6 Ways The Supply Chain Is Changing Industrial Real Estate
Industrial real estate is undergoing a transformational renaissance. At the heart of this change? Warehouses that form the spine of a modern supply chain.
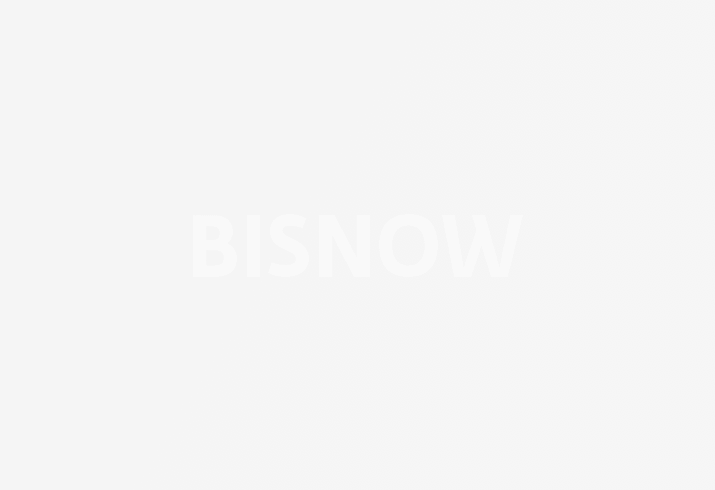
Driven by our increasing shift online for retail needs and the demands of global product flows, companies have been fundamentally transforming their supply chains. Since the warehouse is a central node in any modern supply chain, these facilities are being upgraded and reimagined so our products get to us on time, intact and at low cost.
Bisnow spoke to Prologis head of research Chris Caton about key trends in supply chain modernization driving the creation of the industrial warehouse of the future. Chris joined Prologis three years ago to lead its research division. Before then, he learned the intricacies of the real estate business at Morgan Stanley and CBRE. Comfort with complexity is especially important at a place like Prologis, since it works in 20 countries helping 5,200 customers deal specifically with B2B and e-commerce supply chain challenges.
Going Global
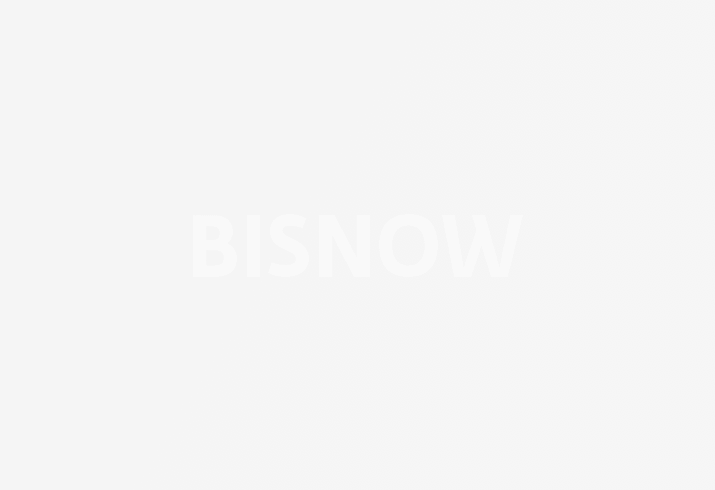
The modern supply chain is an international affair. Consider what goes into a Boeing 787 jet liner, for example. It has wings from Japan, landing gear from the UK and fuselage components from Kansas. How does real estate adapt to these needs? Chris broke the answer into two parts: infrastructure and design. For example, since shipping by water is cheap, global networks work well near established port facilities that can quickly load and unload. Prologis research has shown design elements such as “dock-high doors, expansive truck courts, sufficient trailer parking, ceiling heights and column spacing designed for maximum efficiency” are essential. The Prologis facility pictured above is in Prague.
Go Big
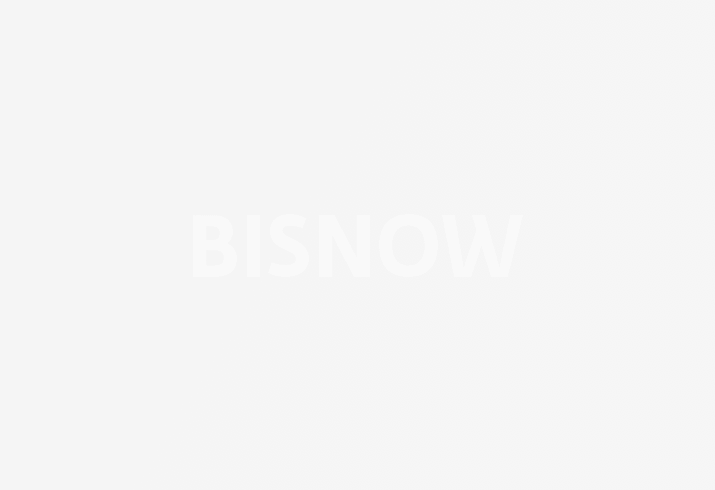
Logistics facilities are getting bigger and offering multiple services for clients. While older facilities in the supply chain were highly specialized and sometimes located far away, clustering these different parts at a centralized hub known as a logistics park boosts efficiency and lowers costs, Chris says. A well-designed park takes into consideration optimized traffic flow and carefully looks at issues such as points of entry and exit. A larger, full-service park ensures goods flow quickly and in volume from one point in the supply chain to the other with minimal hassle and with short wait times.
Consolidation Is Key
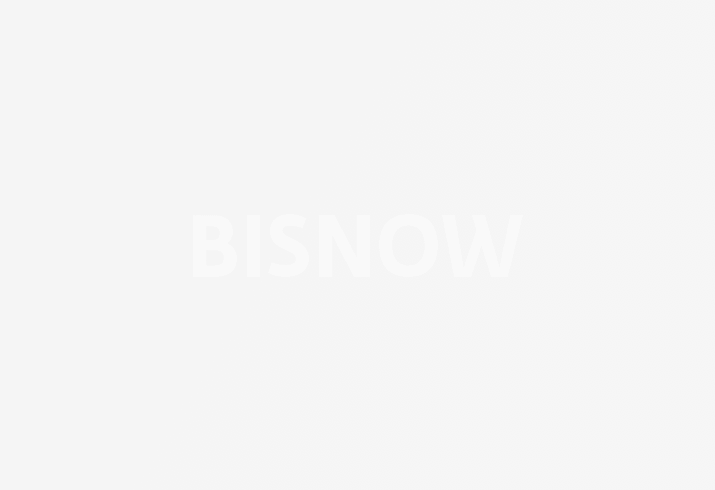
Operators are looking to merge several Class-B properties into a larger Class-A unit. Larger facilities usually lower costs and realize economies of scale. Also, modern facilities make operations more efficient even if there is an increase in rent/SF. The tradeoff is new facilities often offer “superior access to transit infrastructure, be it ports, airports, intermodal or the basic road network.”
E-Commerce Ready
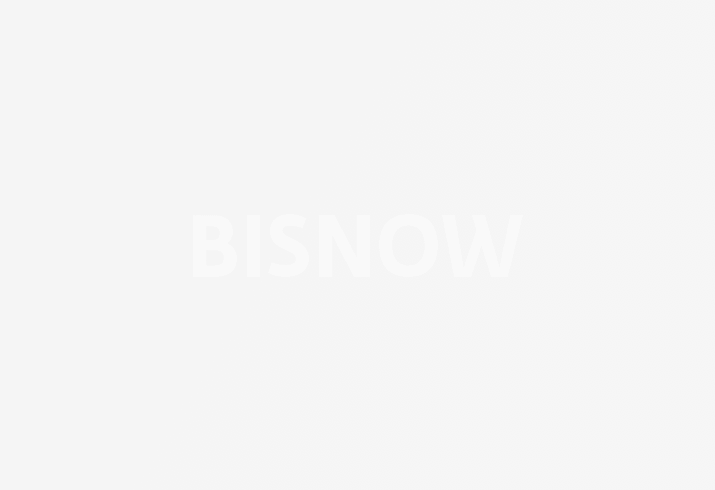
Amazon and Alibaba are fundamentally transforming the way goods are stored and distributed. E-fulfillment—the act of translating your buy click to a package at your doorstep—is a process that needs a particular set of requirements from real estate. Given the labor-intensive nature of the task, companies want facilities near a strong labor base, plenty of parking, proximity to customers and shipping channels.
The growth and diversity of the sector has seen different uses of real estate. Established national and international brands that conduct large volume business need mammoth warehouses that occupy 750k SF, Chris notes. Also, retailers are competing to deliver goods faster and they turn to infill real estate in major population centers for their needs. Smaller players are realizing repurposing existing buildings for e-tail is a cost-efficient route.
Last-Mile Delivery
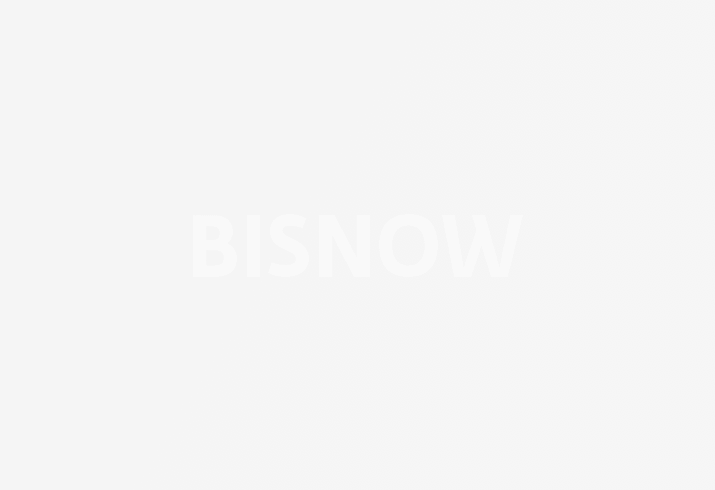
Chris tells us e-fulfillment has two fundamental challenges: the 50-mile challenge and the last-mile challenge. It can be thought of as getting goods to a market and then into a market, he said. Transportation costs claim more than one-half of distribution costs while real estate claims less than 10%. Therefore, customers are willing to pay higher rents if it means they can reduce transportation costs and be in proximity to major consumer markets that will determine future success. Getting closer to the customer is all the more important as companies are offering expedited services, such as same-day delivery.
Another fundamental aspect of a successful last-mile delivery strategy is access to markets. Infrastructure that can move product quickly and reliably to the customer, such as a high-capacity road network and well-maintained rail lines, are absolutely essential. Then the location of the center near these transportation hubs becomes an important—if not the most important—consideration when selecting a logistics partner, Chris notes.
Sustainability
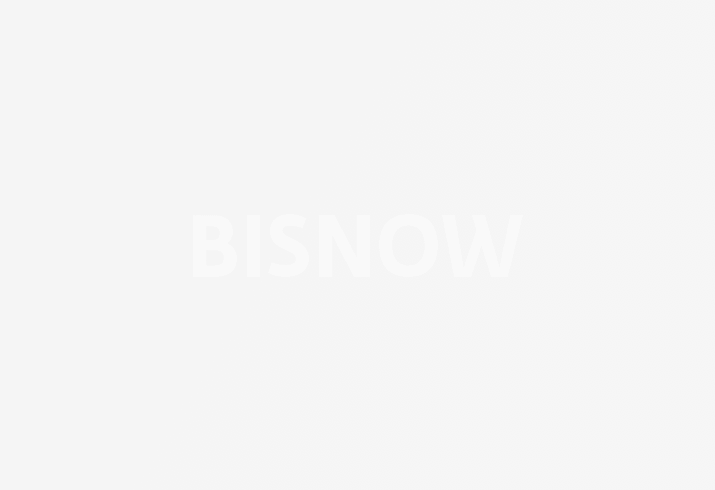
Prologis has a specific commitment to lowering the energy footprint of large industrial logistics facilities. This focus not only makes the facilities better neighbors, but also lowers operating costs. The company's operating portfolio has 31% cool roofs and 73% efficient lighting. Prologis ended 2015 with a solar energy generating capacity of 149 MW. In all, it holds 173 sustainably certified buildings that cover 69M SF across the world.
Prologis has been recognized as a sustainability leader. The logistics company is one of the Global 100 Most Sustainable Corporations in the World for the eighth consecutive year. In 2015, it won NAREIT’s Leader in the Light Sustainability Award in the Industrial Sector. Prologis is also a component of the Dow Jones Sustainability Index for North America and has recently been listed on the Asia Pacific Index.