As Supply Chain Disruptions Return, The 2021 Logistics Playbook Won't Work This Time
Weeks of labor unrest at the Ports of Los Angeles and Long Beach might have culminated in an eleventh-hour deal to avoid a strike.
But the delays they threatened gave a brief flashback to the logjam that prompted a redistribution of port traffic elsewhere in the country. Meanwhile, the very same Gulf of Mexico and East Coast ports that benefited from supply chain adjustments are now imperiled by the drought at the Panama Canal that has curtailed barge traffic dramatically in the past three weeks.
After a year of relative respite, supply chain disruptions are on the rise again. And this time around, logistics users don’t have the same capacity to throw money at the problem or the consumer demand to justify it.
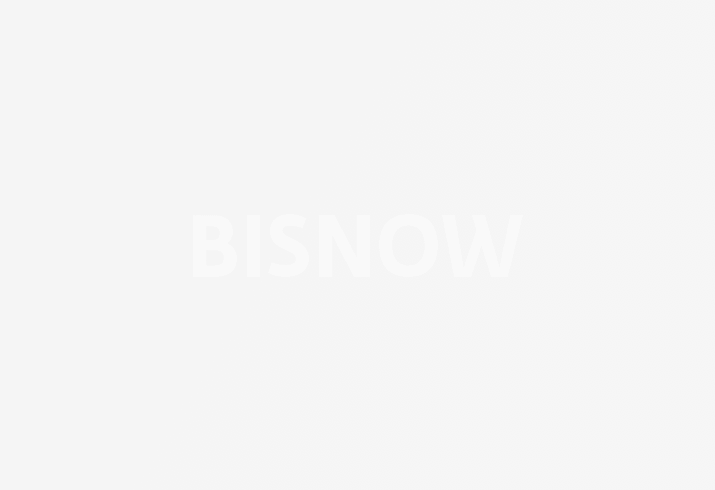
The cascading events that sent import costs and lead times skyrocketing in 2020 and 2021 prompted retailers and other warehouse users to swell their inventories — only for customer demand to shift and for the cost of carrying excess inventory to rise sharply, University of Iowa professor of business analytics Jennifer Blackhurst told Bisnow.
“Companies putting a lot of money in inventory caused huge disasters toward the end of Covid,” she said. “We’re not out of options, but it’s not as simple anymore as swinging between running really lean and having a lot of inventory.”
With inventory strategy shown to be insufficient to overcome supply chain uncertainty, the remaining responses are to build a new supply chain and/or get smarter about the one that exists right now.
The rise in manufacturing is a sure sign of the new supply chain being built. Automakers are racing to build battery factories across the Southeast for electric vehicles, while clean energy and life sciences drive new factory starts across a diverse array of markets.
This new wave of U.S. factories has been assisted by government incentives, much like the CHIPS Act has spurred billions in construction proposals for semiconductor plants.
But that much industry takes years — and lots of work — to bring online, and the supply chain is likely to remain unpredictable through then.
“You cannot make the assumption that you can turn on a new supply chain, sit back and wait, and watch it happen,” Blackhurst said.
Supply chain unpredictability has risen over the past few months after shipping containers dropped to pre-pandemic levels from the highs of 2021, online container transaction platform Container XChange found in its June research report.
The traditional bumps associated with holiday season preparation have not manifested so far this year, as container rates declined steeply in the past week, according to the June 22 update of the Drewry World Container Index.
“As we go into what is traditionally peak season, we aren’t really seeing a demand uptick,” Container XChange co-founder and CEO Christian Roeloffs said. “Part of that is due to the relatively high inventory-to-sales ratio, part is due to slower consumer demand metrics, and it may be that retailers that do expect a demand uptick already ordered earlier, which essentially flattened out what would have otherwise been a slump in those months.”
Even as virus containment lockdowns recede into memory, few companies had any illusions that the supply chain would revert to functioning as it did in years past, Blackhurst and Roeloffs said. Natural disasters become more frequent and damaging every year, transportation bottlenecks arise without warning and labor is a constant issue, whether through a lack of truck drivers or unrest like that seen at the Ports of Los Angeles and Long Beach.
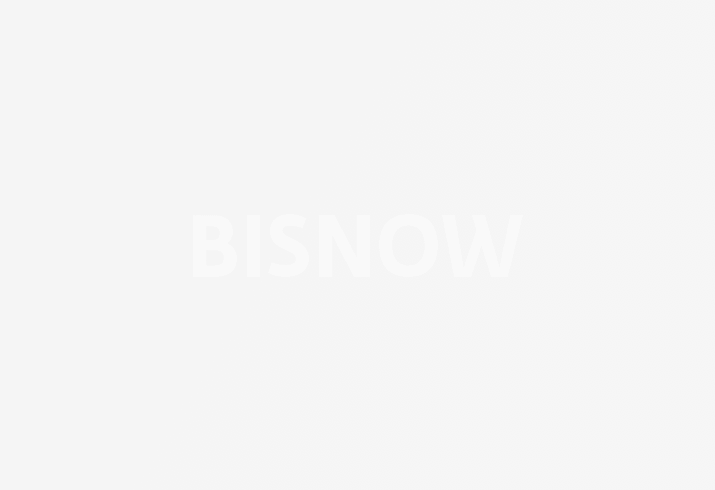
“Companies and supply chain professionals in general realized that our supply chains and container logistics networks are not as resilient as they once seemed,” Roeloffs said. “They’re not as reliable, timely or immune to external shocks as they seemed.”
After bulking up on inventory — the common first response to supply chain snarls — blew up in some companies’ faces, many are now seeking to avoid a repeat of history by leaning hard into technology and data science, Blackhurst said. That allows for closer monitoring of every link of the supply chain and better analysis of the data produced by such monitoring.
But much as the largest retailers like Amazon, Walmart and Target elbowed smaller companies out of the best real estate in the recent leasing boom, they are also among those with the capacity, financial or otherwise, to rapidly scale up the information technology required to make supply chains more intelligent. That has given rise to logistics as a service, which has seen such giants as Amazon, Prologis and Maersk make inroads in the past year.
“A smaller company doesn’t have the buying power or resources to own its own transportation routes,” Blackhurst said. “So [more are] buying it as a service, now that we know supply chain is such a competitive advantage — maybe we knew that before, but it’s really clear now. So you’re seeing more tech companies providing services, and they’re really meaningful right now. And more logistics companies are offering their services in this area as well.”
Amazon and Prologis are both hoping to use the dominant market positions they achieved in the past few years to lure users to their logistics networks, while American Eagle subsidiary Quiet Logistics partnered with JLL this past winter to sublease underused real estate as an intermediary for small retailers without the pocketbooks for their own warehouse leases.
The demand for the new offerings is there, said CBRE Senior Vice President Fred Ragsdale, who focuses on industrial tenant representation from his base in the Dallas-Fort Worth area.
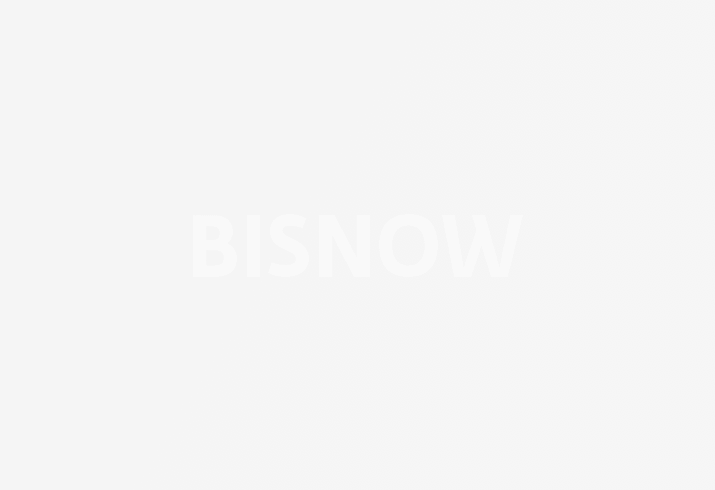
“Without a doubt, across the country, the most active user or tenant group is the 3PLs,” Ragsdale said. “They’re the groups that are taking down space. Some of the larger 3PLs have started to have internal hiring freezes and slow things down, because their business is determined by what their partners are doing. They are the most active and trying to be solutions for organizations that are new to the market, but there’s a little bit slower growth from existing clientele.”
Yet the smartest, most nimble supply chain management still can’t overcome issues inherent to the long journey across the ocean. Importers who shifted their shipping lines away from the West Coast took a hit this month when a worsening drought in Panama caused the Panama Canal Authority to impose limits on the number of barges that can use the crucial crossing between the Pacific Ocean and the Gulf of Mexico.
The public and private sectors in the U.S. launched massive initiatives to revive domestic manufacturing, or at least favor imports from countries closer and with more stable diplomatic relationships to the U.S. than China. But reshoring efforts have only begun to transition from the planning phase to the construction phase in the past year, meaning the supply chain impact is still two years off at least, Blackhurst said.
“Those big manufacturing projects take time, because there’s negotiations around incentives, and then they’re all three- to five-year endeavors,” Ragsdale said. “So we’re seeing a lot of projects start to wash up on the shore now because it takes time to work out those proposals.”
The multiyear wait for domestic manufacturing to come online is perhaps the largest-scale version of the shift in how logistics users are prioritizing their supply chains: valuing predictability and consistency over speed.
“We know as consumers that that’s what we prefer,” Blackhurst said. “It’s like waiting on the cable guy to show up; just tell me when, even if it’s inconvenient, but don’t just not show up. To see potential problems on the horizon and develop backup plans to backup plans — that’s what we’ll see a whole lot of.”