Tariff Threat May Fuel Construction Materials Stockpiling And Spur Industrial Outdoor Storage Use
In anticipation of promised tariffs under the coming Donald Trump administration, some in the construction industry are stockpiling materials, creating fresh demand for industrial outdoor storage, or IOS.
After a growth spike when the pandemic caused massive demand for storage space, IOS has faded somewhat from view, but it could enjoy refreshed interest as a quick solution for companies trying to get ahead of what could be pricey taxes on necessities for new commercial development.
“Of course, this is great for industrial storage, because if you're worried about 25% tariffs on Mexican goods or 60% tariffs on Chinese goods, you better buy your construction inputs, whether materials or equipment, now and store it,” Associated Builders and Contractors Chief Economist Anirban Basu said. “Otherwise, if you wait, you're going to pay a lot more.”
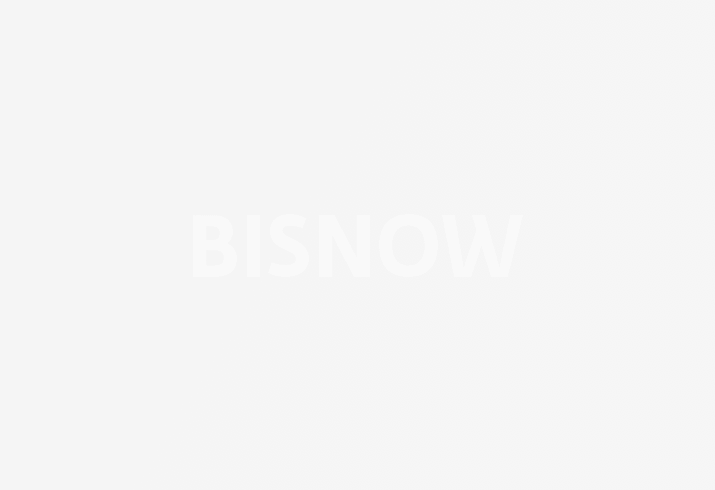
On Nov. 25, Trump said he wants to apply 25% tariffs on goods from Canada and Mexico, two of the U.S.’ largest trading partners for lumber and construction equipment. He had earlier pledged at least 60% tariffs on China and at least 10% tariffs on goods from all nations.
“It’s hard to see in the macroeconomic data, but I've certainly talked to contractors who have told me that they're stockpiling equipment ahead of time because they're worried about the tariff,” Basu said. “There’s no question there's been some response.”
Any move to store goods suddenly may benefit warehouses as well as IOS sites.
“I anticipate many building materials suppliers will stockpile materials to the extent possible,” Matt Hunsucker, founder of industrial outdoor storage newsletter IOS List, told Bisnow in an email. “If suppliers choose to stockpile materials, they will look to increase inventory throughout their supply chain. The easiest and cheapest place to store materials is in outside yards.”
China is a major supplier of steel, flooring finishes, electrical components and HVAC equipment. Mexico supplies concrete, cement, roofing materials, steel, glass and windows. Canada is a major supplier of lumber, aggregates, steel, aluminum and asphalt.
Prologis Managing Director of Global Strategy Chris Caton told the BBC he had already seen more activity “on the margin” as businesses across the economy sought storage space in response to potential tariffs. And while many supply chain specialists at multinational manufacturing firms have spent years shifting their supply chains out of China, that effort hasn’t been widely replicated in CRE.
U.S. construction input prices increased just 0.3% in October but are down 0.2% this year, helping contribute to margins for contractors, according to Construction Dive. Basu told Construction Dive last month that any rush to import goods before the tariffs would put upward pressure on construction inputs.
“The issue here is not so much timeline necessarily, as it was in the past when we had those supply chain issues,” Basu said. “What [contractors] don't want to have is, ‘I've given a fixed price and now my materials cost or equipment costs go up because of tariffs. And now this project that was supposed to make me money is going to lose me money.’ That's not an acceptable outcome. Then you would expect to see some stockpiling.”
To take full advantage of any stockpiling rush, existing IOS owners along the major supply routes should look to buy or lease adjacent parcels with appropriate zoning or configure their sites to allow for denser material storage, Hunsucker said. They should also check zoning ordinances on maximum allowable stacking heights.
Basu initially expects a lot more stockpiling of equipment, as opposed to materials, with the one exception being lumber in the residential construction industry.
For CRE, equipment is bulky and needs to be stored, often for months before being used on the job site, and both China and Mexico export these machines to the U.S. In an industry as fragmented and price-dependent as construction, contractors can get a leg up if they can save money on equipment now, Basu said.
Still, it isn't always easy to get some materials early, according to DPR Construction Supply Chain Leader Tim Jed.
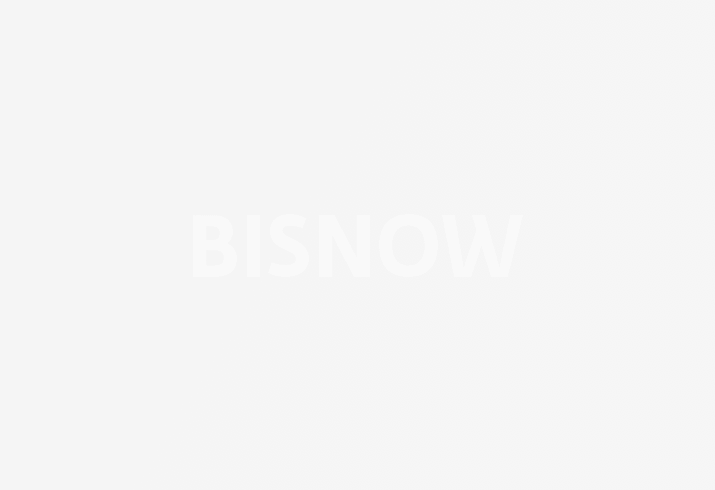
“Due to the nature of our business, and the specialty of the products that would be affected, it is unlikely, aside from some basic types of materials raw materials, steel stock, copper bus bar, etc.),” he wrote in an email.
But determining how tariffs may impact their bottom line will be crucial for contractors going forward, he said. Contractors should understand their supply chain, verify increases in pricing that are being requested and, where appropriate and possible, consider U.S.-made alternatives to international products.
Contractors working on ongoing projects should consider accelerating delivery, even for domestic products, since tariffs could impact the entire supply chain, Jed said. And those looking at estimation or preconstruction should consider potential cost and lead time impacts when delivering estimates to clients.
Basu said that while he has anecdotally heard about stockpiling and movement taking place, the industry hasn't yet started doing so on a massive scale for a few reasons.
First, it isn't guaranteed the tariffs will be implemented. He thinks many see them as a negotiating ploy and don’t believe Trump would make a sweeping change that would hurt American businesses.
Second, the industry has already dealt with supply chain issues for years and has built up stockpiles already.
There is precedent for a high demand for storage space when tariffs are enacted. During Trump’s first term, when he levied 25% tariffs on structural steel from China during an e-commerce boom, big users stockpiled the material, creating demand for material storage capacity.
For Hunsucker, this situation again speaks to the value of IOS, due to its low supply and centrality to the supply chain and logistics networks real estate and other industries depend on. Even with potentially radical shifts in trade, goods and the trucks that carry them need somewhere to stop.
“Since the supply chain is built to be optimized, it becomes glaringly obvious when demand shocks occur, like the COVID e-commerce boom,” Hunsucker wrote. “IOS is being zoned and re-developed out of existence, slowly reducing supply of suitable storage yards over time.”