Finding New Tenants And Averting Hunger And War: Inside The Industrial Asset Class With Big Ambitions
Producing enough food to serve growing populations in the face of climate change is a major challenge for society in the 21st century.
That hasn't stopped one joint venture in the logistics real estate market from trying to address it — and in the process, open up a new world of potential tenants.
“How do we feed our people, how do we prevent mass migration due to climate change?” SmartParc CEO and founder Jackie Wild said of her operating company's lofty ambitions. “Because hunger means war, and war means enormous amounts of migration.”
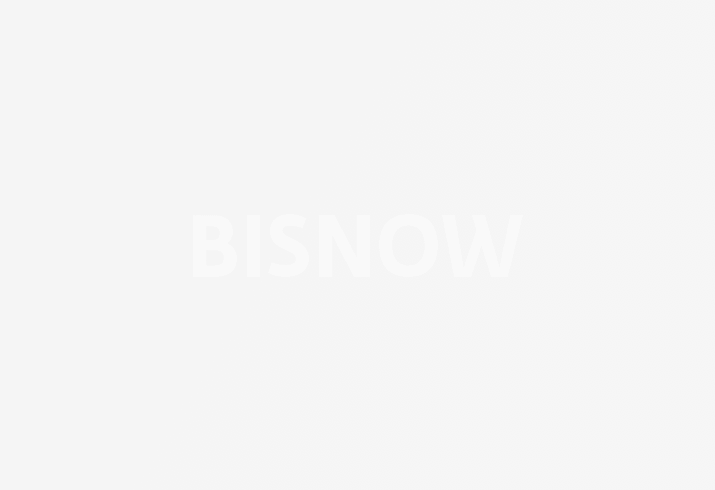
SmartParc aims to bring together food manufacturing and production businesses in specialist industrial and logistics parks in a way Wild said has rarely happened before.
And it has teamed up with industrial specialist Segro, Europe’s largest REIT, to build and manage 2M SF in the UK’s Midlands designed and built solely for food companies. The project will cost £300M and is already attracting tenants after launching in the middle of last year.
The company is looking to roll the idea out globally, with potential new ventures in Canada and North America, Poland, Ukraine and Indonesia on the drawing board.
For food companies, the concept can reduce energy, running costs and carbon emissions, making the sector more efficient while battling climate change, Wild said. For industrial property owners, it can open up a new source of tenants that have never been a major part of the industrial and logistics firmament.
The global food manufacturing market was valued at $121B, in 2021, data from Grand View Research showed, but logistics owners have not been able to tap into the market at scale.
“Food businesses have never made good neighbours or bedfellows in industrial parks,” Wild said.
That’s because food manufacturing or packaging facilities have very specific requirements. They need as much as six times more power than an average distribution facility, necessitating a huge amount of energy infrastructure that can end up using much of the power directed to a standard logistics facility.
Buildings occupiers in the sector also have highly specialised requirements, including temperature control, specialist floors and thicker walls, and large amounts of drainage and changing facilities to allow staff to maintain hygiene levels.
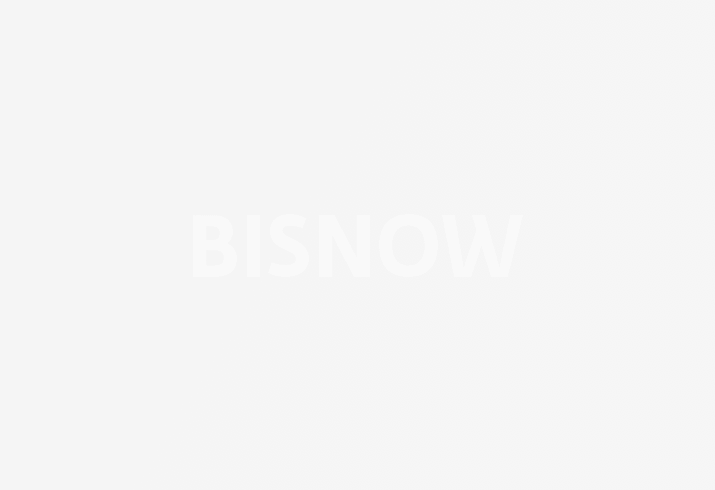
Those factors make it hard to put food manufacturing companies in a standard industrial park. Tenants in the sector tend to have bespoke facilities that they own themselves, but after a period, those facilities can start to become obsolete.
With a background in the food production industry, Wild's goal with SmartParc is to create large-scale industrial parks where tenants can cluster together, sharing energy facilities as well as services targeted for companies in the sector, from laundry and hygiene to recruitment.
The company says it can reduce production costs for companies by as much as 20%, and one big reason why is energy. The company’s first site will have shared energy facilities such as photovoltaic cells and heating and cooling systems that utilise ammonia. The shared system means that if one occupier on the park is not utilising much energy at a given time, it can be directed to other occupiers.
Because energy is shared and comes from renewable sources, less energy is used, and the price of each unit of energy is lower, driving down costs by as much as 30%, Wild said.
At SmartParc’s first facility in Derby, in the East Midlands region of the UK, the company plans a food manufacturing and technology centre of excellence, which will research how local and global supply chains can become more efficient. Having food companies clustered together in one place can also encourage knowledge sharing and innovation, Wild said.
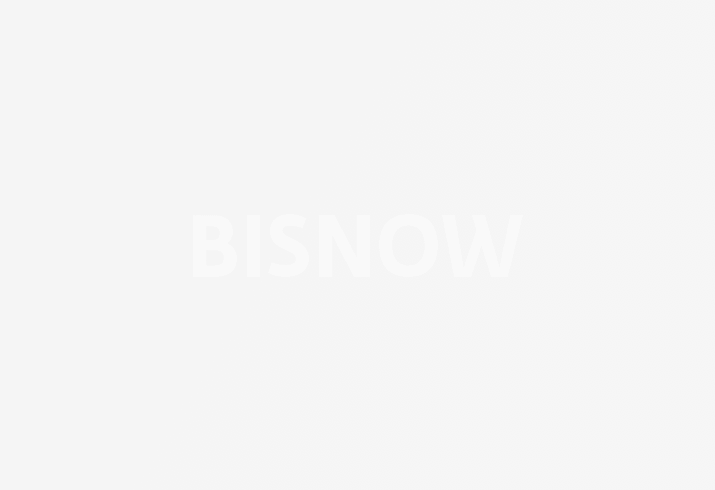
SmartParc Derby saw Segro and SmartParc form a 50/50 joint venture co-owning the land on which the facility is being built, with Segro then becoming the property owner and investing up to £300M to build the scheme and SmartParc acting as the operator.
The site will have between 15 and 20 buildings, ranging from 3.5K SF to 400K SF, with buildings being constructed specifically for individual occupiers rather than speculatively. Meal kit provider HelloFresh is the park’s first tenant, having signed for a 118K SF building in August last year.
“We’re a REIT and we’re looking to create sustainable long-term income, but it’s also a brilliant and innovative concept that fits our sustainability ethos and values,” Segro Head of National Logistics Andrew Pilsworth said. “Jackie and her team have an incredible knowledge of the food industry and know exactly what companies in this sector want, and we can bring our expertise as a property developer and long-term investor. It allows us to access a whole new type of tenant.”
Pilsworth said rents in the sector were higher than typical industrial rents to reflect the cost of more specialised buildings. That means the sector has a similar return profile to Segro’s traditional industrial business, but also provides greater tenant diversification.
Demand will come from occupiers looking to upgrade to modern facilities as well as companies onshoring production to make their supply chain more resilient, he said.
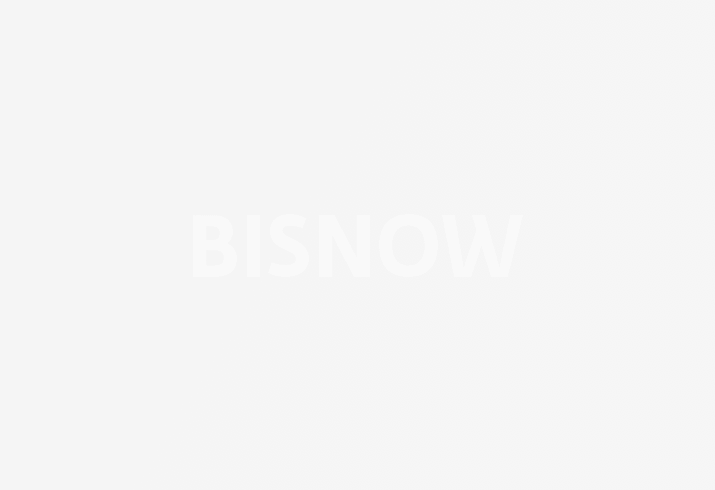
Wild pointed out that climate change was a particularly complex issue when it comes to food production — the sector contributes to rising global temperatures, and is then hit by the effects.
“If we’re serious as a nation about tackling climate change, then we have to look at this sector,” she said. “One-sixth of global emissions come from the food industry, so it adds to climate change. But also from the point of view of survival, every month we are seeing the affects of extreme weather events affecting farming and growing food. It affects every aspect of how we feed ourselves.”
The UK imports 52% of its food, she added, and global supply chains are becoming more uncertain as a result of conflicts like the Russian invasion of Ukraine, where much of the world’s wheat is produced.
Wheat won't be grown on an industrial estate, but Wild said vertical farms would be likely occupiers on SmartParc schemes. The viability of vertical farms increases as the cost of energy drops and as technological advances allow food to be grown to order, reducing waste.
The increases in efficiency SmartParc is aiming to also reduce food waste and boost supply, Wild said, adding that part of the research being undertaken in Derby would involve just that.
“Segro is the first investor, but this is an asset class that will go around the world,” she said.