Construction Price Inflation Hits Critical Level As Developers Report Delays
Escalating construction material prices have moved from painful to chokepoint and are now widely delaying or derailing commercial real estate projects nationwide.
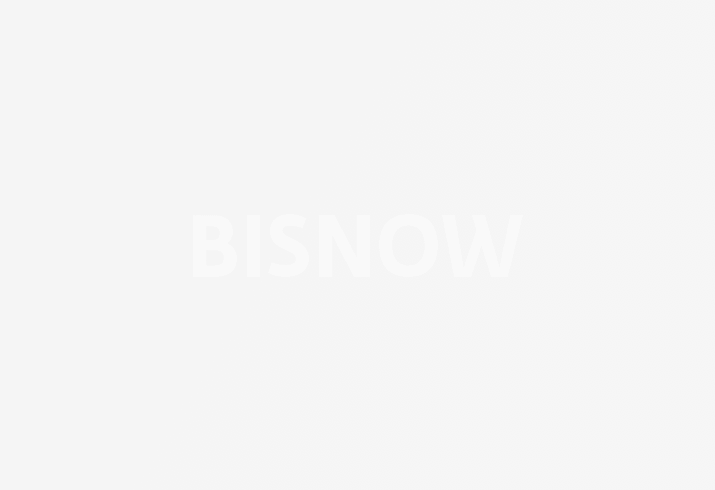
"Pretty much you name it, it is going up in price — sometimes to record levels," Associated General Contractors of America Chief Economist Ken Simonson said. "I've been AGC's chief economist for almost 20 years and have never seen so many things go up so frequently and steeply at one time."
Lumber, steel, plastics, gypsum, wallboard, insulation and cement are all seeing prices escalate, causing heartburn for developers and contractors, Simonson said. Prices for lumber and plywood spiked 86% from April 2020 to April 2021, data from the U.S. Bureau of Labor Statistics shows. Steel mill product prices jumped 67% during the same period, while copper and brass mill shapes rose 49%. Aluminum mill shapes also increased 20%, while gypsum prices inflated 12% during the same period and plastics jumped 14%, according to BLS data.
Input costs for general contractors, a line item that accounts for how much GC's are having to spend on purchases, rose 19% year-over in April, up from the 12.4% annual increase recorded just a month earlier, according to AGC data.
Ballooning costs are increasingly having a direct impact on whether projects get built.
Fifty-six percent of multifamily developers surveyed by the National Multifamily Housing Council between May 17 and June 1 reported delays caused by rising raw material prices and the overall economic infeasibility of new projects.
That number, which is from a survey of 109 apartment development firms, is up from NMHC's last survey, completed in March, when roughly 30% of developers said they had apartment projects delayed by cost concerns.
"NMHC’s Construction Survey shows there's continuing volatility in apartment construction conditions," NMHC Vice President for Research Caitlin Walter and Vice President for Construction, Development and Land Use Policy Paula Cino said in a statement.
Even though difficulties in obtaining permitting, entitlements and professional services remain the most onerous barriers to new apartment development, rising construction costs are now playing a substantial role in slowing the trajectory of multifamily projects.
"Our results show a jump in delays caused by economical infeasibility since our last survey," Walter and Cino added. "It’s clear that any delay in getting materials could mean a delay in actually finishing a project if a substitute can’t be found."
Texas developer Artemio De La Vega with De La Vega Development is watching raw material prices skyrocket as his firm builds The Central mixed-use development in Downtown Dallas. The longtime developer blames the sharp price hikes on supply chain interruptions during the coronavirus pandemic, but also on federal policies that are making oil/petroleum and other materials such as roofing, piping and asphalt more expensive.
As a result, developers either have to eat the difference in material costs upfront or pass them on to the end user.
"Developers will have a harder time making the pro forma work unless they are able to get an increase in rent," De La Vega said. "Inflation in construction materials is a difficult proposition that requires economic expansion and growth to underwrite the price increases, otherwise developers may sacrifice on the quality of the building to get the project built or not build it at all."
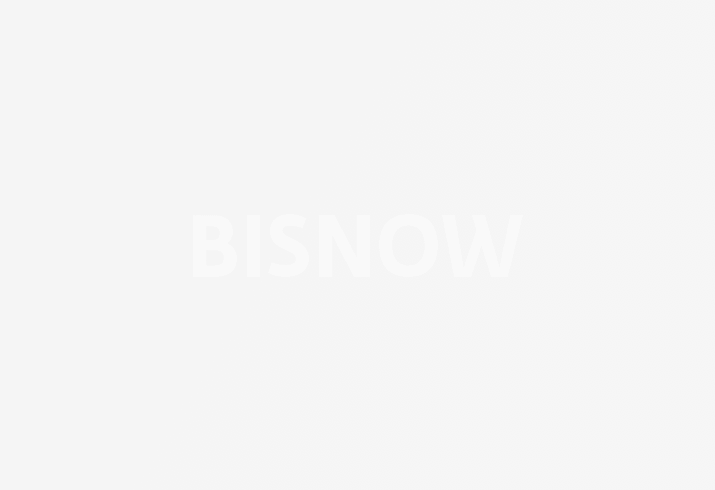
Experts studying the issue say there's no easy solution to the rising cost of raw material prices.
At least part of the problem started four years ago when the U.S. imposed new tariffs on imported materials, and it reached a crescendo when the pandemic interrupted the smooth operation of supply chains from China in 2020.
"Back in April 2017, the U.S. enacted 24% tariffs on lumber purchased from Canada, so what happened is that dramatically slowed down demand," said Thomas CEO Tony Uphoff, who runs a platform for product sourcing and supplier selection. "In response to that, Canadian mills actually closed locations because they were acting on the supply and demand shift."
When supply chains became gridlocked in 2020, other alternative suppliers like China, and even parts of the U.S., could not easily make up the difference in lumber deliveries, he added.
Increased demand for housing during the pandemic added more fuel to the fire, making lumber and other construction material prices skyrocket.
The only solution is some government involvement and waiting for the once gridlocked supply chains to catch up to their pre-pandemic levels.
"We have been working to get the administration to drop these tariffs since shortly after President [Joe] Biden took office," AGC's Simonson said. "We sent a letter in February, highlighting the lumber tariff and the problem it is causing not just for contractors but for the administration's goals for affordable housing and infrastructure."
So far, there has been no concrete action by lawmakers to combat skyrocketing construction prices, Simonson said, but AGC has held what he characterized as meaningful discussions with administration officials.
Spiking demand for residential housing lumber has also contributed to supply shortages for commercial development, and another solution may be waiting for that demand to even back out.
"You are going to see this constriction for probably the next 12 to 18 months," Uphoff said. "What's unclear from any of the folks that track this is how much of this boom of residential housing real estate development will last."
Meanwhile, the construction and development industries are having to make some strategic calls around timing and the worthiness of certain projects.
"Clearly, this situation is unsustainable," Simonson said. "Contractors can't afford to absorb all of these increases, so they will either withdraw from the market, or some may actually go out of business, or they will find owners who are willing to pay more in order to get a project done."
CORRECTION, JUNE 15, 3:27 P.M. CT: An earlier version of this story incorrectly said Thomas, run by CEO Tony Uphoff, specifically serves the real estate industry. It serves multiple industries. The story has been updated.