Lean Construction Can Lift Lagging Sector
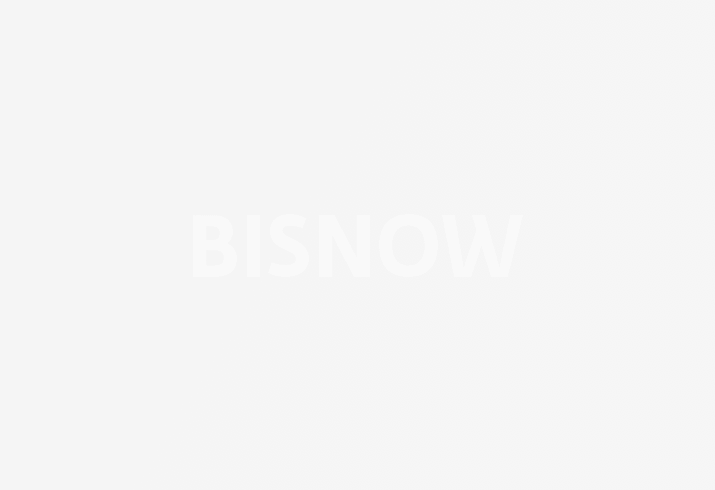
Less than 30% of construction projects are completed on time and on budget. In an effort to improve, some progressive construction companies are adopting lean construction.
Lean processes emphasize efficiency, maximizing value and minimizing waste. This is imperative for construction, a sector in which the labor hour’s effectiveness has been stagnant for over half a century. This means that the output per worker has remained unchanged as other industries have exponentially increased employee productivity, many with a combination of technology and more strategic allocation of human capital.
This resistance to change has contributed to construction's labor and talent shortages.
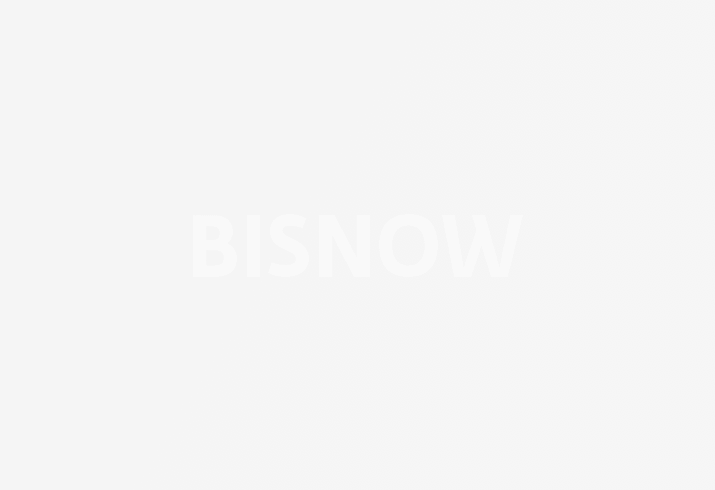
Lean construction has several tenets: find and eliminate waste, standardize practices and reduce variation, focus on process and flow, respect the contribution of each team member, continually improve processes and examine and optimize the whole.
“Ultimately, the savings provided by implementing lean construction principles serves the end user in a big way,” Talisen Construction CEO Joseph Rigazio said. “With careful planning and the elimination of wasteful means and methods, we can reduce costs, expedite schedules, increase safety measures and, most importantly, delight our clients.”
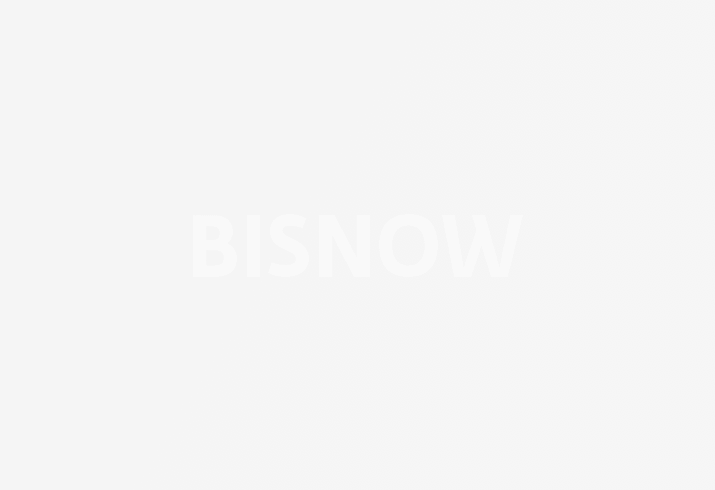
Healthcare is booming, and its growth may lead to more innovative construction solutions. According to NAIOP, healthcare construction in the U.S. totaled $41.4B, or 9% of nonresidential spending last year.
In 2015, Americans spent $3.2 trillion on healthcare, approximately one-sixth of the U.S. gross domestic product. This represents a 6% increase from 2014, which is the largest change since 2007. An aging population and per-capita expenditures over $10K encourage healthcare companies to expand to meet anticipated demand.
For medical office buildings, 2016 vacancy rates were the lowest on record, while net absorption and rents reached post-recession highs. Healthcare companies are also aggressively buying up underutilized or defunct retail properties to convert to clinics and medical office buildings. According to Rigazio, lean methodologies are particularly effective for complex healthcare projects, renovation and new construction alike. They can complement the implementation of new techniques and technologies.
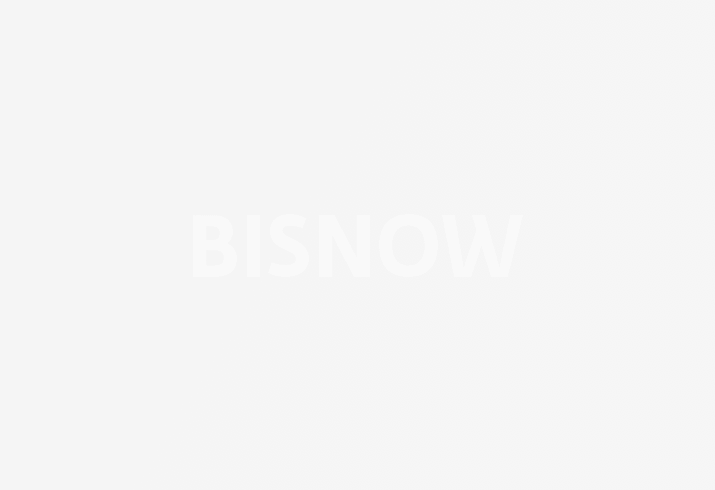
"Modular prefabrication of certain project specifications can offer a considerable time and cost savings," Rigazio said. "Building complex and time-sensitive items off-site in a controlled environment allows for higher quality and faster implementation in certain situation. This innovation saved thousands of dollars in man-hours and materials and actually is a safety benefit due to less fatigue."
According to Rigazio, when adapting spaces for healthcare use, Talisen’s clients are cautious and risk-averse. They may require multiple plans and multiple versions to ensure every need is provided for.
Many contractors will quickly and instinctively assess the potential upside and downside of a plan, and build within the zoning and regulatory bounds. They are accustomed to employing a tested approach and addressing any problems as they materialize.
But due to the specificity of healthcare buildings’ requirements, even the smallest oversight or neglected issue can result in significant construction delays and expensive, suboptimal retrofits down the road.
“There are things in our preamble, before we even start to put together a proposal, that we spend time mapping out,” Rigazio said. "Working innovative methods like these into our projects helps in driving collaboration across teams and delivering the project on time and on budget."
To learn more about this Bisnow content sponsor, click here.