Should We Keep Building? As Cases Rose, Healthcare Construction Faced Tough Questions
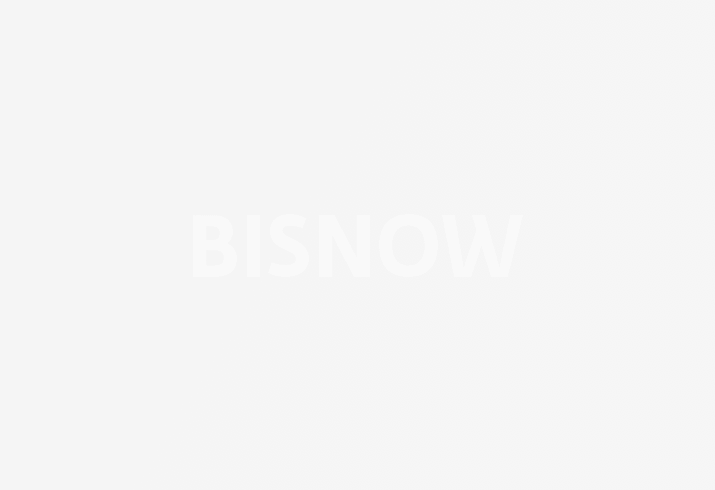
Back in March, construction sites across the nation shut down to combat the spread of the coronavirus. Healthcare facilities, however, were by and large deemed essential construction, meaning hospitals, outpatient centers and medical offices could keep building and renovating.
But the decision to continue building was not simple. As the pandemic set in, the nation’s largest health systems and the contractors that work with them faced not just the challenge of keeping construction employees, healthcare workers and patients safe, but also tough questions about how to allocate their newly limited labor and time on the job site.
“Very quickly, we had to communicate with the healthcare systems we work with to determine what work needed to continue, and what work was considered nonessential, to be put on the back burner,” said Christopher Morris, national healthcare director at Swinerton, a top 20 national contractor. “We had to balance what made financial and logistical sense with what would actually let these systems provide the best care and safety for their patients.”
While Morris said the majority of Swinerton’s healthcare work continued as planned, he has seen some major changes at projects whose scope eclipsed hundreds of millions of dollars. As case numbers rose, construction firms had to take on the role of advising partners for healthcare systems, helping them build a cost-effective plan to continue their projects.
Pumping The Brakes
Early in the pandemic, some healthcare systems decided that they needed to slow the process of construction. Those with buildings in the very early phases of construction especially wanted to minimize the risk posed to their own patients. Some decided that renovations or new construction could wait, often freeing up space that had been shut down in preparation for builders.
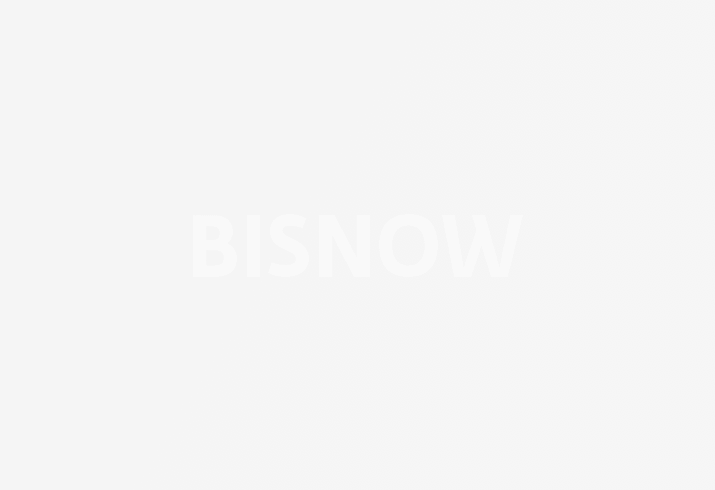
Others decided that they would pause construction in one area to speed up work in another area, or to allocate money for another purpose. But putting a construction project on ice is not always a recipe for long-term savings, Morris said. Delaying a project could mean breaking contracts for materials and labor that could be costly to reschedule.
“We may have secured our fabrication timelines and have materials ready for procurement or scheduled for delivery,” Morris said. “If we lose our spot, it could be months or longer before that material is available again.”
As soon as the shutdowns began, some of Swinerton’s healthcare clients asked the construction teams to provide recommendations for the safest and most cost-effective way to shut down the project. When should work stop, what deliveries are non-negotiable, and when does it seem like the project could start up again?
While the process of negotiating new construction plans was never easy, Morris said, it reinforced his belief in the partnership between his firm and its clients.
“It was always a very frank discussion,” he said. “It was, ‘Let’s talk about what is practical, what meets our objectives and the needs of our patients.’ And it’s our job to be an advising partner to these massive health systems to make sure we can always providing them the best service.”
Ramping Up
Some healthcare systems decided to accelerate construction, working to complete pieces of a project or an entire building ahead of schedule. In some cases, Morris said, healthcare systems pushed forward to build “surge” facilities that would be able to accommodate an influx of patients with COVID-19. Others pushed to complete outpatient facilities that could provide funding to support the rest of the hospital’s operations.
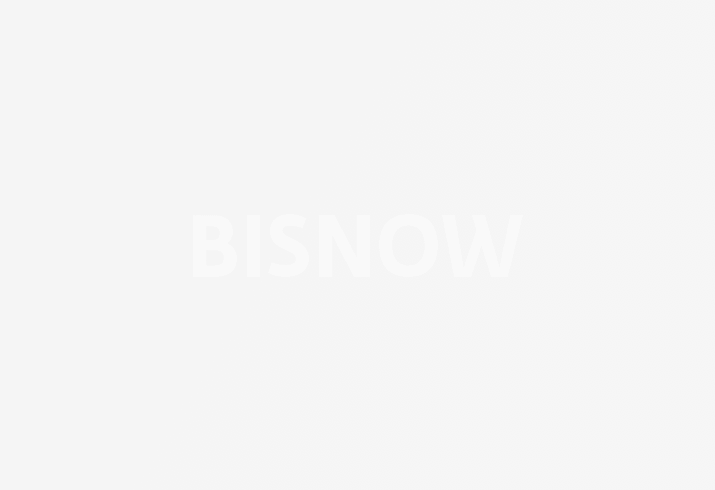
For its part, Swinerton jumped into action, reconfiguring timelines to speed up construction and preparing health and sanitation protocols to keep its healthcare job sites safe.
“The Bay Area construction shutdown went into effect on March 16,” Morris said. “We released our national procedures and COVID plan just two days later.”
On some of the sprawling hospital campuses where the firm worked, Swinerton implemented shift work, bringing in different crews at various points in the day to minimize contact between construction employees. The firm’s tech teams rolled out QR-enabled mobile health questionnaires that workers had to complete along with a temperature check before being allowed on-site. Wristbands and stickers identified workers that had access had met the requirements for access to the job site or the healthcare facility, reducing overlap between workers.
Infection control measures, which have always been a requirement of healthcare construction, became all the more important, Morris said. Swinerton bulked up its on-site infection control staff and isolated more areas of the job sites to ensure that staff came into as little contact with patients as possible. The crews also set up negative air pressure rooms, which keep pathogens from spreading.
“Now I’m on calls with the leaders of Swinerton’s other practice areas, such as our aviation and science and technology teams,” Morris said. “They’re looking to implement some of the same health construction procedures that we’ve always had.”
This feature was produced in collaboration between the Bisnow Branded Content Studio and Swinerton. Bisnow news staff was not involved in the production of this content.