'All Modular Is Not Created Equal': The Misconceptions Of Off-Site Building Types
Off-site building components, whether mass timber, storage containers or the various types of modular units, can be beneficial to getting projects done, but using them properly means understanding their nuances.
Panelists at Bisnow's Los Angeles Prefabrication, Modular and Mass Timber event discussed their various experiences building with these product types.
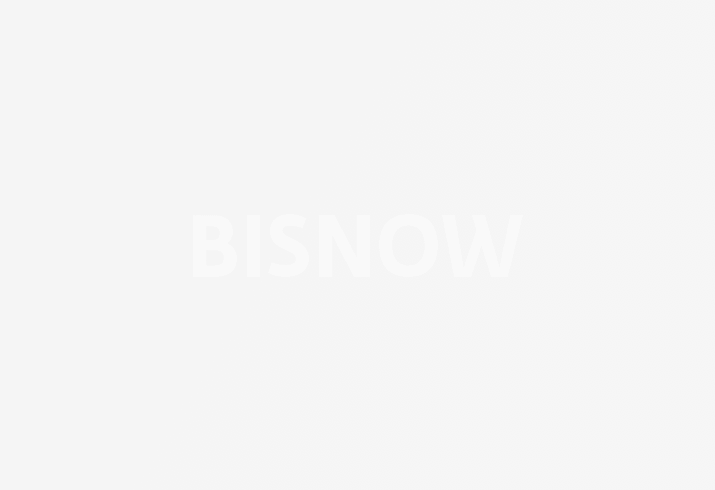
“Our first experience was using shipping containers,” RMG Housing Executive Vice President David Grunwald told attendees at the event, held Tuesday at Hilton Los Angeles Culver City.
“It didn't go well,” Grunwald said. “We had over $800K worth of overruns on a 40-unit project.”
Grunwald’s company learned a valuable lesson: If it’s not done right, in the right factory, staged in the right way and delivered correctly, “modular could be the exact opposite of what it's supposed to do,” Grunwald said.
A theme among the panelists was the level of coordination required for these projects to go smoothly. All the parties have to be brought in early in the process to assess the variety of logistical considerations, and everyone needs to be prepared for the hurdles unique to financing these projects.
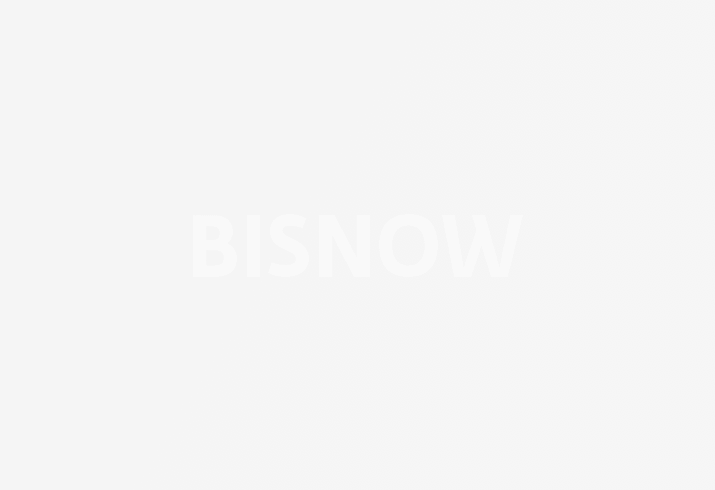
“What bothers me as an architect, when I come in to projects and I put on my developer lens, is that people don't realize that off-site construction is not about less due diligence,” Assemblage Works CEO Michael Mathews said.
“The reality is it's actually four times the amount of due diligence,” he said.
Perhaps because of the immense coordination or the fact that many users of modular seem to discover these complexities during their first foray into the construction type, there are plenty of users who have had negative experiences with modular building.
“All modular is not created equal, and I learned that the hard way,” Stack Modular Vice President of U.S. Operations Konstantin Daskalov said.
The company leaned into the negative experiences that some developers have had with the building type and threw an event called Modular Sucks, which was focused on showing developers how those problems weren't modular problems, necessarily, but problems with an individual company or provider.
“It was the most attended event we've ever done,” Daskalov said.
The broadness of the term modular, which many panelists defined as anything not built on-site, leads to the lumping together of product types like mass timber, shipping containers, prefab and steel-framed modules. People also often consider the various companies that specialize in modular construction as one and the same, to their detriment, Daskalov said.
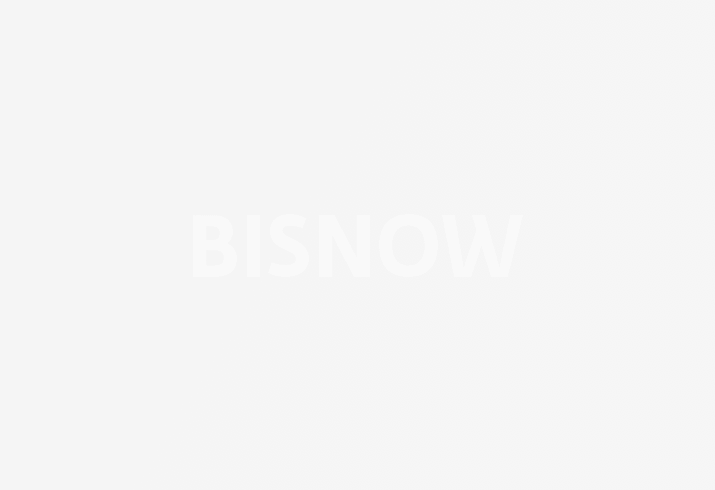
On the other hand, LA-based Primestor is working on a 371-unit project in Norwalk that uses modular units. Stack Modular and Assemblage Works are also working on that project.
For its project, Primestor hailed the city it was working with as much as its building partners for the success of its project.
“All these systems are providing so many alternative solutions, and sometimes there just needs to be clarity on the code perspective,” Primestor Development Project Manager Steven Vasquez said. “Getting the city on board as a partner, as a true partner in terms of working together and asking questions, is critical.”
California is, perhaps surprisingly, often adaptable to this new technology, a few panelists said.
“[California is] one of the best, far and away — one of the easiest and best and most forward-looking states when it comes to off-site modular construction,” Synergy Inc. CEO Justin Stewart said, pointing to San Jose as a city that welcomes the building type.
“The local municipalities, as they see it, as they get more comfortable with it, it becomes easier,” Stewart said.