How One Chicago Developer Plans To Create More Sustainable Housing For Less
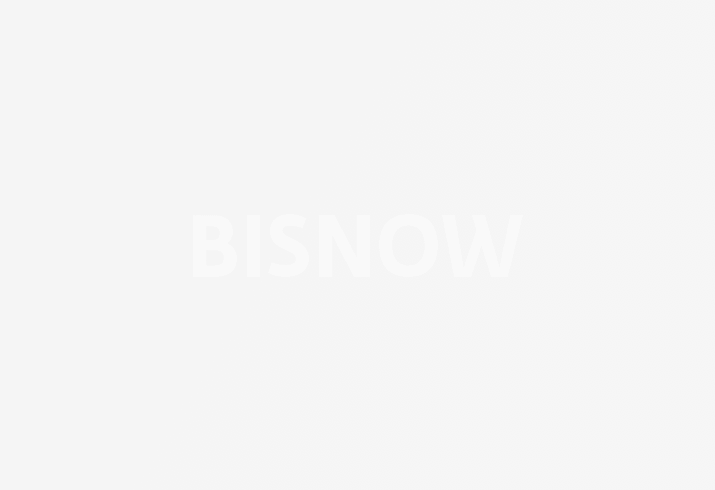
While major cities across the U.S. each face their own set of unique challenges, they all have one thing in common: They need to build more housing.
New York City’s own government website describes the city’s lack of housing as having reached a “crisis point,” while Los Angeles’ housing shortage is only getting worse in the wake of the coronavirus pandemic.
In Chicago, research from DePaul University’s Institute for Housing Studies has found that the city is rapidly losing its affordable rental units, and the pandemic is making it even more difficult to construct traditional multifamily assets.
Michael T. Thomas said he believes he has the key that can help cities unlock economic growth while reducing the construction industry’s overall environmental impact.
“Chicago and other urban areas need more economical housing, but it’s not enough to simply say, ‘Let’s build more houses.’ We also need to find high-tech new construction methods to erect buildings that are both cost- and energy-efficient,” said Thomas, who has been working in the residential and commercial real estate sector for 21 years and hosts The GreenPreneur Podcast, where he discusses living a more eco-friendly lifestyle.
Thomas has teamed up with several strategic public, private and philanthropic partners and investors to create a new type of multifamily development company that is focused on scaling affordable homeownership. Their first project will be a collection of two-to-four unit multifamily buildings in the Woodlawn Community in Chicago.
Bisnow recently sat down with him to learn more about this upcoming project and his vision for the future of multifamily housing.
Bisnow: What are some factors holding back the construction of more housing, particularly more sustainable housing?
Thomas: Traditional construction methods that rely totally on the conventional way of sourcing expensive building materials often lead to long project delays. This not only makes it difficult for cities to build housing to meet their current residents’ demands, but it also makes it nearly impossible for developers to consider using sustainable materials, which could take additional time and money.
Labor represents around 60% of the cost of a construction project, and [with] the attrition of specialized building tradesmen, finding ways to be more efficient on construction sites is more crucial than ever.
Bisnow: How can cities overcome these challenges?
Thomas: It’s time for developers and investors to think outside the box of conventional construction models and consider switching to a prefabricated, componentized model that uses fewer materials.
With prefab manufacturing, components of a building envelope are assembled offsite. Using this method, construction crews are able to assemble the final product 10% to 20% percent faster than with traditional on-site construction.
The walls, floors and roof components of our Woodlawn project are pre-assembled, without worrying about issues like weather conditions disrupting the construction process. With this method, a six-member crew can assemble a building envelope in three days.
Saving this much time can result in project stakeholders saving up to 20% of a project’s total cost. The savings from off-site manufacturing can help more projects pencil out and speed the pipeline of new projects, helping cities reach their goals for new housing creation.
Bisnow: How does sustainability factor into your plan?
Thomas: Along with being less costly and time-consuming, prefab construction models are also less expensive per square foot than conventional methods and use less materials.
In fact, research shows that prefab can reduce timber waste by up to 87%. This is due in part to the fact that since components are made in a factory, design changes are less costly and the factory can reuse any waste materials for upcoming projects.
We want to take things a step further and create prefabricated multifamily buildings using only two construction materials. Traditional timber construction methods can produce a massive amount of carbon emissions. We're doing our part to change that.
Bisnow: What are your upcoming plans?
Thomas: Our current objective is to make an impact on local communities across the Midwest. We will do this by not only bringing new buildings online faster and more efficiently but also by hiring local military veterans and reinvesting into the communities we serve. Our 100-lot demonstration project in Woodlawn Community here in Chicago will be located in an opportunity zone near the $500M Obama Presidential Library.
Currently, we are requesting limited partners and community leaders to join us if they are interested in sustainable development.
This feature was produced in collaboration between the Bisnow Branded Content Studio and The GreenPreneur.com LLC. Bisnow news staff was not involved in the production of this content.