Greystar’s First U.S. Modular Apartment Complex Signals Growth In Once-Fringe Sector
The country’s biggest apartment owner is jumping into what has until now been a niche segment of the housing market with the opening of its first U.S. modular complex.
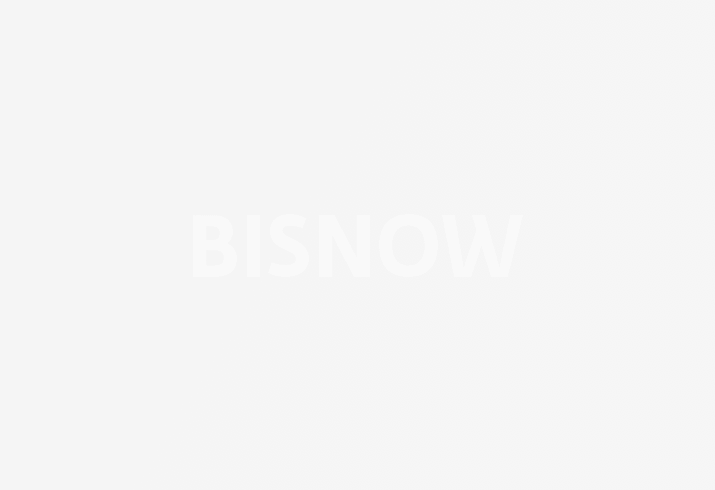
Greystar Real Estate Partners on Monday opened Ltd. Findlay, a six-building modular apartment complex in Coraopolis, Pennsylvania, The Wall Street Journal reported. Charleston, South Carolina-based Greystar developed the six-building, 312-unit property at its modular factory in Knox, Pennsylvania.
Ltd. Findlay is one of the largest multifamily modular projects in the U.S. and Greystar’s first in the country, though it has another half dozen in the pipeline. Modern Living Solutions, Greystar’s modular construction business, is a wholly owned subsidiary that “focuses on delivering housing at scale and at a price point that is attainable,” according to its website.
Modular construction involves constructing modules in a factory before transporting them to the final construction site for assembly, according to trade group Modular Building Institute. Its use was once primarily reserved for emergency and low-cost housing, but the annual market share of modular construction more than tripled to 6.6% from 2015 to 2023, according to the institute.
The construction process uses the same materials and standards as conventional construction, but projects are completed in about half the time.
Greystar built Ltd. Findlay about 40% faster than its traditional apartment complexes, Andy Mest, managing director of Greystar’s modular business, told the WSJ. The on-site construction of the modules used a third of the usual workforce and generated 90% less waste. The project was also 10% cheaper than the construction of a traditional multifamily project in Pittsburgh.
Ltd. Findlay shares many similarities with a traditional complex, offering units with one to three bedrooms and between 660 SF and 1,370 SF. Amenities include a gym, an amphitheater and bocce courts, according to the WSJ.
Greystar first used modular construction in the UK, and Mest said he hopes to replicate such projects in the U.S. But the six modular properties in Greystar’s pipeline will all be within a 600-mile radius of the Knox manufacturing facility due to the cost and difficulty of transporting modular apartment units.
Access to commercial financing is one of the most significant barriers to modular construction, according to an August report from the National Renewable Energy Laboratory. Lenders are often unfamiliar with modular construction and may offer lower loan amounts with higher interest rates, while manufacturers need large upfront deposits since materials alone can account for 60% or more of the production cost.
But support for the building method is growing, especially given a dire need for more housing just as the construction industry is expected to be impacted by President-elect Donald Trump’s proposed tariffs and immigrant deportation. The modular industry would still feel the effects, but it would be more insulated than the traditional construction industry, the WSJ reported.
As labor and construction costs rise, “modular emerges as a more viable alternative to traditional construction methods,” said Jose Luis Blanco, a senior partner at McKinsey & Co.
McKinsey projects global modular construction revenues could grow from $180B in 2022 to $1.1T in 2040.