SoCal Port Volume Spikes As Industrial Looks For A Lift
Cargo volumes have shot up at the ports of Los Angeles and Long Beach, reflecting a recovery from the many challenges the ports faced after the pandemic began. The influx of goods is a welcome sight in an area known for the strength of its industrial market, but where warehouse leasing demand has sagged over the last year.
Activity at the ports, which could be further buoyed by a potential strike at East Coast ports, could contribute to the stabilization of the industrial market predicted next year.
“The last 3 months … have actually been record numbers for both of those ports – higher than volume during the pandemic,” CBRE Director of U.S. Industrial & Logistics Research Amanda Ortiz said in an email. “I would say that bodes well for industrial activity, depending on which products are being shipped over.”
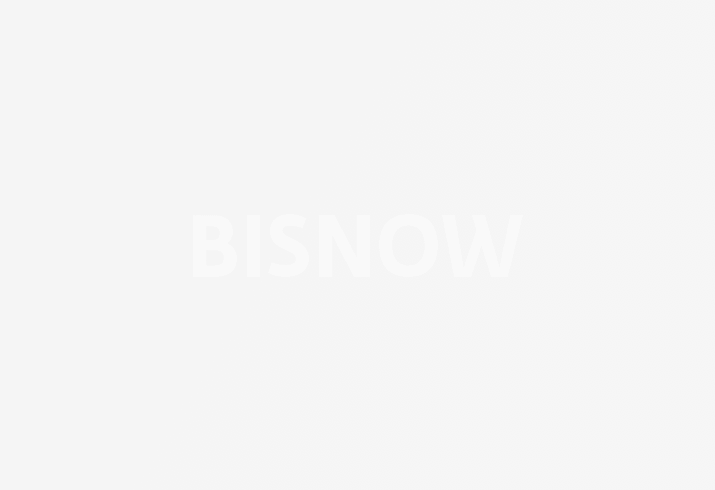
Southern California's industrial market, while one of the strongest in the country, has had a sluggish year, with its vacancy rate in Los Angeles hitting a 14-year high of 3.7% over the summer.
In August, the Port of LA processed more than 960,000 container units, up 16% from 2023’s roughly 828,000 container units, according to the port. The Port of Long Beach processed over 913,000 container units in August, a nearly 34% increase from its 2023 total for the same month, data from that port show.
August 2024 was the Port of Los Angeles’ busiest “nonpandemic month,” POLA Executive Director Gene Seroka said at a briefing last week.
The elevated container volume – “some of which is typically headed to other gateways,” Seroka said – has been making its way to the Southern California port complex for a variety of reasons.
At the forefront is the potential East Coast and Gulf Coast labor strike of port workers with the International Longshoremen’s Association. Workers and port operators along those coasts are on a contract that expires on Sept. 30.
Some shipping companies have already begun to divert their containers away from the East Coast in anticipation of a potential disruption in work, though others have not yet made moves to send cargo elsewhere, Ortiz said.
Producers and manufacturers of holiday items might be among those moving their goods to safer harbors on the outside chance that there are disruptions on the East Coast. One maker of artificial Christmas trees, garlands and wreaths told The Wall Street Journal that concerns about the negotiations caused him to move his goods from the Port of New Jersey to Oakland’s port.
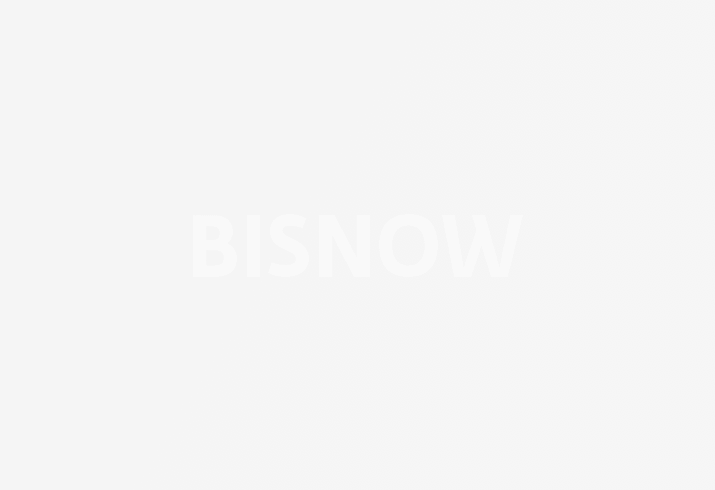
It’s a reminder that the contract end date comes as the shipping industry transitions into what is traditionally its busiest season. Retail sales have also been on the rise, increasing 0.1% in August after a 1.1% jump in July, according to Commerce Department data.
Among those who have not yet diverted any cargo are customers of George Goldman, president and North America CEO of CMA CGM, a major shipping, logistics and terminal operations company.
Goldman, speaking at the briefing last week, noted that when ships are diverted, it’s not his idea or his company’s. Instead, it’s at the request of customers.
“We, as an ocean carrier, do not dictate diversions,” Goldman said. “This is dictated and mandated by our customers. They're the ones that will tell us, if they want to divert, what supply chain channels they prefer to use.”
While his plans had not yet changed to account for the possibility of labor disruptions on the East Coast, he said he was hopeful for a resolution that avoids all that.
“One day is too long of a shutdown,” Goldman said.
Though the potential strike is likely top of mind for many in the logistics industry, it is far from the only consideration for shippers and their customers.
Seroka noted that geopolitical turmoil has heightened concerns about moving ships and their crews and cargo through the Red Sea, causing shippers to find alternative ways around the area. An ongoing drought in the Panama Canal has also played a role in high volumes to the LA area, Seroka said.
“All of this has really created a second look by supply chain experts as to how they want to route that cargo,” Seroka said.
It has only been a year since the ports of Southern California were dealing with their own labor strike. That effort, on the heels of an unprecedented pandemic-era backup and subsequent shortage of shipments, didn’t dent the area’s industrial performance.
During those labor negotiations last summer, the market was as strong as it had ever been, allowing it to absorb any impact that came with disruption at the port, preventing a dip in fundamentals in the surrounding markets, Ortiz said. There were effects on cargo, though, with the West Coast losing some volume it is now regaining.
Even in difficult times, port-adjacent industrial properties do better than the overall market, Ortiz said.
That vacancy at the 18 seaport markets that CBRE tracks was below the national average, and rents, which have remained relatively flat for industrial real estate nationally, are up about 4% for seaport markets alone.
“The major ports [the 18 CBRE monitors] are going to continue to thrive, because real estate demand should increase as the amount of imports to those ports does,” Ortiz said.