Construction Firms Look To Build A Better Job Site With New Technology
Construction productivity has been on the decline for decades. The labor shortage has cut into delivery times, forcing contractors to look for ways to do more with less. While contractors have been slow adopters of real estate technology, some firms have learned to adapt, turning to virtual reality and other related technology to get the job done.
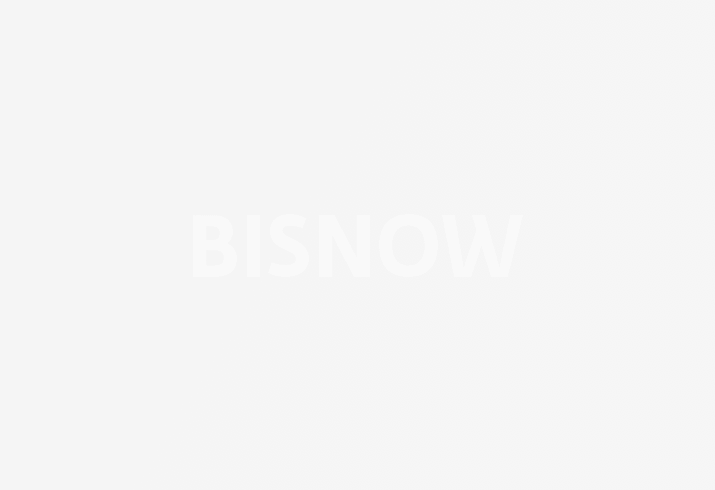
“We noticed over decades, efficiency and productivity have declined,” Suffolk Regional Manager in San Francisco Michael DiNapoli said.
The need for more technological advancements grows more dire every year. The labor pool has shrunk 23% since 2007 and material costs have increased 10% over the last five years, according to JLL.
Over the last six years, nearly $10B has flooded the construction technology industry to fund innovations from robotics and cloud technology to augmented reality and smart helmets. But it may take about five to seven years for the technology to be commercially available to the industry, and two decades before new technology and robotics are widely used in the market, MIT Real Estate Innovation Lab Director Andrea Chegut said in a JLL report.
In the meantime, companies like Suffolk Construction, Mortenson Construction and Pankow are testing their own innovations and new technologies.
Suffolk has been rolling out Smart Labs at its various offices, including those in Boston, San Francisco and New York City, to explore new technologies from virtual and augmented reality to building information modeling and production tracking software. Additional labs will open in Los Angeles, Miami and Tampa. These labs allow team members to sit with clients and partners to better collaborate on planning, design and construction.
“We believe our Smart Labs are on the front lines of an industry disruption that will change the way buildings are designed and built, and we are excited to reinforce a culture of invention and curiosity — both in our own people and within the industry,” Suffolk Executive Vice President and Chief Innovation Officer Chris Mayer said.
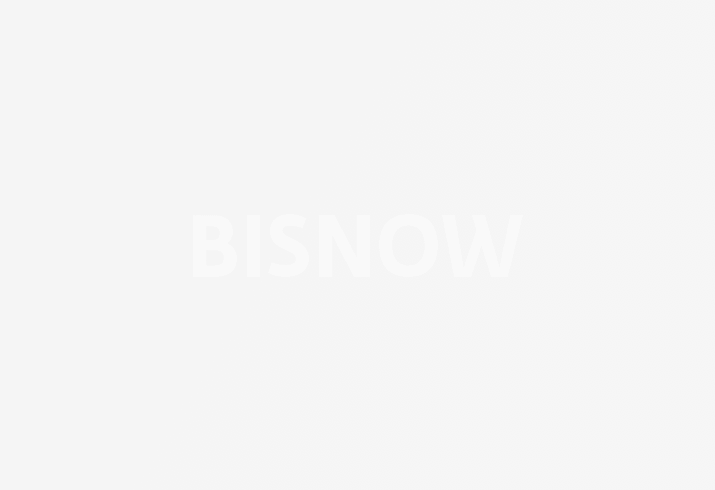
The Smart Labs allow Suffolk to test tech in real-life scenarios to see if it is increasing productivity and making the work easier, according to DiNapoli.
The lab in Boston will be more heavily focused on research and development and augmented and virtual realities, DiNapoli said. The Los Angeles office is testing a job site security program, which uses facial recognition and badges to track who is on the job site. The New York office is piloting a geotagging program and is using a platform that can recognize and tag personal protection equipment. It will build a pattern and send out notifications if workers are not wearing the proper equipment, according to DiNapoli.
Though each of Suffolk's labs has a different specialty, each includes a data wall that projects predictive analytics and operational performance indicators onto a wall so team members can view and measure different areas. A huddle wall integrates 3D, 4D and 5D models for closer collaboration during planning meetings.
In addition to the data wall, a virtual reality cave offers a room where teams can view the future of construction by immersing into virtual models. Since team members can essentially step into their models (as seen in the above video), architects and project teams are able to identify and address logistic challenges before construction begins.
For its 1700 Webster St. project, Suffolk developed VR to showcase the model of the building while under construction. The building also will incorporate a new HVAC unit called Jaga, a product from Europe that has not been built in the U.S. before. The VR can pull apart the HVAC unit so team members can see how the unit comes together and how it fits flush with the wall, according to Suffolk VDC Manager Michael Kasovski, who runs the Smart Lab in San Francisco.
Tracking And Improving Productivity
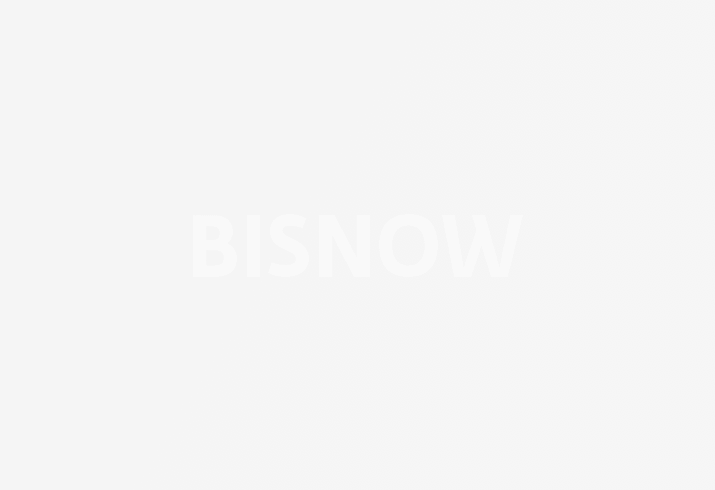
To increase productivity on construction sites, Suffolk's San Francisco office developed a plan-and-control model. This model allows for Suffolk to be involved in the design early in the development and construction process since it is much more difficult and costly to change design later in the process.
If a team is working on a deck and realizes the plans and units are not fitting, it may stop and ask the question about the plans, or it may guess. DiNapoli said the strategy, called plan and control, attempts to avoid this problem altogether because the plans have already been worked through prior to construction.
Suffolk tested plan and control during its build of Equity Residential’s 340 Fremont, which was built in 27 months. That project used prefab walls and the models were so accurate they cut down on contingency use dollars, DiNapoli said. With Suffolk involved in pre-construction, it was able to pick subcontractors, locking in pricing early, according to the San Francisco Business Times.
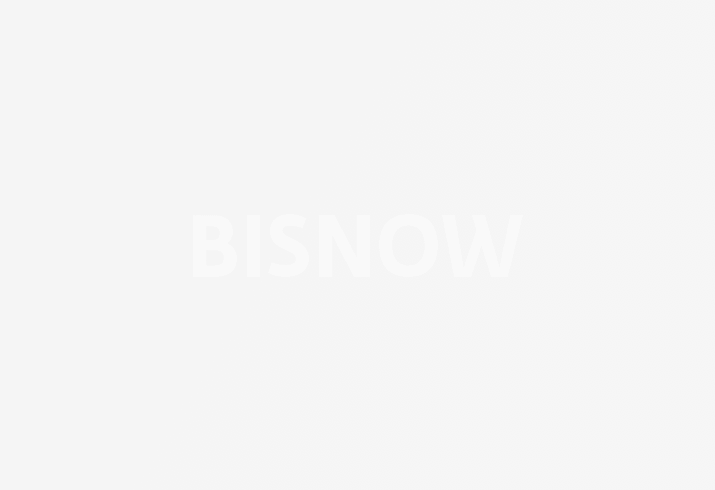
“We’re returning contingency dollars and using less staff on projects,” he said. “Designers are spending less money on construction administration as well.”
In addition to plan and control, Suffolk also has been using design pull planning, which essentially creates swim lanes for each person involved with the project. They put in notes on what problems or challenges need to be overcome allowing other team members to keep track of the progress.
Suffolk also is testing Tableau, a data analytics platform that creates project scorecards for various construction teams so managers and/or supervisors know where to improve productivity.
How Tech Can Collect Building Information
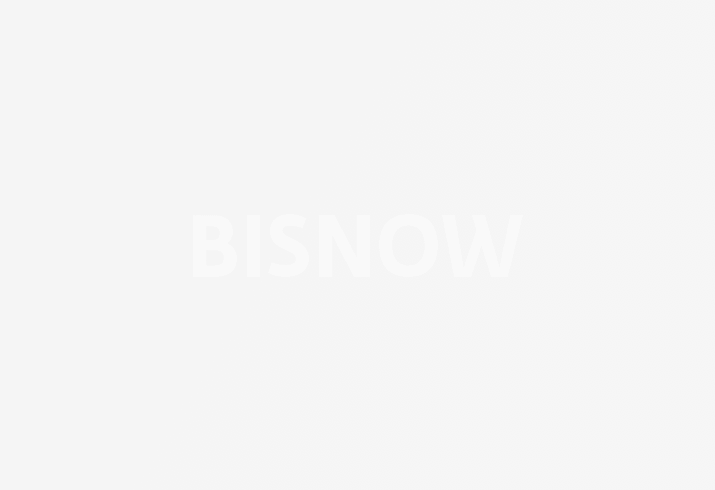
Tech companies also have stepped up to provide better ways to track through building information modeling (BIM) and document allocation. Stereograph uses a cloud-based platform for structural engineers, designers and others to upload plans to a building so that it is all in one location, according to Stereograph Country Manager Thibault Thomas.
“More and more buildings have a BIM file and it often goes to the trash can after the project is finished,” Thomas said.
The platform will keep a BIM file updated through the process and provide building owners with a 3D model after the project is complete. This model can be used to implement smart technology and track building operations as well. The software can work with building temperature controls and motion sensors to let users know which rooms are occupied to make sure the room is not too hot or cool.
Technology is also being used to document job sites and keep track of a project’s progress. Multivista will document every phase of a build to provide an index of photos in the cloud. The firm also offers 3D navigation of a job site that allows users from all over the world to access job site information remotely, according to Multivista account manager Robert Canali.
This technology has helped with the proof of scheduling, trackability and subcontractor accountability. It also helps contractors figure out where a problem lies with a fixture or another part of the construction project by going back and looking at the photos to see which fixture may have been built incorrectly instead of going through each fixture on the job site.
As more technology is adopted, more construction firms will be able to deliver products on time and with fewer mistakes.
“Everyone is trying to solve the productivity problem,” Suffolk's DiNapoli said. “The industry is hampered by productivity and cost.”