Fixing What Ails The E-Commerce Supply Chain 'Like Turning An Aircraft Carrier'
For more than a year, companies have been racing to lease more and more warehouse space across the U.S. as they build out their logistical supply networks in the face of surging e-commerce demand.
But the coronavirus pandemic has shown a weakness in that strategy: The systemic issues plaguing the shipping industry today stem from a critical shortage of workers facing many industries, a shortage that diminishes shipping and trucking capacity at a time when retailers are racing to get the product on store shelves and to consumers’ front porches.
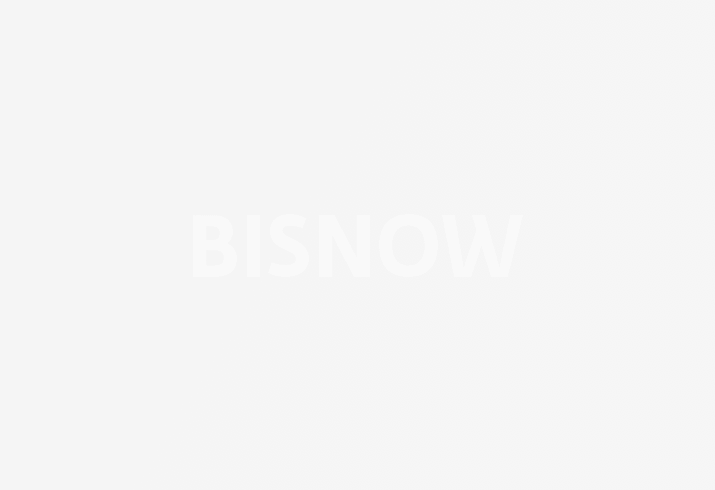
It's a problem that won't be solved by Christmas.
“Fixing this holiday, it's literally like turning an aircraft carrier. I mean, what can you really do at this juncture?” said Adam Roth, the director of the commercial real estate brokerage firm NAI Hiffman's global logistics platform.
Since 2017, developers have delivered between 200M SF and 300M SF of new industrial space every two quarters, according to data from the Federal Reserve Bank of Atlanta.
In the past two years, much of that construction came in response to consumers' hyper-adoption of online shopping during the pandemic. While consumers have returned to shopping in brick-and-mortar stores as local governments gradually eased social distancing restrictions, their online shopping habits still haven’t waned much. E-commerce penetration into total U.S. retail sales climbed from 12.4% in 2019 to 15% by 2021, according to the Atlanta Fed, citing U.S. Census Bureau data.
Warehouses have evolved over the past few years to reflect this modern e-commerce landscape where consumers want products within a matter of days, if not hours.
Developers raised roof heights to accommodate e-commerce users stuffing a wider variety of products into distribution centers as they send single items to individual households instead of bulk shipments directly to stores. Floors were designed to hold more weight to allow for robots and other automation to be able to process more orders in shorter amounts of time. Trailer and truck parking became plentiful to help provide a just-in-time inventory model for retailers.
That worked smoothly up until the pandemic. Now, limited capacity and labor struggles are stretching America's logistical system to the breaking point as consumers continued to shop despite the recession spurred by the pandemic.
The logistics industry is an “incredibly complex system, which prior to it being turned off at the start of the pandemic, worked very well together,” said co-warehousing operator Saltbox co-founder Tyler Scriven said. “Imagine trying to rebuild a watch that has 10,000 pieces. It's hard to get it running well again.”
Even before the pandemic, labor availability was a critical issue and a key to warehouse site selection. But labor is a current headache across the entire supply chain, experts say, from warehouses to trucks and trains.
The lack of workers is limiting the capacity to get goods off of ships coming into U.S. ports and into local stores or distribution centers. Finding and retaining labor was among the third-party logistics industry's largest concerns, with 73% of those saying hiring is a crucial challenge, up from 58% a year earlier, according to Inbound Logistics' 2021 3PL Market Research Report. For shippers, labor concerns were the second-biggest challenge behind transportation costs, according to the report.
While a shrinking labor pool has been years in the making, Leslie Ajlouny, the chief marketing officer for the 3PL Evans Distribution Systems, said the pandemic only exacerbated the situation, especially with truck drivers, many of whom have left the workforce or switched to other careers.
“It's the same thing that's affected the restaurant industry and the service industry in general,” said Ajlouny, the immediate past chairperson of the International Warehouse Logistics Association. “It's much, much worse now than it has been in recent years. We are constantly recruiting. It's still a struggle.”
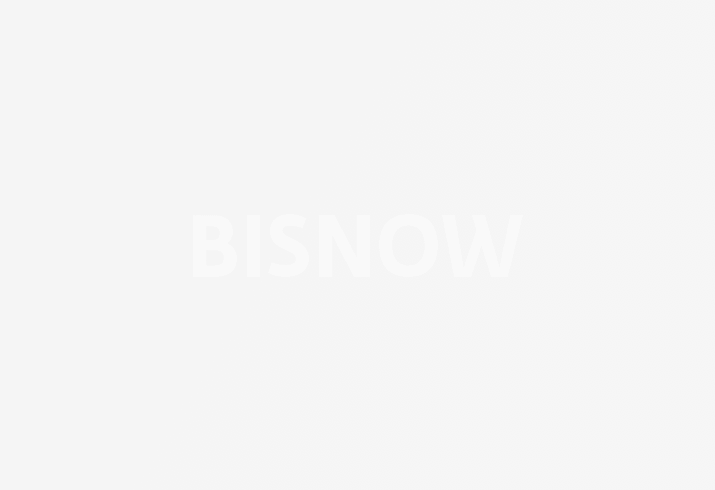
The logistics industry is attempting to alleviate some of the systemic problems facing it in various ways. Major retailers and companies like Walmart, FedEx, UPS, The Home Depot and Samsung have pledged to use more overnight labor at two major California ports to help unload 3,500 more containers a week in an effort to combat the bottlenecks, Reuters reported.
Walmart, Target, Costco and Dollar Tree also are chartering their own ships to get goods to U.S. ports.
Warehouse operators are tweaking aspects of their system to try and alleviate some of the anticipated headaches.
Gooten, an on-demand printing firm that produces wall art, furniture and printed clothing for a variety of retailers, plans to shift orders to one of 70 global production facilities as needed, Gooten Chief Marketing Officer Mark Kapczynski said. If they hit delays in one, those orders will be shipped to another facility to fulfill them.
“The whole nature is we can't be dependent anymore on the single warehouse model,” Kapcyznski said.
Some fulfillment operators also are adding surcharges for shipping to e-commerce clients, said Gary Porter, the chief analytics and development officer for GoFor Delivers, a last-mile logistics and delivery service.
"Surcharges are reduced for those customers shipping year-round volumes, whereas new entrants seeking holiday capacity without a track record will end up paying a premium," Porter said.
Saltbox is aggregating client orders into fewer pickups to guarantee FedEx will come by, rather than hoping services will still come for individual shipments, Scriven said.
Adding even more warehouse space, especially around ports, could alleviate some of the issues facing the industry, Transwestern Development Co. Logistics Group partner Greg Boler said.
“It is really having more warehousing closer to the port, or period,” Boler said. "Right now, there's no room at these ports. Warehousing is essential to relieving the crisis that is here."
Trucking and warehousing companies are on a hiring spree in time for the peak holiday shopping season.
GXO Logistics, the world's largest third-party logistics provider, announced this past week that it intends to hire 9,000 contract and permanent workers in the U.S. for the holidays and a total of more than 20,000 worldwide to help wrestle with growing demand.
While GXO believes it will be able to follow through on its hiring ambition this year, it comes at the sacrifice of increasing costs, GXO Chief Commercial Officer Bill Fraine told Bisnow.
“Wages are up,” Fraine said, easily by as much as $5 an hour. “We found in most markets because we're GXO and because we're well-known ... it's tight. But we're not missing heads. That comes with planning months ago, not starting now.”
FedEx estimated labor shortages impacted the shipping giant’s second-quarter results by $450M, Chief Operating Officer Raj Subramaniam told investors during an earnings call.
“The competition for talent, particularly for our frontline workers, has driven wage rates higher and pay premiums higher,” Subramaniam said Sept. 21. "While wage rates are higher, the more significant impact is the widespread inefficiencies in our operation from constrained labor markets."
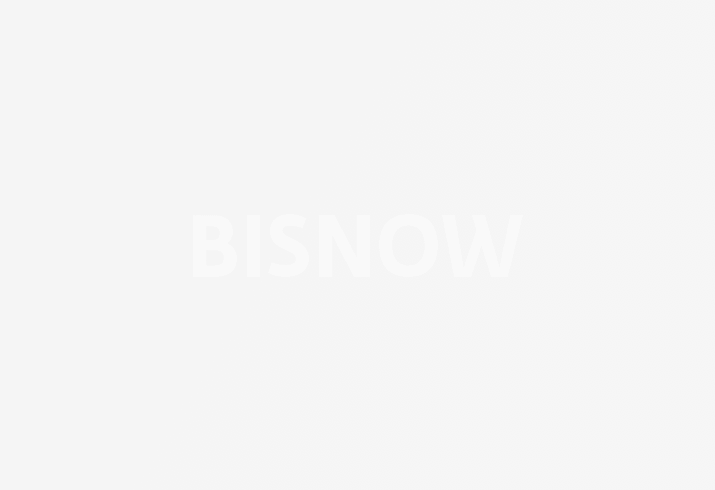
There are potential infrastructure solutions to address the delivery of goods to stores. Experts say as labor becomes more expensive, technology and robotics become more feasible to buy for warehouses. Boler and other experts also say manufacturers need to return to the U.S. to produce goods as well, relying less on Asian markets.
“The only way that this is going to significantly change is [when] we have kind of onshoring domestically here in North America,” he said. “This is a systemic infrastructure concern. But I think it will make us better as a country when we’re no longer dependent on other countries shipping stuff to us. That is not going to happen before Christmas."
In the end, Saltbox’s Scriven said solutions to the systemic issues plaguing the industry this year are out of any warehouse operator, 3PL, port operator or railway’s control. Instead, it’s about the need for more infrastructure improvements in the U.S., especially as consumers shift more toward online shopping.
“The problem will get much worse before it gets better, and that is unavoidable, I believe,” Scriven said. “We've kind of loosely been aware ... that we lack the typical infrastructure to support our growing digital economy. But now we're seeing that firsthand and we're seeing what that feels like. Our technological advances had outpaced the investment and growth of our physical infrastructure.”