Data Center Developers Wrestle With Materials Costs, But Find Ways To Cope
These are heady times for data center development, with demand for product as high as it has ever been because of the world's insatiable appetite for data.
But these aren't perfect times, according to developers and contractors who specialize in the product type. The industry is dogged by increasing materials costs for construction and equipment that are growing as much, or more, than the rest of the construction business. Some in the industry are tying part of the increase to tariffs.
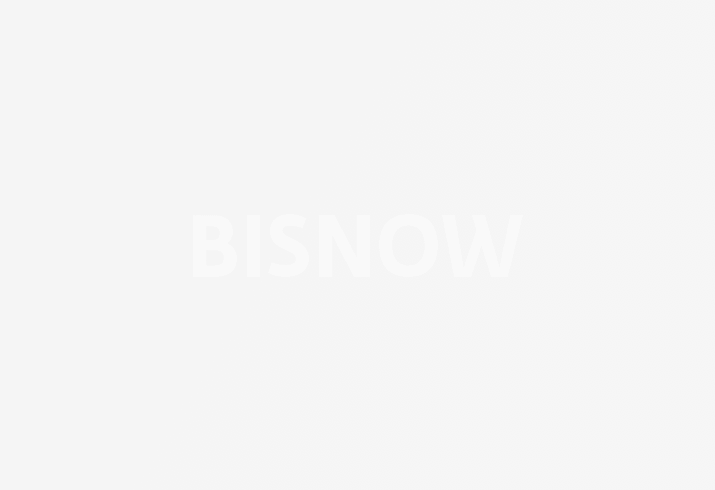
"The cost of materials, such as items made from copper and steel, has gone up particularly fast recently, in part we believe because of tariffs," Cyxtera Technologies Vice President, Product and Data Center Strategy Mitch Fonseca said.
"The cost of the equipment we use has also gone up, whether it's assembled in the United States or not."
Miami-based Cyxtera is a major owner of data centers, with a global footprint of 57 facilities, and is rapidly expanding. This year, the company is expanding its existing data centers in Silicon Valley, Phoenix, Atlanta, New York and Toronto to meet customer demand for co-location infrastructure.
"Development costs are up, but mostly on the material side of the business," ServerFarm Vice President of Engineering/Construction Sam Brown said. "It's tough to pinpoint a specific tariff as the reason, but tariffs and government trade positioning seem to be part of the reason. Even talk of a tariff can impact the price of materials."
The hot construction market as developers rush to meet demand is also affecting what they are paying. According to CBRE, surging demand from hyperscale cloud providers led to a record 303 megawatts of data center absorption in the seven primary U.S. data center markets in 2018, and another 500 MW are in the pipeline.
"The demand is crazy for products using copper and galvanized steel, which form important components in data centers," Brown said.
ServerFarm's assets are in metro Chicago, Atlanta, Washington state, the U.K. and Canada. The company develops new facilities, but also acquires existing underutilized data centers as value-add plays, remaking them into updated multi-tenant environments.
Nonresidential construction input prices overall were up 2.8% in April compared with a year earlier — a bit ahead of inflation — but prices for inputs using some metals accelerated more quickly, according to Associated Builders and Contractors' analysis of Bureau of Labor Statistics data.
The price of steel mill products, for instance, was up 5.8% year over year, and fabricated structural metal products were 3.9% more expensive than a year ago. Other metal-based products didn't increase so much, or at all: nonferrous wire and cable dropped 0.2% year over year in April.
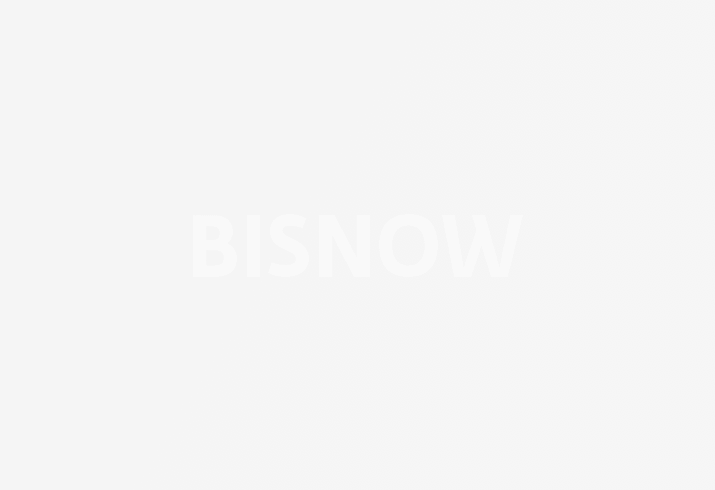
Costs for data center developers and contractors also vary considerably according to market. For example, recent material cost increases in the Chicago market were relatively modest. Structural steel and metal decking prices, for instance, were up 1.2% quarter over quarter in Q1, according to Mortenson Construction.
By contrast, structural steel and metal decking increased 5.9% in price in the Seattle market, where frenetic growth and high demand for materials is spurring construction costs as a whole to rise above historic averages.
Labor is another factor in rising costs for data centers, though not as much as materials on average nationwide, according to data center construction experts. The impact of labor costs on data center construction is much more localized.
"In some regions, where hyperscalers are building at an explosive rate within a small geographic area, there's a dramatic shortage of skilled trade labor," Page principal for science and technology John Major said. Page is a global architecture and engineering firm based in Austin.
"Hyperscale builders are competing with each other to attract subcontractors and skilled labor to commit to work on their project campus instead of their competition’s project campus," Major said. "I’ve heard that one contractor resorted to paying each laborer $100 per day just to show up at their project instead of the competing project."
"The skill sets are in high demand, and there are more construction companies focused on data centers now," Fonseca said. "In some markets, such as Santa Clara, California, contractors are so busy that if you want them to prioritize your project, that will come at a premium."
There is also a shortage of design professionals and data center operators, Major said.
"Architects and engineers struggle to find and hire qualified professionals in the data center industry, which limits the amount of design work we can take on with short notice," he said.
A number of universities are now offering courses in data center design and operations, such as Southern Methodist University’s master's degree in datacenter systems engineering. Major said that is a welcome development.
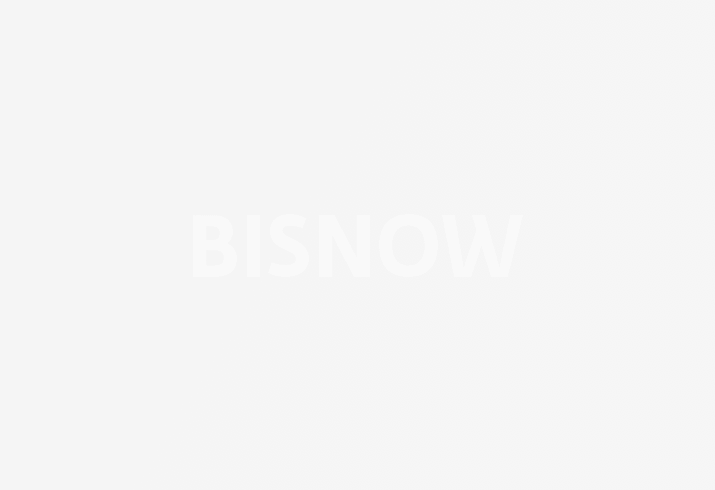
In the face of higher materials costs, and sometimes higher labor costs, what are developers and contractors doing to bring data centers in on time and on budget?
"You need strategies for dealing with unpredictable costs, and to be in constant contact with your supply chain," Brown said. "You can't assume there will be a standard 2% to 5% increase in any material cost, or any cost, from year to year. Planning is more critical than ever."
Most developers have devised a standard data center design with minimal variations, but which can be site-adapted to various climates and geography, Major said.
"By doing so, they have a good baseline for construction costs and construction schedule when they deploy future projects. Variations to the standard design have the potential to introduce risk to the budget and schedule, so the developers drive towards standardization and consistency across their portfolio," Major said.
Once a standard design has been established, developers can procure equipment well in advance of construction activity to reduce speed-to-market, Major said.
"There is a growing trend in the data center market towards a more integrated delivery model, which eliminates the traditional hierarchy and favors increased collaboration from project inception through project execution," Southland Vice President Tim Michael said.
Southland is a mechanical, electrical and plumbing contractor with a data center specialty, among others.
Paramount to an integrated delivery model are partners who understand more than their assigned scope of work and who can operate in an environment that is centered around a “what’s best for the team” approach, Michael said.
"The model focuses on choosing partners (not bidders), building teams and aligning goals through an integrated form of agreement," Michael said. "The outcome is one which challenges the team to think and behave differently, but that drives waste out of the process to reduce cost and increase speed-to-market."