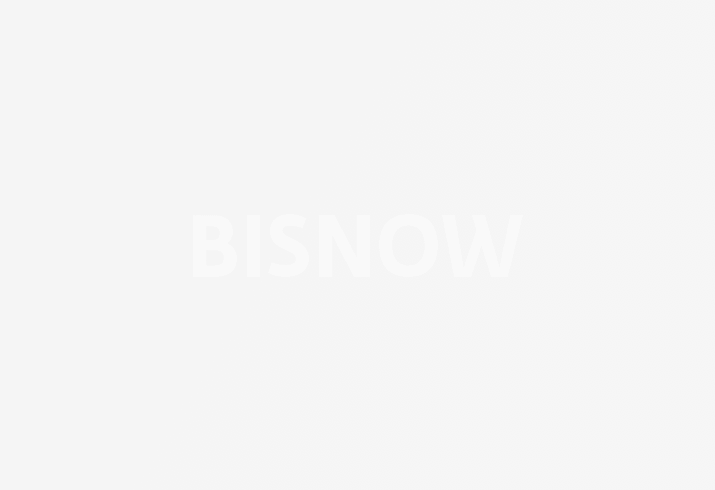
Developing a large building, or entire scheme, has always been complicated, but has arguably become more complicated over the years. Regulatory changes add new requirements, while societal changes have been exacerbated by the coronavirus pandemic. Add to that material shortages and a growing focus on sustainability, and a build programme can be hard to orchestrate.
“One way to ease these burdens is to have early design engagement with a building materials manufacturer,” Etex Market Manager Melanie Davies said. “The industry is going through significant change and a project needs to be flexible and as risk-free as possible. We work with clients as early as possible to make sure that a building achieves what it is supposed to.”
Etex’s UK Building Performance division includes brands Siniat (drywall), Promat (fire protection), FSi (fire stopping) and EOS (steel framing), which gives it coverage across multiple parts of a building specification. Davies outlined many ways that early design engagement with a manufacturer can reduce the risks associated with property development, while providing opportunities to create excellent buildings. Here are a few.
Regulatory Risks
Once a building is complete and handed over to the owner, that owner is responsible for risks. As such, owners want to be assured that the building meets all regulations — particularly fire regulations, which have come to the fore in the past few years. Davies said that many developers look to their supply chains with experience in this space to guide them through.
“Using a manufacturer that is also an expert in creating product systems that conform to regulations also makes sense,” Davies said. “The complete systems we create are tested in real-world scenarios, so collaborating with us early in the project to design for regulatory conformance will smooth out compliance. We’re also aware when a regulation is going change and can manage this.”
Insurance Premiums
Insurance premiums “can be a real pain point,” Davies said, as premiums have increased in recent years, again due to fire risk. Policies can be extremely expensive or might not cover all aspects of a building, such as a building façade.
Using a complete system can give peace of mind, Davies said, as insurers have full information about all the different materials used and how they perform together.
“You need the golden data thread, a way to make sure you’ve got a data trail on all products used from the beginning,” she said. “This is much easier if you work with the same supplier from the start. We offer project packs, with all information needed for you to have a data trail from day zero.”
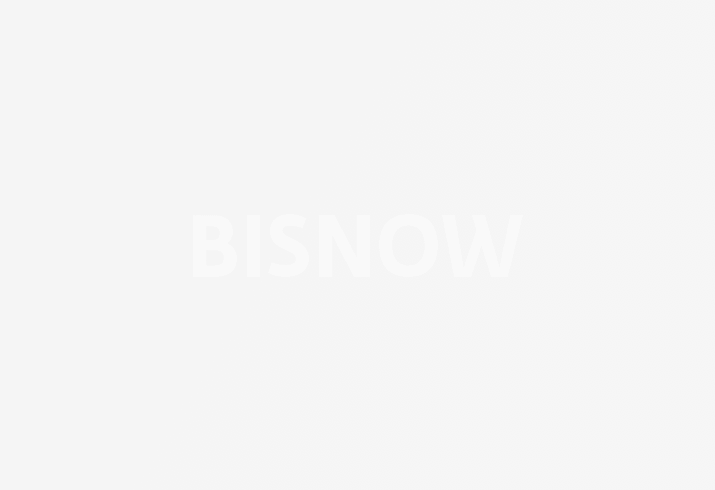
Supply Chain Continuity
The combination of Brexit and the pandemic has thrown many supply chains into disarray. Material prices have increased significantly and the shortage of haulers is pushing projects back. This can add both money and time to budgets, which hit the viability of a scheme.
“If you engage a manufacturer from the start, you know you will be able to deliver on your promise,” Davies said. “They will know when the order is going to land so can plan further ahead and ensure supply.”
Add to this less reliance on materials from overseas. Etex brand Siniat manufactures a lot of its plasterboards in the UK and has recently invested £140M in a new plasterboard factory that will open in 2023, which will significantly increase its manufacturing capacity. Not having to rely on an international supply chain makes logistics and deliveries a lot easier.
Consistent Quality
If you use the same manufacturer for several projects, you can be assured you will get the quality and consistency you need, Davies said. This is particularly important in the Build-to-Rent sector, where developers often build more than one building within a brand and want to meet and maintain a certain level of quality.
“We’ve worked with a large percentage of developers in the UK across sectors,” she said. “We’ve grown and delivered in the BTR space as the sector has grown. We understand the industry’s pain points and design needs. We know how to create a building that people actually want.”
For developers, the knowledge that they will be handed a top-quality building is essential. They can market the building to the right tenants, whether that’s commercial or residential, to ensure they get optimum return on investment and can achieve their goal: a building full of happy people.
This article was produced in collaboration between Etex and Studio B. Bisnow news staff was not involved in the production of this content.
Studio B is Bisnow’s in-house content and design studio. To learn more about how Studio B can help your team, reach out to studio@bisnow.com.