Warehouses Increasingly Turn To Automation, But That Creates New Problems
The companies that occupy industrial logistics properties are having a hard time finding workers, pushing them toward automation technology to move goods through their warehouses.
But bringing in robots isn’t a simple solution. It doesn’t work for some facilities that weren’t built with automation in mind, and the technology requires warehouses to use much more power, a resource that has become scarce in many regions as the booming data center sector overwhelms utilities.
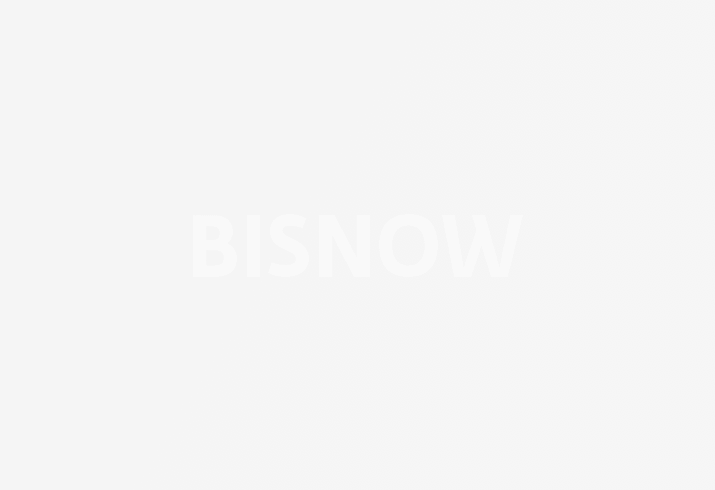
“It’s top of mind for all the companies we work with is, what are they doing next? Because they can't find the labor anymore,” Daniel English, managing partner at industrial and data center owner Legacy Investing, said last month at Bisnow’s Mid-Atlantic Industrial Summit in Baltimore.
A December survey of 1,000 supply chain and logistics executives found that 76% were facing notable labor shortages, with 37% of those describing their shortages as “high” or “extreme,” according to logistics software firm Descartes Systems Group. The American Staffing Association projected that job openings in the warehouse and transportation sector will hit 1.7 million this year and rise to 2.1 million by 2030.
English said he worked with a company, which he declined to name, that over the last four years has never been able to fill more than 70% of its warehouse jobs.
“They said, ‘We have to automate. We cannot do this anymore,’” he said.
Automation can also help industrial tenants reduce the amount of space they lease. Some are employing this strategy in the face of rent increases that are "causing a strain on those companies' finances," Prologis Vice President Karen Cherry said at the event.
“They're looking at, ‘How can I incorporate these new technologies and innovations and automate my facility when I can't afford to pay a doubled rent?’” she said. “So they're looking at consolidating and doing that upgrade to automation."
Urban Outfitters has leaned into automation for its rental clothing brand Nuuly, an effort that has helped it cut costs and turn a profit, The Wall Street Journal reported in April. The company opened a $60M automated warehouse in Missouri earlier this year.
An estimated 26% of warehouses are expected to be automated by 2030, up from 18% at the end of 2021, according to Interact Analytics.
“This is actually more common than I think the market is aware of,” English said of automated warehouses.
But not all properties are a fit for the advanced technology.
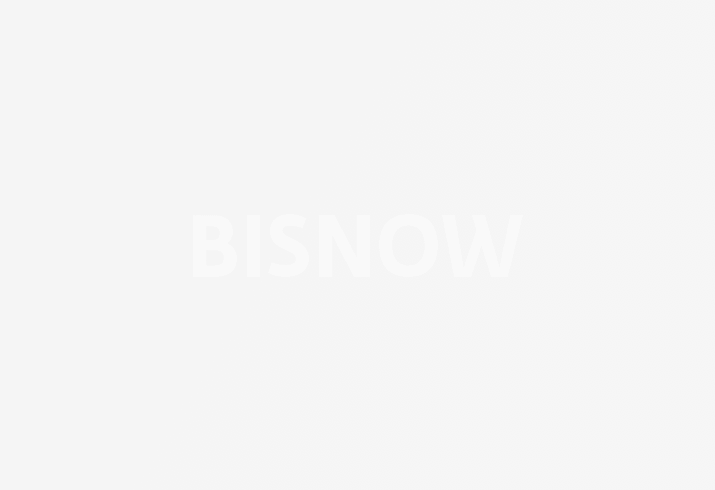
A host of industrial projects that broke ground on spec during the pandemic-era boom are still looking for tenants as demand has cooled. But English said “a lot of” these spec projects don't work for automation because they weren't purpose-built, a point that ARCO Design/Build Vice President Drew Enstice echoed.
“A lot of times when someone's building a spec building, they're not spending the money to have all the extra infrastructure and equipment because they're not sure they're going to need it until one of those tenants comes in," Enstice said at the event.
Peterson Cos. President of Development Taylor Chess said his firm bought a warehouse in the Baltimore area that was fully automated, but it has run into issues with the humidity.
“In this area, there's some sort of weather pattern that creates moisture, and the concrete will sweat,” he said. “The robots can't run on sweat, so we've got to condition the space so that it doesn't have this humidity, moisture content. These are things that you never would have thought about in a warehouse before.”
Additionally, automated warehouses consume far more power than traditional ones filled with human workers, several industrial executives said.
“The real estate mantra used to be ‘location, location, location.’ Well, now it's ‘location, location, power,’ and not necessarily in that order,” Prologis' Cherry said.
“Power is really important, both on existing buildings and on new developments,” she added. “For our customers with the additional automation technology that they're deploying within their spaces, it's on the owners to really assist them in providing the power that they need.”
Providing that power has become much more difficult over the last year.
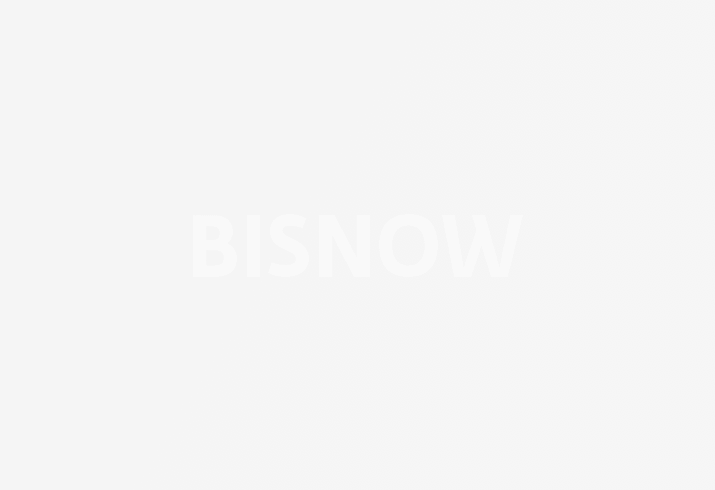
Big Tech's artificial intelligence arms race has led to a data center construction boom across the country that has put an enormous strain on power utilities. In major markets like Northern Virginia, the Bay Area and Texas, utilities are telling data center developers it could take years to secure the power they need to fuel their facilities.
Data centers are projected to consume 6.6% of all U.S. electricity by 2028, up from 2.3% last year. This has created a pitched battle for any other asset classes — such as automated warehouses — that need large amounts of power.
“There is competition of power,” said Powers Brown Architecture principal Reinaldo Venancio, who said he has worked on automated warehouse projects that require more power. “So we're competing all the time with data center sites.”
Legacy Investing's English said he has worked with a large tenant, which he declined to name, that struggled to secure power for its automated warehouse.
“They couldn't get power for a year to run their automation system, and they were quite frustrated,” he said. “There's sort of this data center-industrial overlap, which is really interesting because there's not enough infrastructure to get the land to have enough power.”