U.S. Reshoring Rush Running Up Against Labor Market Malaise
The push to reshore and otherwise grow U.S. manufacturing space is in full swing, as private companies look to avoid supply chain disruptions and public policy supports its expansion as a matter of national and economic security.
But forces are pushing back, namely a labor shortage impacting both the ability to build the new manufacturing spaces the reshoring effort demands and to staff them once they’re finished. These challenges can serve as a deciding factor for companies choosing when and where to build.
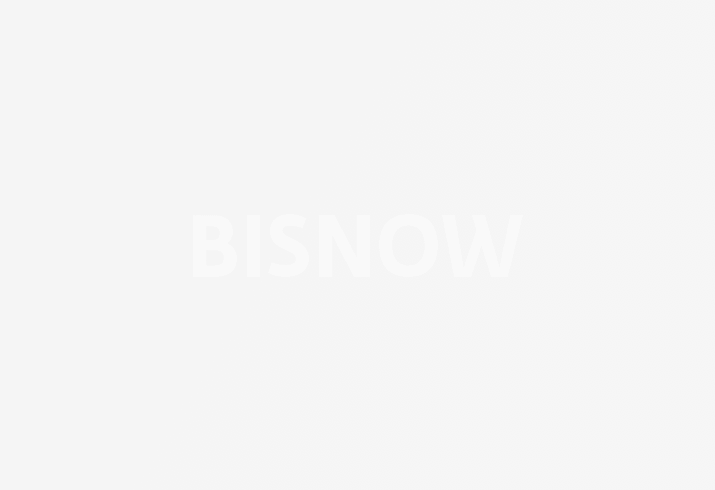
“The actual talent that the firms need to operate these new facilities is certainly something to consider when we're talking about kind of site selection challenges, especially in the smaller locations, the micropolitan markets where some of these large facilities are going,” Newmark Managing Director of Industrial Research Lisa DeNight said.
The pandemic exposed weaknesses in the international supply chain, with U.S. companies clamoring for goods needed to distribute everything from toilet paper to semiconductors to vehicles. Combined with a push from the Biden administration to bring more manufacturing back to U.S. shores, development of new manufacturing facilities is climbing.
Private construction spending on manufacturing facilities has topped $210B, according to a February report from the National Association of Manufacturers, the result of reshoring, among other demand drivers.
But at the same time, over 65% of manufacturers surveyed by Deloitte said the challenge of attracting and retaining talent is now their top concern.
Labor-related delays have already occurred in the sector. Last year, Taiwan Semiconductor Manufacturing Co. extended the production schedule for chip factories in Arizona, citing a lack of specialized workers.
“We are encountering certain challenges as there is an insufficient amount of skilled workers with those specialized expertise required for equipment installation in a semiconductor-grade facility,” Taiwan Semicondcutor CEO C.C. Wei said during a company earnings call not long after the announced delay.
An estimated 365,000 jobs connected to reshoring and federal direct investment were announced in 2023, according to the Reshoring Initiative, on top of 343,000 in 2022, which was nearly double the number just five years earlier.
“Manufacturing often requires significant headcounts — sometimes thousands of people — which inherently brings challenges from a staffing perspective,” Claudio Knizek, global advanced manufacturing and mobility leader for EY-Parthenon, told Forbes.
The labor shortages are likely to impact smaller markets more than larger ones, according to Newmark’s North American advanced manufacturing report. Such places as Brownsville, Tennessee; Elizabethtown-Fort Knox, Kentucky; and Sherman-Denison, Texas are all slated for new facilities with thousands of job openings in the coming years, Newmark found.
Individually, each of these five markets’ projected employment gains will surpass all but one of the top mid-sized markets, indicating new advanced manufacturing facilities have the potential to disproportionately impact smaller economies, the report explains. At the same time, the advanced manufacturing labor pool in such places as Brownsville and Sherman-Denison is relatively limited.
The Sherman-Denison metro area is in Grayson County, just north of Dallas. Locally based calculator maker Texas Instruments and Taiwanese-owned Globitech both have advanced manufacturing projects underway in the area, despite a labor shortage dating back years.
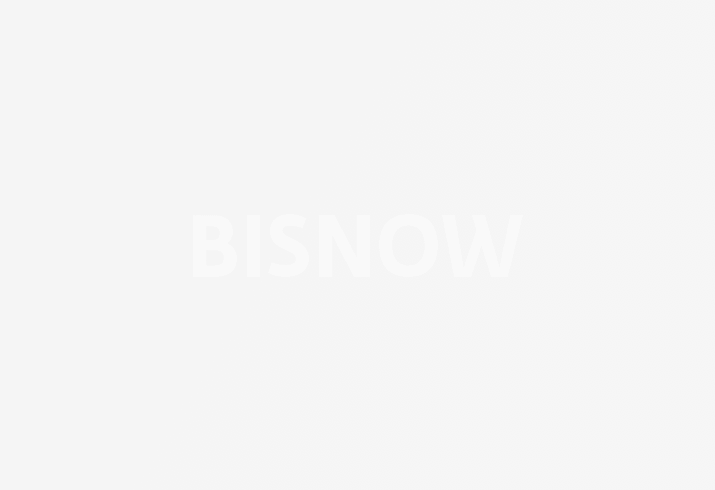
Counteracting the shortages are incentive dollars, not just from the federal government but from states and municipalities as well. For its manufacturing campus, Texas Instruments expects to save $2.36B in property taxes over 35 years, the Dallas Morning News reported. However, these incentives are usually tied, at least in part, to successful job creation, placing more pressure on the ability to find workers.
Labor has long been a factor in site selection among manufacturers, but now the focus is especially keen, Newmark Head of Northeast Research & National Life Science Research Liz Berthelette said.
“We've found that a plurality of the projects that we track not only have located where there are higher concentrations of advanced manufacturing labor but where there are higher than average concentrations of a preexisting manufacturing base compared to the total industrial inventory,” Berthelette said. “That's common sense, in a way.”
The shortage of U.S. construction workers is widespread as well and stands to impact the pace of manufacturing development.
“Some of these megaprojects need tens of thousands of construction workers,” Berthelette said. “That could also be a potential deterrent.”
The construction industry will need to attract an estimated 501,000 additional workers on top of normal this year to meet the demand for labor, according to Associated Builders and Contractors. In 2025, the industry will need to bring in nearly 454,000 new workers on top of normal hiring.
In the face of labor shortages, there will be some workarounds for manufacturers — such as the traditional one of automation augmented with emerging AI tech, according to ElmTree Funds Managing Director MaCauley Studdard, whose company is a net-lease investor with a special interest in reshored manufacturing assets.
“Labor within facilities is definitely still a constraint that companies are working through,” Studdard said. “What we've seen, by large corporations that have the balance sheet to fund automation, is building modern warehousing and manufacturing facilities that house robotics and conveyor systems and everything that they need to operate most efficiently.”
Public-private partnerships to train new workers are also in place as well, DeNight said.
At the federal level, the Biden administration kicked off an initiative last year to train advanced manufacturing workers via a variety of partnerships with local officials, employers, unions, community colleges and high schools. The administration named five “workforce hubs” where the effort will focus on specific industries, such as Phoenix for semiconductors, optical cables and battery making. Other hubs will include Augusta, Georgia; Baltimore; Columbus, Ohio and Pittsburgh.
Other initiatives are locally created, with a local focus.
In Washington state, for example, the nonprofit AJAC partners with employers to create advanced manufacturing apprenticeships. In Massachusetts, the Center for Advanced Manufacturing provides grants for the creation of programs that prepare high school students for manufacturing careers. Colleges are getting in on the action as well, such as the Workforce Development Center at Cincinnati State which focuses on advanced manufacturing.
“Most states are operating on budget surpluses and there have been many initiatives and investments on a state by state or local level to bolster manufacturing workforces,” DeNight said. “It's somewhat of a decentralized approach, but there are many players that are racing to make this happen.”