Waterproofing Doesn't Have To Be The Most Stressful Step In Construction
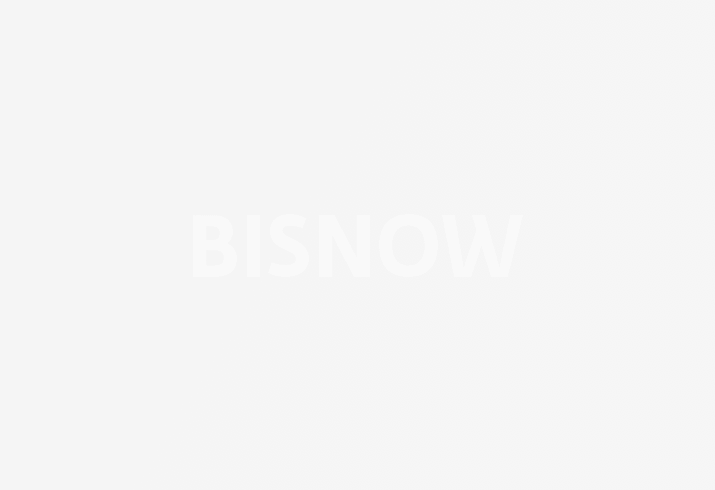
Advanced building materials are helping owners and contractors take the stress out of one of the most critical steps in any construction project: waterproofing.
Installing a membrane, the traditional method for waterproofing, can be a chaotic process, creating scheduling conflicts and requiring a heavy footprint of labor and materials.
If the membrane fails, it can lead to finger-pointing between owners, contractors, subcontractors and engineers. The rush to identify who will take the blame for the leak can turn a stressful construction job into an adversarial one, leading to delays and disruption.
“Every developer has a nightmare story about waterproofing,” said Tim Yeiser, president of Dricrete, which has developed a chemical waterproofing system as an alternative to membranes. “We haven’t lost a single day in 20 years with our system, and we can guarantee a faster, less stressful job.”
Unlike membranes, Dricrete’s waterproofing system has a light material and labor footprint. The chemical admixture is added at the batch plant, meaning there is no need for materials on-site. Only one person needs to be on-site to quality control the concrete pour. Especially with social distancing protocols in place, having fewer bodies on-site during waterproofing is a benefit.
The Dricrete team provides quality control on-site and at the batch plant to make sure the process runs smoothly. And after the concrete is poured, Dricrete guarantees that it will repair any leaks.
“We’ll hold your hand through the entire process,” Yeiser said. “If there is a leak, we’ll fix it, no blame game, no questions asked.”
Traditional waterproofing has always presented a massive logistical challenge. Coordinating between subcontractors, suppliers and consultants can take months of planning and scheduling. Any single team’s delays can upend the whole process and take weeks to reschedule, eating away both time and money.
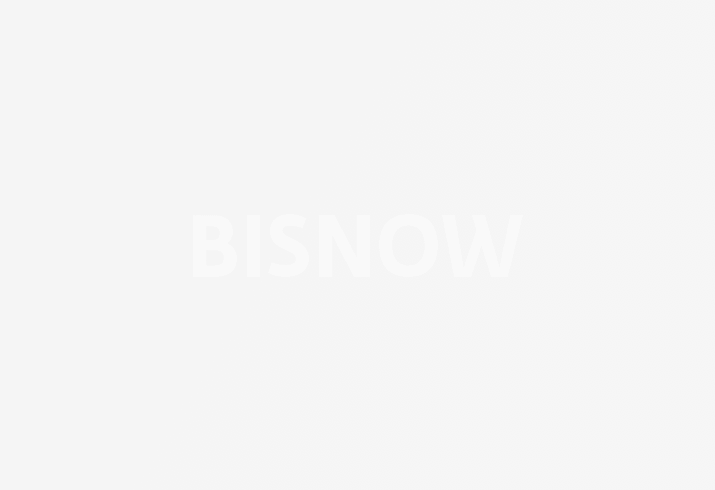
For every underground floor, eliminating a membrane and using Dricrete will shave a full week off the schedule, Yeiser said. For a multilevel, below-grade parking structure, those extra weeks can easily translate into hundreds of thousands, if not millions, of dollars saved.
The construction industry has made immense strides in terms of technology in the last decade, from 3D imaging to building information modeling and prefabrication. Dricrete is another technological leap forward, Yeiser said.
“The best day for any membrane is the day it’s installed. Then it becomes more and more vulnerable as time goes on,” Yeiser said. “Because of the hydrophilic chemical structure, Dricrete just gets stronger and stronger throughout the life of the building. It’s not subject to the human errors that can often derail a membrane installation.”
According to Yeiser, about eight out of every 10 construction lawsuits are centered around some flaw in waterproofing.
“By getting buildings out of the ground faster, we are alleviating the aggravation and anxiety,” Yeiser said. “This is just a smarter way to waterproof.”
This article was produced in collaboration between Dricrete and Studio B. Bisnow news staff was not involved in the production of this content.
Studio B is Bisnow’s in-house content and design studio. To learn more about how Studio B can help your team, reach out to studio@bisnow.com.