The Rise Of The Prefabricated Building
Developers, general contractors and subcontractors swap stories that sound too good to be true about prefabricated construction: a student housing project that cut its delivery time by a third or a hospital that installed hundreds of bathrooms in three days with only five laborers. Though the practice of off-site construction dates back thousands of years, the last real estate cycle has pushed prefabricated construction to prominence.
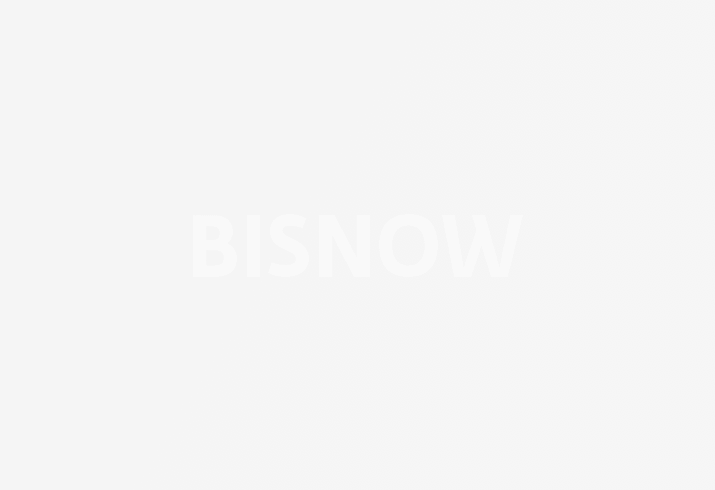
“We think the recession actually benefited our industry,” Modular Building Institute Executive Director Tom Hardiman said. During the last recession, many skilled laborers left the construction industry and did not return, Hardiman said. That, coupled with developers needing to find greater efficiency, made prefabricated buildings more appealing.
“The construction industry is very reluctant to change. When things were going well, developers and general contractors may not have felt the pain or need to change,” Hardiman said. “Now they do, and there’s no turning back.”
Off-site construction, also called prefabricated or modular construction, allows various building elements — anything from bathrooms to pre-wired light fixtures to exterior walls — to be built in a factory and transported to a construction site.
“We’ve found it helpful to think about modular as a construction process rather than a specific type of building,” Hardiman said. “It describes how the building was constructed, not what the building is.”
One downside to constructing off-site is decreased flexibility to update buildings in the field.
“What we’re talking about doing is rethinking decisions that are made too late and advancing them upstream,” DPR Construction Project Executive and National Prefabrication Leader Zach Murphy said. “[Prefabrication] isn’t good for making last-minute changes, but it’s about making those decisions earlier.”
DPR also uses virtual design and construction, a type of computer modeling, to solve problems with subcontractors and building partners in the virtual world before building in a factory or in the field.
But that loss in flexibility once ground is broken makes it imperative to commit to design, Trammell Crow principal Jeff DeBruin said.
“For instance, if you add prefab racks in your restrooms, and then at the eleventh hour you want to add another sink, your racks are no longer useful. You’re banking on consistency and redundancy, and any changes make you less adaptable.”
When done correctly, off-site construction can benefit a project’s schedule, budget and skilled labor requirements.
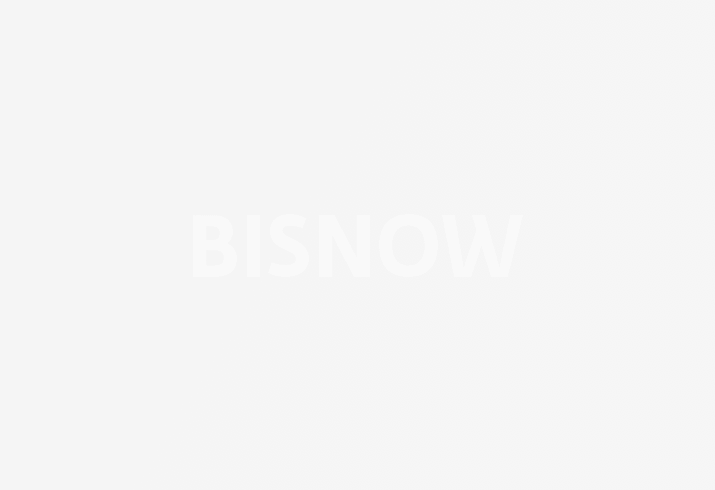
“When you just prefab for sake of prefab, you can add in a lot of cost by overbuilding structures to be rigged and set into place,” Murphy said. “From our view, there’s economic decision to make at each point: Is this better done in a factory or in the field?”
Certain asset classes have more opportunity to build modular, particularly sectors with redundancies such as student housing, education buildings, hospitals, data centers and senior housing.
Some asset class do not lend themselves to prefabrication.
“Unlike hotels and senior living facilities, mixed-use and office space is not ideal for prefabricated solutions where tenants are likely to require reconfigurations from time to time,” DPR Regional Leadership Team's Peter Read said. "This is problematic with load-bearing interior walls."
But Hardiman has seen increased interest in healthcare, commercial retail and institutional buildings such as prisons and police stations.
In May, Marriott International announced plans to modularly construct 13% of its North American developments in 2017.
The rise in popularity has many developers determining how off-site construction can help their projects pencil.
Maximizing labor resources has been the primary driver to prefabrication construction, DeBruin said.
“I don’t think it inordinately helps speed to market. It might be more of a cost mitigator than cost saver. But anytime you can prefab in a controlled setting, there’s a propensity for enhanced quality control,” he said.
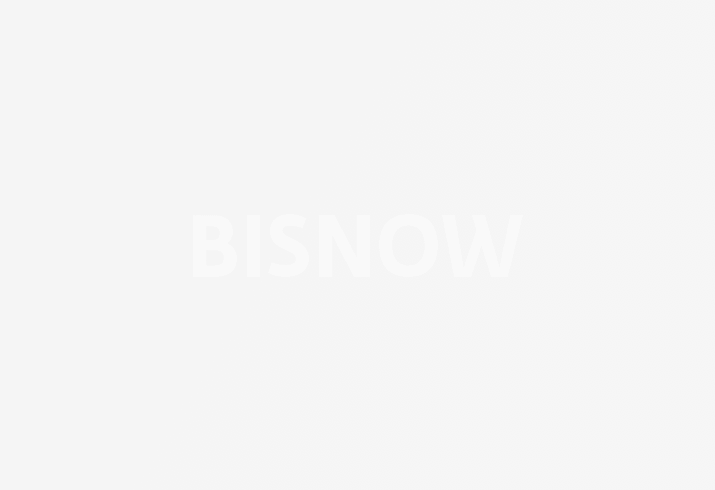
With skilled labor shortages impacting more of the U.S., off-site construction is a way to build projects in less affected areas, and to provide workers with safer working conditions in a prefab factory than out in the field.
“It isn’t as simple as that there are not enough skilled laborers,” DPR Project Executive Sean Ashcroft said. “It’s also about geographies of where skilled laborers are located versus where they are needed. If you have skilled labor in range, you can give them a better job in a safer workplace. Then if you have local fluctuation [in labor markets], you take out that element of shortage.”
Prefab offers more control and flexibility with labor.
“We often think about how many bodies we have in some area of a project,” Ashcroft said. “We have more controlled outcomes in a shop with less exposure to elevated working areas and things like that. It’s less strain on your workers.”
For Hardiman, the benefits of building off-site make its value a no-brainer for general contractors and developers.
“No one would question how we build cars today. It would be comical to have all the parts delivered to your driveway with a dozen workers to build it,” Hardiman said. “Yet we build our homes, schools and offices in this inefficient and wasteful manner every day.”
Hear more from Trammell Crow’s Jeff DeBruin at our Dallas Construction & Development event on Aug. 17 at the Westin Dallas Downtown.