Construction Industry Hones In On Carbon Reduction To Build Greener
Challenges seem to mount for the construction industry with each passing year, most recently in the form of sky-high fuel costs and a nagging labor shortage, but operators are still chipping away at their decades-old quest to reduce their impact on the climate.
As an industry that fundamentally relies on the production and implementation of raw materials to create the built environment, construction has a big part to play in determining how green the future of real estate will be, a question that factors into society’s larger existential questions as climate change persists.
"We have industries because there's a planet on which to do commerce," Skanska Senior Director of Business Development for Georgia and South Carolina Jimmy Mitchell said.
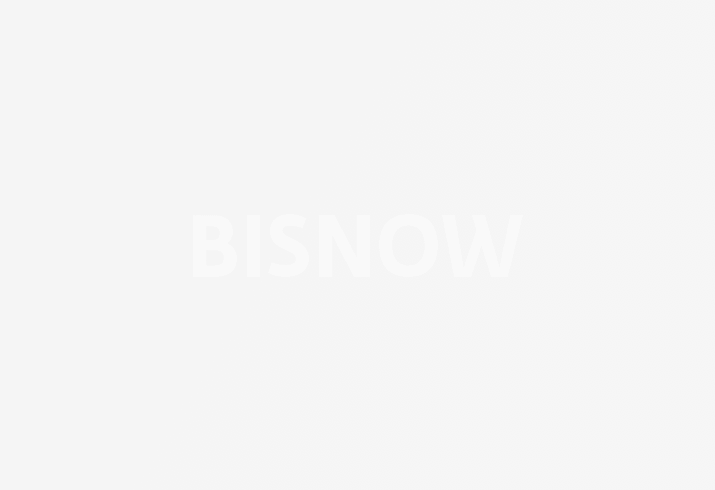
And while political spats, court decisions and international conflicts complicate the path to a greener future, some construction companies are taking it upon themselves to plow ahead.
"If policymakers don't want to do it, the construction industry needs to do it," Mitchell said, referring to taking the carbon out of the construction process. "Policy might catch up anyway — in which case it would be good for construction to be a leader in decarbonizing."
Reducing carbon emissions from building operations has been a policy and industry goal for decades, but only in recent years has the construction industry focused on cutting emissions from the actual building process.
The decarbonization movement in the industry is gathering steam, under pressure from not only regulators, but also investors and activists, responding to the fact that the construction industry is responsible for about 20% of annual carbon dioxide emissions worldwide, according to the Energy Information Agency. Building operations, meanwhile, contributed 27%, according to the same report.
Even the recent Supreme Court decision restricting the U.S. Environmental Protection Agency's power to regulate carbon emission won’t slow the push for more sustainable construction, experts say.
A survey by SAP and Oxford Economics found that 58% of respondents said that their companies have reduced their energy consumption in recent years.
But the process of lowering construction carbon emissions will be a long slog with a number of hurdles, according to contractors. Some 47% of the SAP respondents said that increased process complexity is an obstacle to meeting sustainability goals, while the limited availability of needed resources is also likely to be an obstacle.
Even so, contractors are looking to cut carbon emissions, including with the use of new technologies and materials.
Skanska USA Building, for example, now provides carbon assessments on every new construction project over 53K SF using a tool it co-created called the Embodied Carbon in Construction Calculator, or EC3. "Embodied carbon" is the term that describes carbon emissions in every step of the construction process.
"It's a free tool, and anyone can use it," Mitchell said, adding that during the pilot phase of using the tool, it showed that a 30% reduction in embodied carbon is usually achievable for little or no cost.
Sourcing low-carbon concrete is a recent and growing trend among construction companies.
"Low-carbon concrete is definitely something that can have a measurable impact on reducing carbon emissions in construction," PCL Director of Sustainability Scott Beckman said. "We've been actively deploying those kinds of products on some of our projects, creating our own internal guidance documents to support our teams in understanding how to specify the material."
One of PCL's first uses of low-carbon concrete was on a project at Calgary International Airport, with a savings of more than 25 pounds of carbon emissions per cubic meter, or about 35 cubic feet, of concrete.
And in Chicago, McHugh Concrete is trying out a concrete mix developed with Oremus Material that replaces as much as 60% of more common cement types that emit higher concentrations of carbon. Instead, the mix uses slag from blast furnaces and fly ash from coal-fired power stations, improving sustainability by using recycled materials and reducing carbon emissions.
McHugh is using the concrete at Reed at Southbank, a 41-story residential tower.
"The Reed's total embodied carbon for concrete was reduced by over 32% compared to industry standard mixes, and exceeded project specification requirements by 14%, according to our testing," McHugh Engineering Group Director of Engineering Eamonn Connolly said.
At Claremont Hall in New York, which is being built by Lendlease, reduced-carbon concrete and steel led to a 32% overall reduction of carbon compared with traditional materials, Lendlease Director of Sustainable Construction-Americas Amanda Kaminsky said.
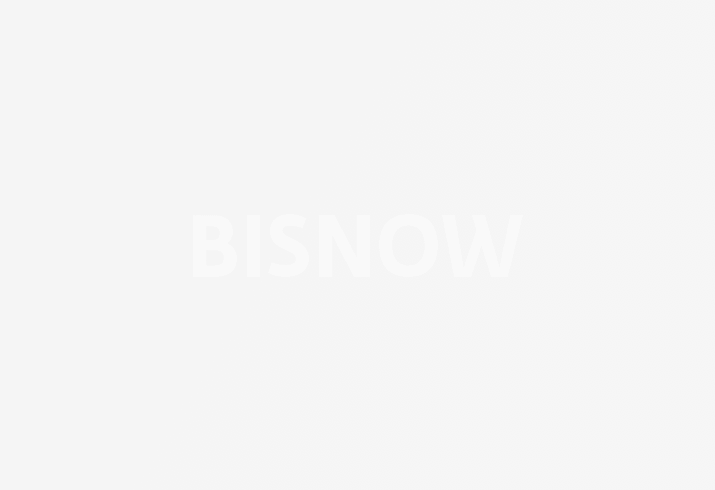
The industry is also adopting liquid-applied roofing technology, a coating that can be applied to most roofs. When it cures, it forms a rubber-like, seamless waterproofing membrane that also cuts carbon emissions.
"We're now installing liquid applied roofing technology on commercial roofs, which helps reduce landfill waste," Western Specialty Contractors St. Louis Roofing Branch Manager Keegan Tune said.
The tech can be applied over most traditional roofing materials, reducing the amount of tear-off roofing waste dumped in local landfills, Keegan said.
Reducing the carbon footprint of construction equipment is also a critical part of emission control for the industry.
"We are in phase 2 of a pilot program to test new to-market electric and hybrid equipment," Turner Construction Chief Sustainability Officer Julie Gisewite said. "The program is collecting data on a large project in the Midwest on how the equipment will not only perform environmentally, but offer Turner savings on fuel and labor, two critical issues facing the construction industry in a time of fuel inflation and labor shortages."
The team has piloted an electric mini-excavator, forklifts and utility terrain vehicles, as well as hybrid excavators and light towers, she said. The data from the pilot will be used to inform decision-making to reduce the greenhouse gas emissions in Turner's operations.
"We have found, for example, that battery hybrid generators need to run less and work more efficiently when they are running, resulting in a quieter environment, fewer refueling events and a lot less emissions," Gisewite said.
The company has also implemented a “no idling” standard for its job sites that disallows idling by all vehicles within the construction fence. Reducing the idle time of a Class 8 engine by one hour per day can save more than 7,000 pounds of carbon dioxide emissions and $1K or more in fuel costs per year, Gisewite said.
Other simple changes, like Costa Mesa, California-based Kazoni Construction’s decision to go almost entirely paperless, can make a big difference by reducing consumption over time.
"Pretty much the only thing that we print is a hard copy of blueprints for the job site," Kazoni Construction President April Kulpinksy said.
Though it’s a long road with challenges that simply add to the stack of problems the construction industry must solve, firms that are working to reduce their emissions and materials use get in on the ground floor to reduce a property’s ultimate impact on the environment.
"When you look at the overall life cycle of a building, carbon embodied in its materials becomes much more an area of focus as operations become more efficient," PCL’s Beckman said.
UPDATE, AUG. 2, 1:38 P.M. ET: This story has been updated to clarify the relationship between McHugh Concrete and Oremus Material.