Modular Construction Experts Share Development Tips For Prefab Success
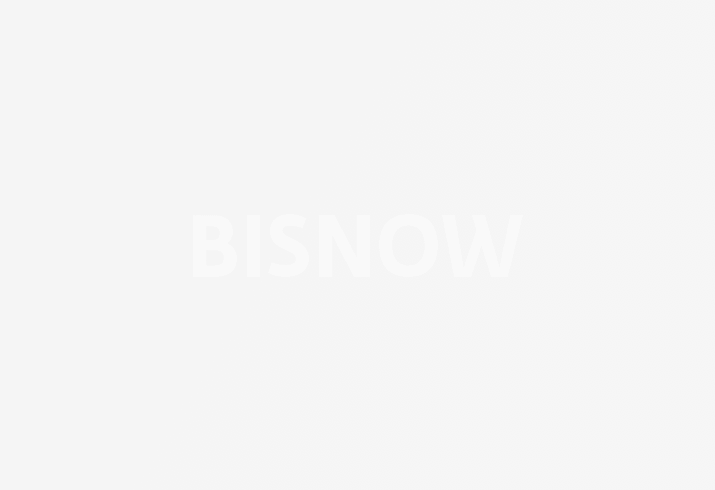
Prefabrication is growing increasingly relevant in commercial real estate across the board, but experts are still seeing developers question the benefits of modular construction.
“The developers out there look at us as a glorified subcontractor,” Slack Modular President Jim Dunn said. As a result, many developers neglect to clue in modular contractors until late in the process.
“If you can’t find a place for the crane, there’s no point in building boxes,” Dunn said, speaking about the process of moving the pre-built units onto a project site.
Dunn, speaking at a Nov. 16 Bisnow event about off-site construction in Downtown LA, was joined on a panel by other leaders from modular and prefabricated construction companies, all of whom agreed there is still a lot of education that modular companies have to do when they join or take on projects.
“If you’re approaching [modular] because your project isn’t penciling in your pro forma, don’t do it,” Synergy Modular CEO Justin Stewart said, although he did note that modular can often be a cost-saving tool in the end.
More types of commercial real estate projects are considering prefabrication. ProSet principal Scott Bridger said that pre-pandemic, his firm handled a lot of hospitality work — a trend becoming more commonplace across the modular field. In the wake of the coronavirus pandemic, Bridger is now seeing a surge in multifamily proposals seeking to use modular construction, from affordable projects to student housing.
CRATE Modular CEO Richard Rozycki said he has seen a significant uptick in projects that are funded through Proposition HHH, a voter-approved measure that funds permanent supportive housing for formerly homeless residents. He also has noticed a surge in demand for modular construction in K-12 education projects.
The panel, which also included Fulcrum Senior Project Manager Brad Lancaster, Prefab Logic CEO Doug Pill, and moderator Nolan Lenahan, associate principal at DCI Engineers, also touched on the need for more comprehensive standardization in the field.
Doing so would make it easier for different firms to work on the same project, panelists said. Manufacturers for the most part have their own way of doing things, making handoffs tricky.
More transparency around processes could also help advance prefabrication’s reputation overall.
“If a module leaks, if a module is upside down, we all wear that,” Dunn said. “Our industry wears that scarlet letter — it doesn’t matter who built it.”