Can’t Build Them Fast Enough: How Precast Concrete Meets The Speed-To-Market Demands Of Industrial Owners
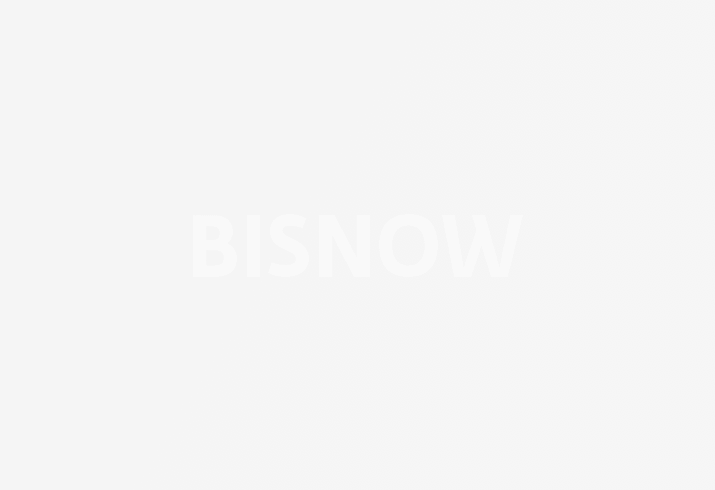
Once the preserve of workers on forklifts who moved pallets from 9-to-5, industrial buildings are increasingly automated and busy 24/7. Serving as vital supply chain links in today’s e-commerce-driven, omnichannel-focused and AI-enhanced economy, the U.S. industrial market added a record 89M SF in Q1 2023 alone, according to CBRE.
While CBRE noted that all of this new construction risks driving up vacancy, demand for industrial space continues to be strong in some regions. In the mid-Atlantic, for example, Pennsylvania’s Lancaster County benefits from its central location and easy access to numerous major East Coast hubs.
“People are often surprised to find out that Lancaster County has access to more people in a 200-mile radius than any other county in the U.S.,” said Melissa Reid, director of marketing for High Concrete Group, an architectural precast concrete producer serving the mid-Atlantic area, as well as the Northeast and Midwest. “Due to our proximity to New York City, Philadelphia, Baltimore and Washington, D.C., our prefabricated building solutions align well with the needs of the industrial sector in this region.”
Lancaster County also is close to the state’s I-81/I-78 corridor, which CBRE identified as one of the fastest-growing U.S. regions for industrial construction.
Reid said industrial customers value speed to market, which is an advantage of High Concrete’s precast concrete building solutions. Manufacturing at its headquarters and plant location in Denver, Pennsylvania, High Concrete can supply industrial customers with precast products that allow new building exteriors or structural components to be erected in days, rather than weeks, she said.
The process is also more sustainable and creates less waste than competitive building processes such as cast-in-place and tilt-up concrete.
“We manufacture in a controlled environment according to lean principles and we have very minimal waste because we know exactly how much we need to pour,” Reid said. “Also, we're able to substitute cementitious materials with more sustainable options, such as recycled glass, to decarbonize our concrete products while maintaining their necessary structural integrity. Our competitors doing cast-in-place or tilt-up construction out in the field don't have the environment to be testing and making improvements like we can.”
Fast construction schedules and improved sustainability aren’t the only priorities for High Concrete’s industrial customers. High Concrete Group Director of Sales Jamie Sweigart said other important criteria include cost, the availability and durability of the materials used and the aesthetics of the finished warehouse or distribution center.
Sweigart said precast performs well in all of those categories, particularly compared to alternatives like cast-in-place.
“Typically, precast concrete is competitive against any building material,” he said. “And because precast concrete is fabricated off-site year-round, it is not weather dependent like tilt-up. As many as 18 to 24 precast panels can be set daily, even during mild weather events, creating a very quick enclosure for the building.”
Longer-term, advantages of precast include its durability and resilience in the face of harsh weather.
“Precast concrete is fire rated with its thickness and composition, and it can be designed for severe winds, blasts, seismic events and even flood loading if required,” Sweigart said. “It also serves as a rain barrier, not a rain screen like many other enclosure systems. It does not allow water to penetrate through the panels. Instead, the water hits the surface and runs off.”
Insulated precast wall panels can reduce energy consumption while providing high R-values, a measure of a material’s thermal resistance and a factor of particular concern for food distributors.
“With today's new codes, almost all buildings require higher R-values and continuous insulation from edge to edge, and precast provides both,” Sweigart said. “Increased R-value also can reduce the size of the HVAC units needed, further reducing costs for the building owner or tenants.”
Other advantages include low maintenance costs and a component life span of 75 to 100 years, he said.
If building owners or developers want to get the full benefits of precast, they should include the precaster early in the design process, Sweigart said. That way, they might be able to shave months off the project schedule.
“The misconception that if ‘I don't bid the project, I don't get the best price’ is absolutely incorrect,” he said. “In fact, I would argue that owners are getting a higher price when they bid out a project, due to all the redesign that will be required once the key trade partners, including the precaster, are on board. It’s much more efficient to have the precaster involved at the start and working hand in hand with the designers.”
This article was produced in collaboration between High Concrete Group and Studio B. Bisnow news staff was not involved in the production of this content.
Studio B is Bisnow’s in-house content and design studio. To learn more about how Studio B can help your team, reach out to studio@bisnow.com.