Chip Manufacturers Are 'Getting Lapped' By Data Centers In Race To Develop AI Infrastructure
Big Tech’s artificial intelligence arms race is driving a development boom for data centers and semiconductor manufacturing in U.S. markets, but chipmakers are having a much harder time navigating the development headwinds facing both industries.
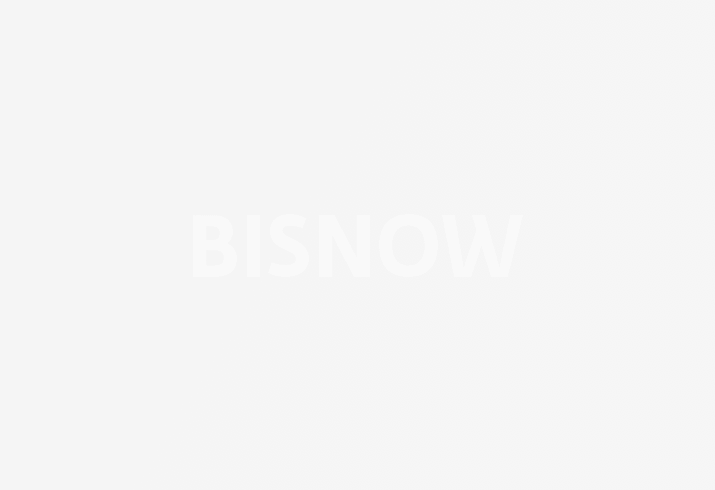
Despite skyrocketing demand for high-performance AI chips and billions of dollars in government subsidies to incentivize their fabrication in the U.S., semiconductor manufacturing firms like Taiwan Semiconductor Manufacturing Co. and Intel have been stymied by the same development challenges plaguing the data center industry, from power constraints to supply chain disruptions and labor shortages.
But chip manufacturers are way behind the data center industry in navigating these problems, according to industry executives speaking at Bisnow’s National Semiconductor Infrastructure and Real Estate summit, held Nov. 20 at the Scottsdale Marriott at McDowell Mountains.
Unlike data center builders, semiconductor manufacturers have largely failed to adjust their development and construction practices to address these headwinds and improve speed to market, the executives said. The result has been slower-than-expected growth and widespread delays on semiconductor projects beyond anything seen in the data center sector, with the gap expected to widen as data centers continue to beat out chip fabricators for materials, electricity and labor.
“The chip companies are definitely getting lapped by the data center companies when it comes to building out new facilities,” said Justin Jurek, director of Hitec Power Protection, a provider of power management systems for data centers and chip fabricators.
“We are seeing a lot of growth in the data center market, but while there’s lots of interest in building chip fabs, it’s not moving at the speeds we'd like to see,” he added. “There are a lot of chip projects that wanted to be online a lot sooner.”
Just as trillions of dollars in AI investment have fueled an unprecedented need for data centers, they have also driven an explosion of demand for the semiconductor chips powering the high-performance computing equipment inside them. It is a wave that has made chip designer Nvidia the world’s most valuable company and elevated firms like TSMC that fabricate the processors.
Global semiconductor manufacturing revenue is expected to double to more than a trillion dollars within the next six years, according to data from Gartner presented at Bisnow's summit. And while the U.S. accounts for only 8% of global chip fabrication today, there is a concerted effort from semiconductor firms and the U.S. government to rapidly expand the country’s chipmaking capacity.
As data center firms and chip manufacturers have grown together economically, they are also rising alongside each other physically.
Although the scale of data center build-out in the U.S. is much larger, the primary growth markets for semiconductor manufacturing, Texas and Arizona, are also two of the fastest-growing regions for data centers. Smaller data center hotbeds like the hyperscale hub of New Albany, Ohio, have also landed major chip fabrication projects. This reflects the similar site selection criteria for chip plants and data centers, but also the symbiotic relationship between two sectors that need each other for growth, said Gartner Senior Director Cori Masters.
“We're in a time of huge expansion, both for data centers and also for semiconductor manufacturing,” Masters said at the event. “The semiconductor revenue opportunity doubling in the next five to six years is a huge milestone that requires not just capital expansion but data center expansion.”
But as the two industries race to get new facilities to market as fast as possible, data center firms and chip manufacturers are facing development headwinds that have slowed the construction of new facilities and hampered their ability to keep pace with demand.
The data center boom has led to a spike in energy demand that has maxed out regional power grids across the U.S., an increasingly acute power shortage that has led to 10-year wait times for utilities to provide electricity to large consumers like data centers and chip plants. Supply chain woes also continue to create long lead times and uncertainty around the availability of critical equipment. Developers routinely face wait times of up to two years for items like the standby generators and electrical switchgear both industries need.
At the same time, a shortage of skilled construction labor needed for high-tech projects like data centers and chip fabricators is making it increasingly difficult to deliver projects on time. There just aren’t enough contractors to go around that have the skill set to build things like clean rooms or complex electrical systems required in these facilities.
The largest players in the data center industry, hyperscalers like Amazon Web Services and Microsoft and third-party developers, have dramatically transformed their development, construction planning and procurement practices for power and equipment over the past 24 months to limit the potential slowdowns caused by these lingering challenges.
But the same can’t be said for chip manufacturers, panelists said at Bisnow's event. The result has been significant delays in the construction of high-profile chip fabrication projects like TSMC’s planned facility near Phoenix and Intel’s proposed plant near Columbus, Ohio.
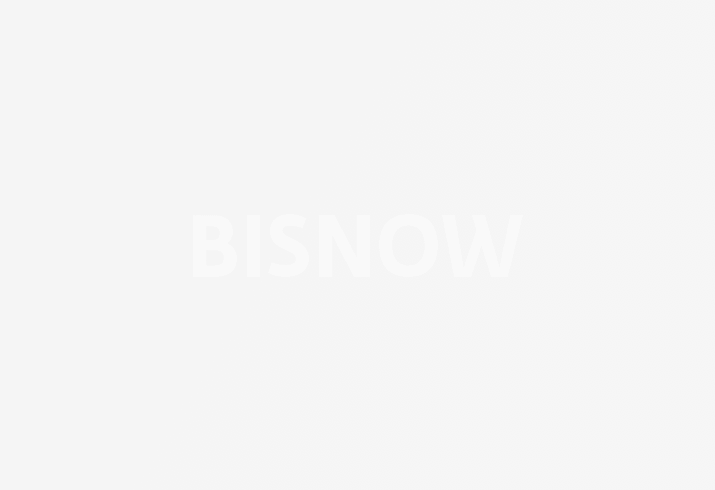
Hitec’s Jurek highlighted the data center industry’s willingness to get creative and make massive investments to get power for new facilities faster than utilities can provide it.
Data center firms are co-developing generation projects with energy firms, financing utility infrastructure projects, funding collaborations with utilities to find new ways to consume power, and investing in an array of technologies, from hydrogen fuel cells to modular nuclear reactors, that could enable them produce their own power on-site. He sees few comparable efforts from chipmakers.
Data centers have been similarly proactive when it comes to tackling supply chain disruptions. Operators now routinely stockpile generators, switchgear and other key equipment. They are also increasingly willing to deploy capital toward ordering oft-delayed items in bulk before there is even a specific project to put them in, all to ensure future projects will be more likely to get to market on time.
“We don't see that kind of aggressive behavior yet in the chip fab industry, but it might be needed,” Jurek said.
Despite the broad consensus that chip manufacturers need to be more proactive in their approach to supply chain constraints and other challenges slowing speed to market, Page Electrical Engineering Director Jonna Bournias also said this kind of advanced planning can be more difficult for chip plants compared to data centers.
Bournias said the rapid evolution of semiconductor design, with companies like Nvidia coming out with new chips every year, creates uncertainty around design and equipment needs.
“Plants have challenges with upfront planning because it's very hard to get your hands wrapped around what you're building when your product cycle is so short,” Bournias said. “They start these facilities before they even realize exactly what they're going to be building in them.”
Still, these additional challenges emphasize how important it is for semiconductor firms to adjust their construction practices to account for these shortages, Bournias said, and their failure to do so amounts to a major unforced error.
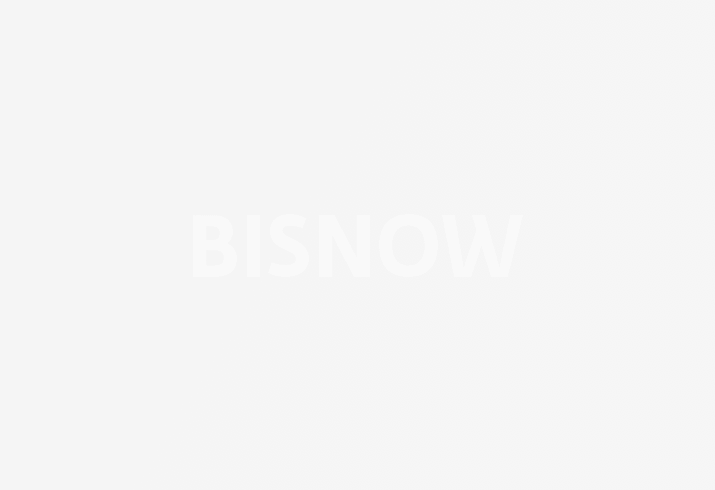
The data center industry, beyond just stockpiling key equipment and hiring contractors in advance, has also undergone a dramatic shift in construction planning. There has been a widespread realization of the importance of collaboration between all parties involved in a data center project from the second planning gets underway to avoid construction slowdowns due to equipment and labor scarcity.
Such multilateral early engagement with contractors, tenants, equipment manufacturers and other stakeholders allows developers to better anticipate design changes, identify areas where these changes are likely, and develop a construction plan that accounts for different scenarios. It also sets up skilled contractors to understand those scenarios and ensure their availability even as there are changes to the order of construction.
This was a major culture shift in an industry that has traditionally valued secrecy and where the impulse has been to keep proprietary design and equipment information as close to the vest as possible to maintain a competitive advantage.
But construction industry leaders involved in data center and semiconductor developments said this cultural change hasn't occurred in the semiconductor manufacturing space. Chip fabrication firms are still keeping designs, equipment specifications and other proprietary information close to the vest until the last minute, preventing early collaboration and planning with contractors and other stakeholders that could help anticipate problems in advance.
This represents a missed opportunity for chipmakers and is a root cause of why semiconductor plants are being developed far more slowly than data centers, Shockey Precast Vice President Marshall Sorenson said.
“It’s like the data center industry years ago — it’s shrouded in secrecy,” Sorenson said. “It’ll be hard to break through that cloak, but it has to happen.”
Because chip plants and data centers are frequently built near each other, the data center industry’s superiority in navigating power, equipment and labor shortages is exacerbating these problems for chip fabricators. Projects are competing for the same generators, contractors and grid connections. And more often than not, the data centers are winning, executives said.
“Projects can’t get contractors on board because a neighboring data center went up, it went up a lot faster, and it took all the trades,” Jurek said. “Then equipment vendors those facilities were designed around are no longer interested in the project because now they're just too busy.”