CRE Braces For Higher Costs, Perhaps Inflation Stemming From Trump Tariffs
President-elect Donald Trump’s promised tariffs are cause for concern among many in the commercial real estate industry, with developers and builders fretting over the possibility of material cost increases.
Others in the CRE sphere are even worried that tariffs could prolong inflation, the troublesome indicator that led the Federal Reserve to begin hiking interest rates in 2022, a policy it only began to reverse in September.
“The greater impact on CRE could come from the fact that tariffs are inflationary and, all else equal, will keep interest rates higher for longer,” Associated Builders and Contractors Chief Economist Anirban Basu told Bisnow.
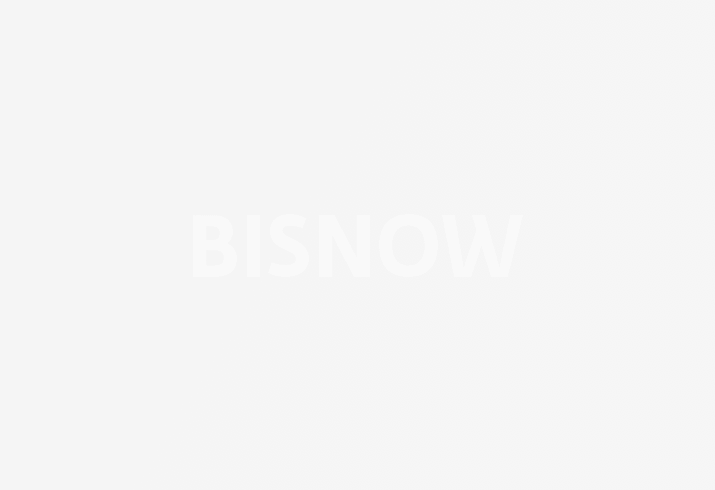
Trump has proposed new levies on foreign goods, including a 10% universal tariff and a 60% tariff on Chinese goods. These tariffs could “increase construction costs, driving up prices on housing and commercial projects” according to an analysis from RCLCO.
While many in the real estate world are happy to see their fellow developer Trump back in the White House, the former and soon-to-be president's tariff suggestions have raised eyebrows.
Many analysts expect Trump to negotiate or soften some of these tariffs when he actually takes office. During his first administration, when he put tariffs on steel and sparked a number of retaliatory tariffs from targeted nations, he did end up negotiating.
If allies like Vietnam or Taiwan were excluded from a new round of taxes, that would mean that steel from those countries could help dampen the blow of losing access to cheaper Chinese steel. But even then, there is still fear that any significant tariffs won’t just alter the U.S. cost for key construction components but also alter the global price of goods. Global prices for copper dropped 4% on the news of Trump’s reelection due to fears of dampened demand.
“This is where it gets harder to really dissect what [these tariffs] mean,” DPR Construction Supply Chain Leader Tim Jed said. “Because, is it really everything? Is it raw materials? Is it specific products?”
But as they currently are proposed, they would have impacts that would dampen enthusiasm in CRE just as rate cuts started turning around the long-term outlook. Goldman Sachs believes these tariffs could reduce GDP by half a percentage point in the first 18 months, which would likely slow CRE development, especially in manufacturing and retail. As soon as the tariff policies become clear, Jed expects an instant spike in prices.
“Hypothetically, tariffs could delay some investments,” Unispace Americas Managing Director Daniel Maldonado said. “But if the interest rates are steady and there’s an ease in regulations, then that could favor more CRE acquisitions and construction.”
Most materials are, at least in some capacity, produced domestically. Some, like drywall, concrete and gravel, get produced in great volume stateside. The real issue, according to Basu, is that as a nation, the United States “produces very few materials at the scale necessary to support the construction industry.” It gets more challenging when the entire supply chain is taken into account. Many domestic metal producers, for instance, use iron ore from Brazil and Canada.
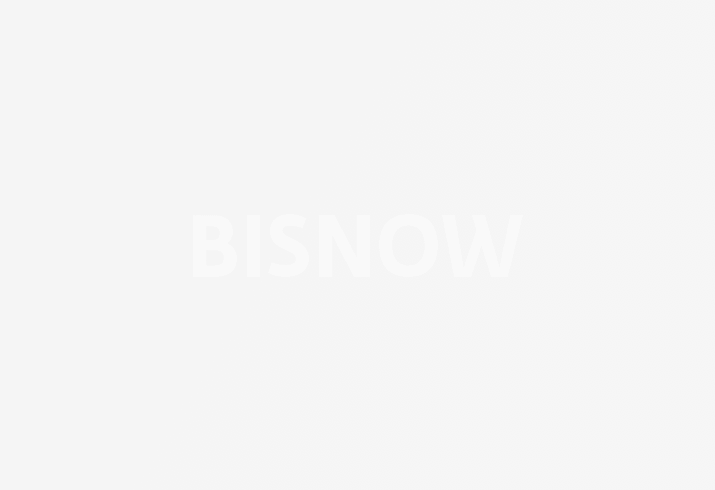
The proposed 60% tariff on Chinese goods might have the most impact on the building trades and costs. Significant amounts of specific materials, as well as electrical equipment and switchgears, primarily come from China. Over half of imported bathroom ceramics and glass mirrors come from China, according to data from the Observatory of Economic Complexity, and those aren’t produced in large quantities in the United States, Basu said.
For other popular materials, like building stone or cement articles, between a fifth and a quarter of all imports come from China. About 57% of glazing glass also comes from the country. And aluminum, which gets used in storefront systems and ornamental stairways, mostly comes from China. Steel might have the most widespread impact — roughly 54% of the world’s crude steel is produced in China, Jed said.
“While these materials can be sourced from other countries and are, to some extent, produced domestically, doing so would come with increased costs,” Basu said. “If too much demand is displaced, we’ll likely see longer lead times for certain materials.”
Furnishing and fixtures would also present a challenge. The United States produces mirrors domestically, for instance, but they typically are not the type used to outfit bathrooms in an office building.
Finally, technical and electrical gear, including the gear and even vehicles used to do construction, might become increasingly hard to come by with extended tariffs. Minerals like cobalt and chemicals like arsenic used in certain tech hardware are almost exclusively found and made overseas.
One key distinction that alters the impact of the tariffs is whether they apply to raw and finished materials at the same rate. Jed said that if things like rare earth metals aren’t punished as much as finished materials, that could mean the raw materials themselves could be shipped to a third nation to be assembled, which would be less than importing something directly from China, for instance. But if not, that would raise the price of magnets, metals, glass, ceramics, batteries and electronics.
As far as Jed knows, he hasn’t seen firms stockpiling specific goods and raw materials before the tariffs would go into effect. The industry doesn’t tend to move that fast — projects being built in 2025 likely already have orders placed for goods and materials, and massive orders going one-way in the global supply chain can be more expensive. Jed said that can, in extreme cases, lead to double shipping charges since importers have to send back shipping containers without any return goods.
The construction supply chain has recently dealt with severe supply shocks, from the pandemic to the Red Sea and Panama Canal blockages. Jed said that’s made the industry more nimble and more accustomed to preordering and finding alternate suppliers. This time, however, things are different. The pandemic interrupted production, slowed supply chains and boosted demand for certain types of construction. Basu recalls the image of a neighborhood of single-family homes finished except for the garage doors.
“I've been talking last week with some suppliers on the West Coast, and they were talking about trying to push on their clients to confirm the project earlier before the prices go up,” Maldonado said. “But honestly, I don't think anyone has a certainty on what's going to happen.”
Tariffs won’t stop the production of goods, but they can cause higher costs and push contractors and builders to weigh their options closely. Sourcing material from new countries with smaller tariffs, for instance, might be more time-consuming, making it cost-effective to suffer the extra costs of Chinese goods to make sure a project meets preexisting schedules. This moment of scrambling and uncertainty will favor larger players that can afford procurement departments, while smaller developers and contractors will likely struggle with new pricing and more limited availability.
Based on his experience of the 2018 and 2019 tariffs, Jed believes there’s going to be a lot of lobbying and experts running analyses to see just how tariffs on certain suppliers will impact the economy. Trump will likely claim what’s called Section 232 authority, which grants the president latitude to enact tariffs in the name of defending national security, and a number of other laws granting him power to undo trade imbalances. How far he actually goes remains to be seen.
“There'll be pressure and they'll be lobbying as we start to zoom in on where it's helping and hurting,” Jed said. “My hope is that we would see an adjustment to those things to actually improve the scenario, to the benefit of our economy.”