Window Film A Must For Building Repositioning
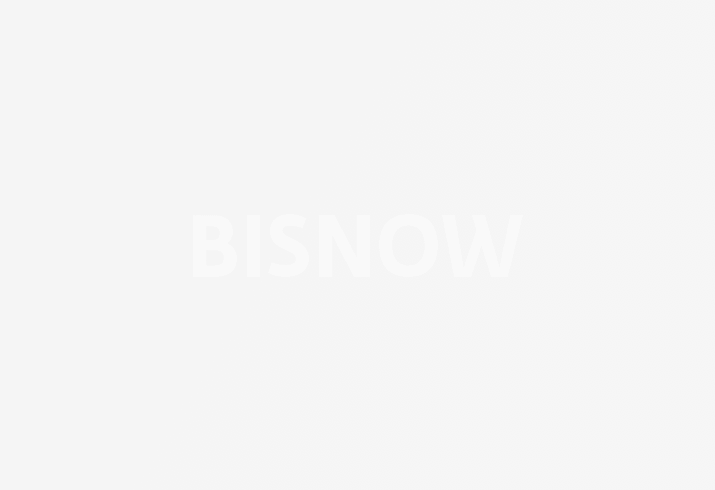
To stay relevant in today’s marketplace, repositioned assets have to keep up with a new generation of sleek, efficient green buildings. One way for owners and developers to quickly add value during repositioning efforts is by improving window quality. Energy-efficient windows can help keep buildings from falling behind a greener market.
“Sometimes building owners’ budgets won’t allow for the expense of full glass replacement,” Campbell Window Film CEO Brad Campbell said. “Using window film to convert existing, single-paned windows into high-performance glass can be a more cost-effective solution.”
Southern California is dotted with commercial buildings that were constructed prior to the use of high-efficiency glass. Reflective glass, which offers some increase in efficiency, has been in use since the 1970s, Campbell said, but this glass falls far short of today’s super-efficient low-emissivity or “low-E” glass.
Low-E glass is made of nano-coatings that block infrared rays while allowing visible light to pass through, keeping buildings cool in direct sunlight and warm in cold weather. This kind of glazing is integral to the most energy-efficient properties in today’s market, including net-zero and LEED Platinum buildings. It is also an important step for buildings looking to attain compliance with California’s Title 24 efficiency standards.
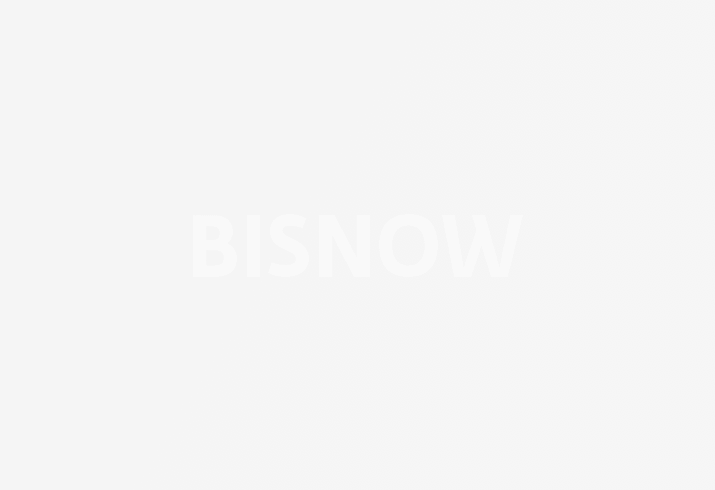
Low-E glazing was introduced in 1981, but was not used widely in commercial construction until the mid-1990s, Campbell said. Now, it is standard on new commercial construction, but thousands of legacy buildings in SoCal are still stuck with outdated glazing, which means they could be wasting hundreds of thousands of dollars a year in heating and cooling costs.
If an owner or developer is building from the ground up, installing low-E glass can ensure long-term savings and uphold efficiency standards. But Campbell said window film can achieve the same level of solar performance as dual- and even triple-paned low-E windows on existing buildings.
And often, replacing old windows with low-E glass does not make sense for repositioning projects or renovations on existing buildings, as low-E glass can cost eight times as much per square foot as window film.
Campbell cited a cost savings study done on Disney Channel’s building in Burbank, California, where Campbell Window film installed 3M Thinsulate Climate Control Window Film. For 16 years after initial installation, the building forecast savings of $251K/year, with payback on the investment reached in only the third year after installation.
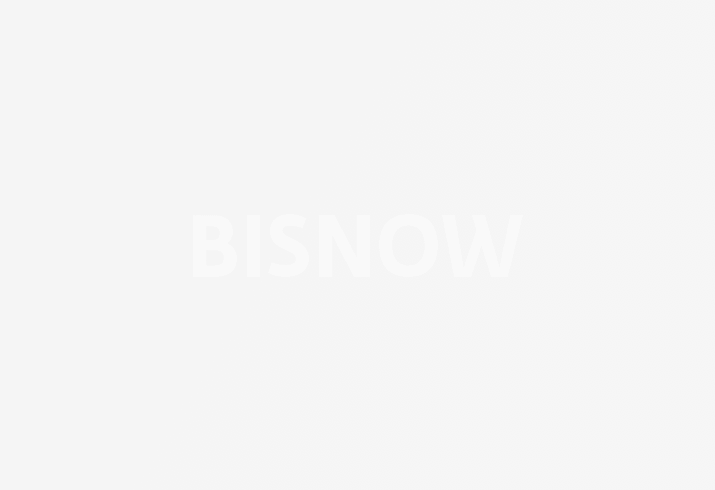
Keeping buildings cooler in the hot months of the year can also keep tenants around longer, Campbell said. Comfortable tenants mean higher occupancy and lower tenant turnover. Combined with energy savings, tenant happiness can drastically increase buildings’ return on investment through the repositioning process.
Campbell said building owners are hesitant to fork over the initial cost of window film, even with the guarantee of a reduced energy spend and the accompanying long-term savings on utilities. Part of the problem is what appears on profit-loss statements.
“Money put toward energy bills, which has been termed ‘purple money’ does not figure alongside so-called ‘green money’ on profit-loss statements,” Campbell said. “Consequently, the initial investment in energy savings is not seen as incentive enough.”
Commercial real estate owners sometimes look at purple investments as capital expenditures, Campell said, rather than a means to savings. He said he has seen success by helping companies quantify the amount of returns they can expect from an investment in window film.
This feature was produced in collaboration between Bisnow Branded Content and Campbell Window Film. Bisnow news staff was not involved in the production of this content.