How Swinerton, A 133-Year-Old Company, Plans To Usher NYC Into The Post-Pandemic Era
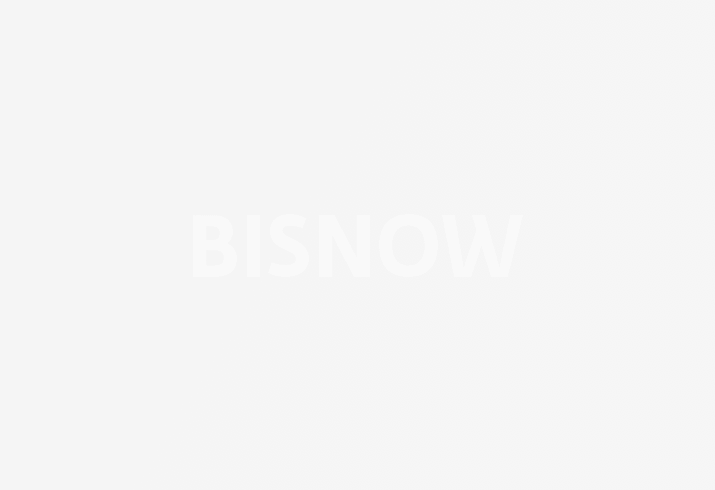
New York City’s construction industry is ready to rebuild following the setbacks caused by the coronavirus pandemic, but something is standing in its way. The city’s building sector remains 25,000 jobs below its pre-coronavirus peak, despite the fact that it was one of the first industries allowed to resume business following the first shutdown.
Carlo Scissura, chief executive of the New York Building Congress, told The City in June that “In the wake of such a challenging and devastating period, the building industry is primed to lead the recovery across our country.”
The fastest way to restart New York’s economy, he added, is through large-scale infrastructure projects supported by the federal government. But who will build these projects if the city is struggling to find skilled construction workers?
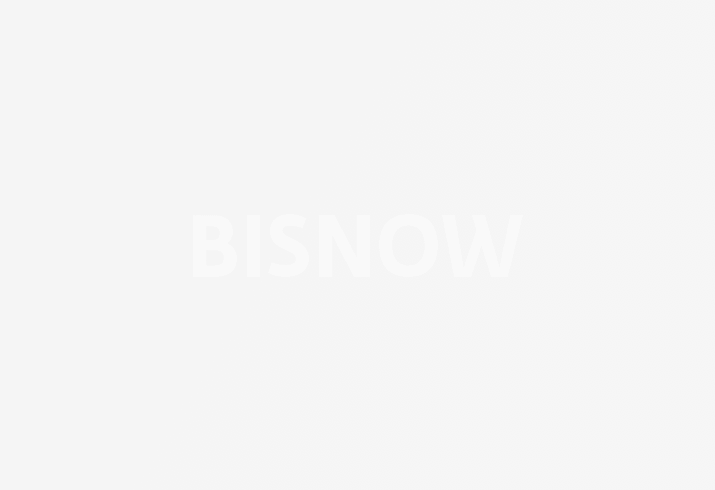
The answer may lie to the west, toward a California-based company that recently made NYC home and is working to bring innovative building solutions to the city.
“Swinerton has always built differently,” said Andrew Pearl, vice president and division manager at Swinerton, a 133-year-old construction company that recently opened a New York office. “Now, we want to bring what makes us different to New York City, to answer the call to build back better.”
Since its founding in 1888, Swinerton has grown into a $5B, 100% employee-owned company with 4,800 employees and more than 2,400 craft carpenters and laborers. Its diverse employee base gives the company the ability to self-perform many jobs other firms would have to outsource, including cleanup, concrete, drywall, demolition, doors/frames/hardware, electrical, rough carpentry, millwork and associated scopes.
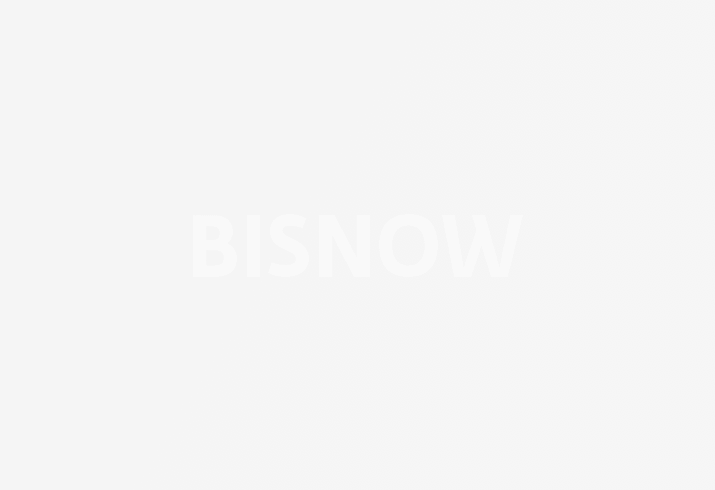
Along with that, Swinerton specializes in new building materials, techniques and tools that have been transforming the construction industry. Pearl spoke with Bisnow to highlight some of these innovative techniques that the team is hoping to use to rebuild NYC in the wake of an unprecedented year.
Taking Mass Timber To New Heights In Interiors
Mass timber refers to a variety of engineered wood products used in construction, including cross-laminated timber and glue-laminated beams. Mass timber construction has grown in popularity thanks to its cost and environmental and aesthetic benefits, but it has not been used as commonly in NYC as it has been on the West Coast. Swinerton’s New York team will bring the expertise of Timberlab, its mass timber delivery and integration company, to the Big Apple.
“Timberlab builds off of our general contractor experience to holistically integrate mass timber into a commercial building by carefully coordinating the timber structural system with the other building systems,” Pearl said. “For interiors, the beauty of mass timber is in the simplicity of the system, both its structure and finish, and it can be used as an alternative to steel and concrete with one-fourth of the weight and less environmental impact.”
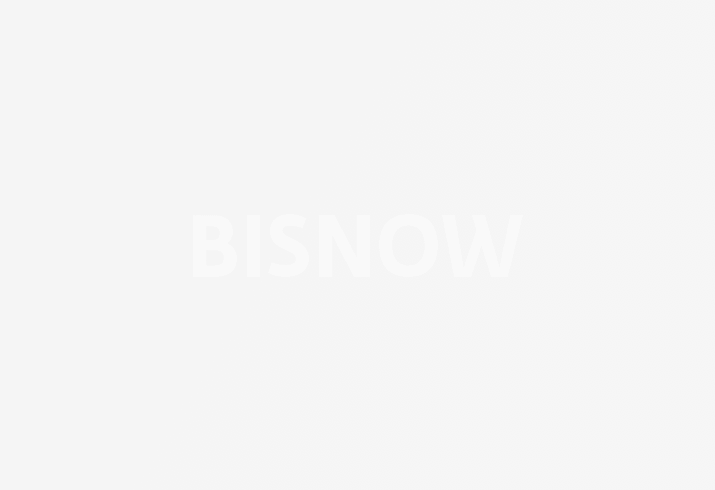
Leveraging Tech Trends And Expertise
Swinerton has a large portfolio of West Coast-based tech clients, Pearl said, and the company plans to bring its experience working with the latest tech trends to the country’s second-largest tech center: NYC.
“Current trends include shifting beyond a flexible work environment filled with amenities to one where teams can choose where and how they work, as well as a focus on workplaces that are more sustainable as well as equitable and inclusive,” Pearl said. “These trends stem from big tech’s commitment toward carbon neutrality on all aspects of their businesses, as well as developing a workplace that better reflects the values of their global workforce.”
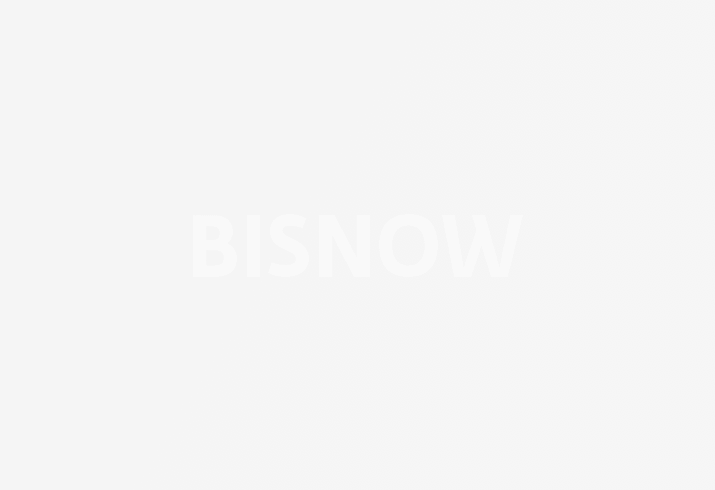
Bringing The Latest Technology To NYC
Swinerton strives to be a better builder by encouraging innovation and technological solutions to address building problems and challenges, Pearl said. The company holds two innovation competitions per year and partners with outside firms to create products that make building faster, safer and more cost-efficient.
Swinerton partnered with Canvas, a construction robotics firm, to develop the first drywall finishing robot. A process that normally takes three to five days to complete can be reduced to two days with the robot.
Swinerton’s drywall group partnered with Dusty Robotics to bring an autonomous robot that prints digital building models directly onto the floor of a construction site. Additionally, the company’s innovation team designed a pilot project for validating the feasibility of automating data capture on job sites. Working with partners Boston Dynamics, Avvir, Kaarta and Stanford’s CIFE program, Swinerton is able to accurately measure the quantity and quality of work in progress. From this data, it is possible to speed up schedules, generate quantities for payment applications and measure the quality of work.
In-House Virtual Design And Construction And BIM
Pearl said Swinerton’s in-house virtual design and construction/building information modeling team has hands-on experience in implementing prefabrication methods for plumbing, electrical, mechanical and fire sprinkler systems as well as framing/drywall and concrete formwork.
“What sets Swinerton’s BIM team apart from competitors is its understanding of what it takes to successfully implement BIM on a project that allows the trades to prefabricate their systems and streamline the installation process,” Pearl said. “This method not only saves time, it ensures what was coordinated during the BIM process is what gets installed in the field. We’re thrilled for the opportunity to bring skills like this, and our 133 years of experience, to the NYC market.”
This article was produced in collaboration between Swinerton and Studio B. Bisnow news staff was not involved in the production of this content.
Studio B is Bisnow’s in-house content and design studio. To learn more about how Studio B can help your team, reach out to studio@bisnow.com.