How Waterproofing Technology Helped A High-Stakes Brentwood Multifamily Project
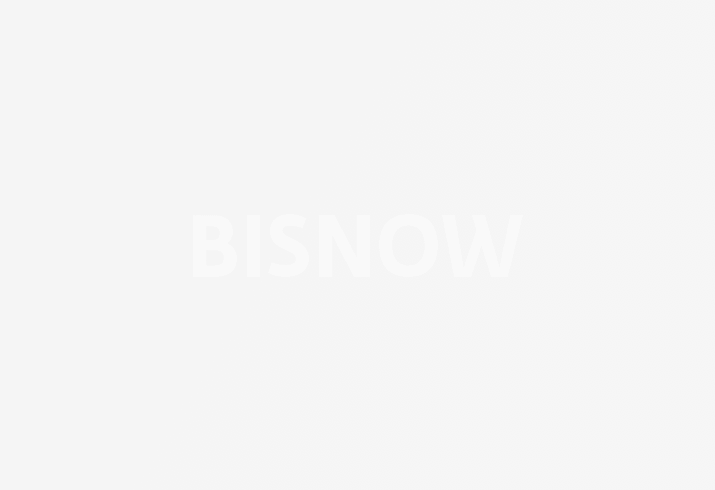
As an owner’s representative, Jim Suhr is always on the lookout for new and better ways to make his clients’ projects more efficient.
In January 2020, that search took on a new level of urgency as Suhr was overseeing the construction of the Respara at Brentwood, a resort-style multifamily development. The job site for the 54-unit project was situated at the end of a narrow road off one of the busiest thoroughfares in Los Angeles. Just beyond the property lie protected wetlands and a 40-foot drop into a ravine leaving only one way in. The narrow entry and lack of parking created a logistical nightmare.
With excavation underway and the project on the line, Suhr needed a way to pour and waterproof a two-and-a-half-level underground concrete parking structure. He needed a light footprint to reduce the number of deliveries and the number of people physically on-site.
The solution was Dricrete, a concrete admixture company that had been on his radar. Because Dricrete’s chemically advanced materials are added at the batch plant, Suhr could eliminate the waterproofing membrane and the weeks of logistics as well as the entire crew typically needed with a traditional waterproofing application.
“The No. 1 reason I went with Dricrete was to speed up the construction process as a whole,” Suhr said. “Because their products are mixed in at the concrete plant rather than on-site, we could be a lot more nimble with deliveries on the high-pressure site.”
Waterproofing Respara’s parking structure proved to be a complex undertaking. The residential area meant that Suhr couldn’t get tie-backs to any neighboring foundations to hold back the 30-foot high dirt walls. The team needed temporary rakers, steel rods planted at an angle that would reinforce the shoring walls. The process of shipping a membrane and all the necessary waterproofing adhesives, combined with the complexity of working a plastic membrane around the rakers would have proven extremely time-consuming.
Instead, Suhr took delivery of 120 loads of Dricrete enhanced concrete that could simply be placed around the rakers, easily solving the problem. Seamus Kennedy, owner and president of James Kennedy Construction, worked as the project manager on the Respara site and noted how the Dricrete application was handled by a highly capable two-man team.
“Dricrete fit in perfectly to that high-stakes environment,” Kennedy said. “Tim Yeiser, the company’s owner, was there himself 90% of the time, which was impressive to see.”
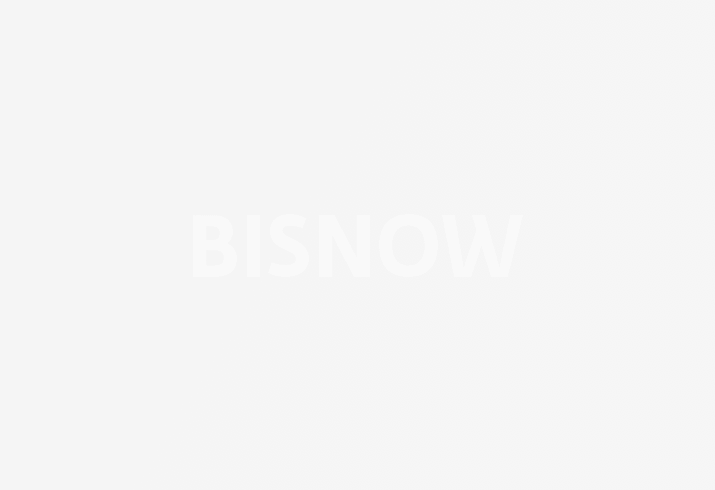
When it comes to waterproofing, he added, the less obtrusive a subcontractor can be the better. Usually, a waterproofing job requires coordinating between three or four different companies. If one laborer doesn’t show up or one contractor has a conflict arise, it can set a project back for weeks or months. Because Dricrete requires no coordination between multiple trades and uses a team one-tenth the size of a typical waterproofing crew, Kennedy supports using Dricrete on any kind of project.
“I’ve worked in concrete for almost 40 years now, and we’ve always done it the same way,” Kennedy said. “But after seeing the time savings, the dollar savings and how smooth the process has been, I’ve become a cheerleader for Dricrete. I’d take them with me anywhere I work.”
Because the Respara is a luxury project, Suhr understood that the residents would expect an elevated experience when they moved in. Having a waterproofing job that he could trust, and that would last, was especially important.
Unlike traditional membranes that deteriorate, Dricrete utilizes chemistry and technology that continues to grow stronger and more waterproof for the life of the building. Dricrete guarantees that it will cover the cost of any repairs no questions asked, eliminating the usual blame game that often accompanies these situations. During the first rainstorm after the garage had been poured, Kennedy said Yeiser himself arrived on-site, searching for any leaks that might need to be fixed.
Construction is nearing completion at the Respara site and delivery is expected in the fall. Suhr estimates that using Dricrete saved several weeks of work, translating to more than $100K in savings. He said he hopes those kinds of dollar savings will convince others to join in.
“Construction is an intensely physical line of work,” Suhr said. “It’s really just a network of human beings out there and innovation only spreads through word-of-mouth. Part of why things cost so much to construct is that we haven’t done a good job of modernization in this industry. So when an innovation comes along, I try to do my part and spread the word to my colleagues about how to build smarter and build better.”
This article was produced in collaboration between Dricrete and Studio B. Bisnow news staff was not involved in the production of this content.
Studio B is Bisnow’s in-house content and design studio. To learn more about how Studio B can help your team, reach out to studio@bisnow.com.