How Political Uncertainty Is Affecting Cities That Rely On The Cross-Border Economy
Every day, trucks, passenger cars and pedestrians cross the border between San Diego and Tijuana, bringing goods and workers across the border in both directions. That movement of goods and people contributes to the economic growth — a $230B binational economy — on both sides of the border in cities that have a shared culture and history.
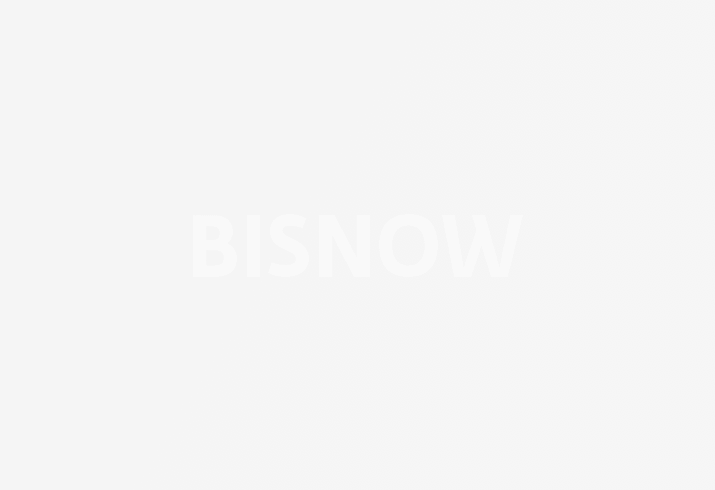
That porous border is a key strength for companies that operate in border cities, such as San Diego. But operating out of border towns has become an uncertain proposition in the current political climate. With President Donald Trump’s withdrawal from the proposed Trans-Pacific Partnership, heated debates over the future of the North American Free Trade Agreement, and the continued push for a border wall and 20% border tax, it is no longer clear whether operating with a foot in each country is a wise approach.
While some companies are sticking to their current plans and continue to see the benefits of trading with a nearby nation rather than one halfway around the world, others are looking at whether they need to change course.
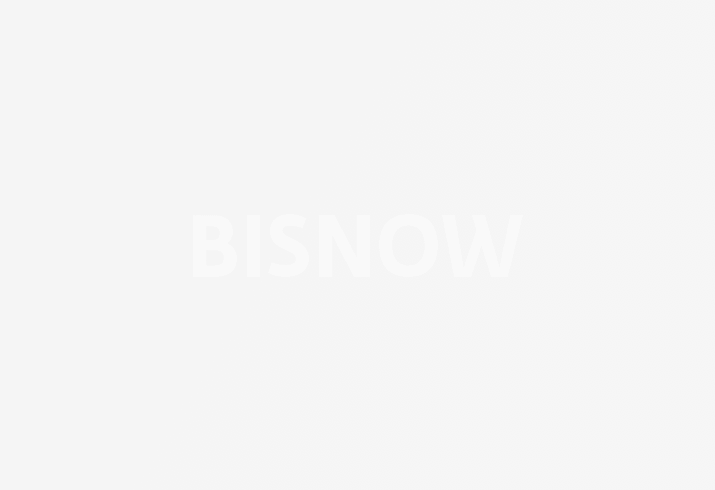
“Big uncertainty is the thing Trump has introduced to business,” San Diego World Trade Center executive director Nikia Clarke said. “Everyone wants clarity as to how these trade issues will shake out. This is not confined to San Diego or border cities.”
She said more than 40 million U.S. jobs are linked to international trade, which affects businesses across the U.S., Mexico and Canada.
“This is not a border city or blue state issue, it’s an American issue,” Clarke said.
Some on the ground in San Diego and Tijuana say many businesses remain committed to working on both sides of the border.
That is the case for binational companies with manufacturing operations in Tijuana, according to John Galaxidas, president and CEO of San Diego-based Synergy Real Estate Group. Galaxidas works with industrial clients on both sides of the border.
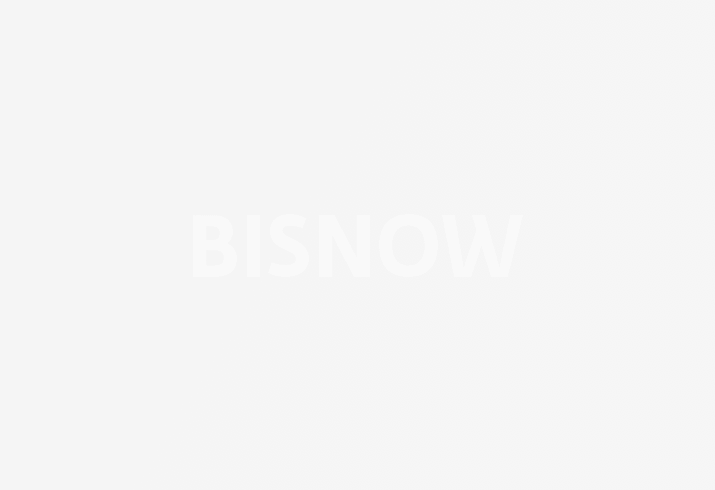
“If anything, most are doing nothing,” Galaxidas said. “Most are waiting to see what happens to NAFTA.”
A few clients that had planned to set up shop in Mexico are staying in the U.S., he said, and some U.S. companies are considering moving their operations back to the States, though it makes little sense when costs are compared.
In part, the long timeline for establishing and building or leasing facilities means that many companies cannot quickly respond to a shift in political will, while those not yet locked in can weigh their options and determine if it still makes sense.
“Some companies that had been looking at nearshoring in Baja have already pulled the trigger,” said Christian Tagliapiata, regional operations manager at IVEMSA, a corporate shelter firm that assists foreign companies in establishing operations in Mexico. “But for others, it still makes sense to do business in Mexico, and there’s no deterring companies with projects already in the pipeline.”
Many products move across the border several times during their manufacture. That means jobs on both sides of the border. If they were not in Mexico, these manufacturing jobs would likely be in India or China, Clarke said.
“For a long time, it was so cheap to manufacture products in China, but not so anymore,” Clarke said. “Costs rose in China and with shipping adding pressure, companies are reshoring or nearshoring closer to U.S. markets.”
There is a benefit to companies — and the local economies — of only shipping a few miles across the border rather than across an ocean. Clarke said the content of products co-produced across the U.S.-Mexico border are 40% American-made, while Chinese products may have just 1% to 2% of American content.
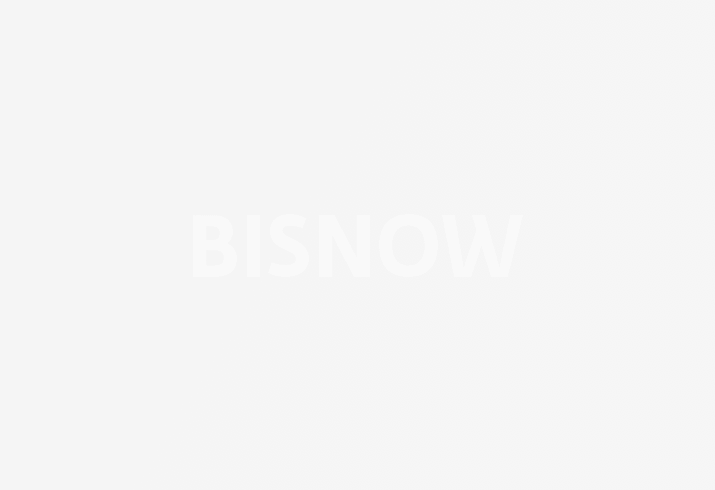
Prior to the U.S. elections, manufacturing was a main reason companies decided to locate in or leave Mexico, said Fernando Arjona, owner of Tijuana commercial brokerage firm Omega Capital Mexico. Sony and Sharp no longer have plants in Tijuana, he said, but their products are still made there by manufacturing contractors.
Arjona just concluded three deals with foreign third-party logistics operators for between 30K SF and 100K SF.
Even with a stiff import tax, it likely would remain more cost-effective for many companies to manufacture in Mexico than California, Arjona said. The average wage in Tijuana is $4.50/hour, compared to $11 to $15/hour on the other side of the border.
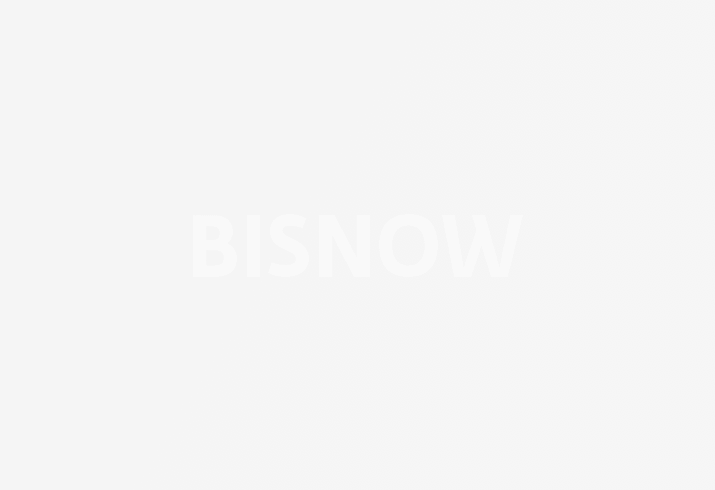
For workers, there is anxiety about what may happen to their jobs at firms operating in Tijuana.
Two workers spoke to Bisnow about job security at Medtronic’s medical device manufacturing facility in Industrial City, a large industrial district on the Otay border, one of the places where goods and workers cross the border daily.
For the first time in his life, Alberto, who has a wife and three children, has a job with a reliable income. He formerly worked as a deliveryman, but said that type of work is erratic. He began working for Medtronic eight years ago as a mover of products and materials to and from the plant floor.
“I have advanced with wage increases,” Alberto said through a translator.
His salary, along with his wife’s income (she also works for Medtronic) allowed them to buy their own apartment.
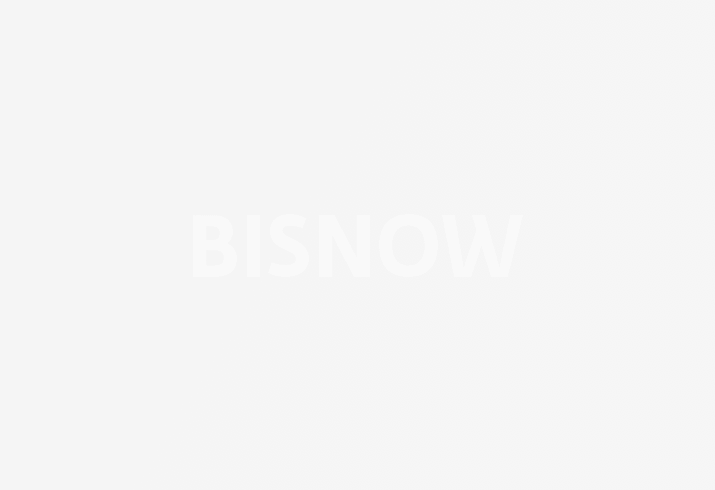
Victor has worked at Medtronic for seven months. Until Mexico began charging a 16% duty on merchandise purchased in the U.S., he said he made more money buying tools wholesale in the U.S. and selling them retail in Tijuana. Victor said his job as an assembler does not pay much, but does provide a steady paycheck.
Trade is crucial to economic prosperity in the San Diego-Tijuana mega-region. Tijuana has 15 industrial districts with more than 500 manufacturers for electronics, medical, automotive and aerospace products. It also has a growing innovation economy of its own.
Galaxidas said it is more convenient for company executives to visit plants in Tijuana than Asia, and NAFTA allows goods produced in Mexico to flow across the U.S. border quickly and cost-effectively. A container shipped from China takes up to three weeks for delivery to U.S. markets and costs nearly $8K to ship compared to about $3K from Tijuana. Tijuana’s attractiveness is enhanced by its low corporate tax, growing trucking industry, and combination of industrial real estate capacity, developable land and low-cost, high-skilled labor force.
“If the U.S. slaps on a tariff, the rippling effect would almost certainly be passed on to the U.S. consumer," Clarke said.
Arjona said there is a lot of discussion in Tijuana’s manufacturing community around what to do if Trump follows through on imposing a border tax.
“A 20% tax would hurt us,” he said. “We can get really creative or do the same thing.”
Arjona said it probably will not affect companies already here, but could impact new companies entering the Tijuana market.