How Russia's Invasion Of Ukraine Could Impact The Construction Supply Chain
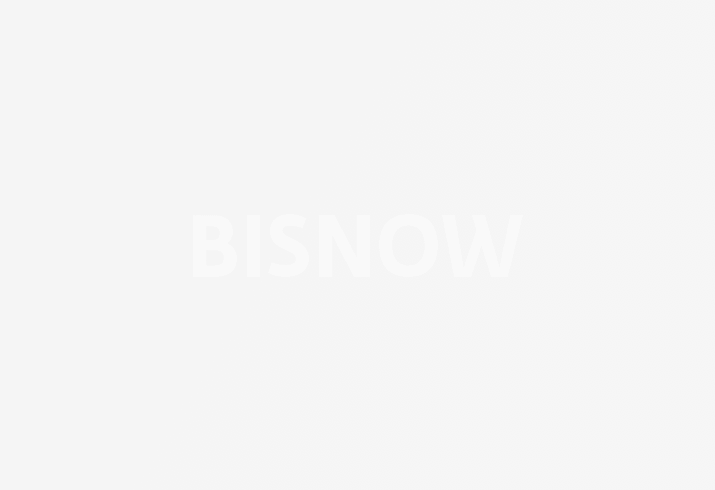
The Russian invasion of Ukraine has generated seismic economic and geopolitical ripple effects, the vast majority of which have yet to come into view.
And while much of the attention has focused on the economic sanctions placed on Russia and Vladimir Putin's inner circle, the conflict is also expected to have negative impacts for developers, particularly in New York City, who have come to rely on certain materials produced in Ukraine.
“With the context of the problems going on in the world, this is not high on the list. But we are starting to see some real concern about the impact this will have on an already-stressed supply chain,” Seth Weissman, founder and president of real estate private equity firm Urban Standard Capital, told Bisnow.
The coronavirus pandemic had unearthed flaws in the supply chain, resulting in two years of extended lead times, increased material costs, labor shortages and higher project costs. With inflation already projected to climb higher over the course of 2022, developers questioned if they were in a position to bear the additional cost of delays from a geopolitical conflict.
Ukraine, along with Belarus, Poland and Germany, is one of the principal producers of windows systems — from manufacturing glass panes and aluminum frames, to assembling windows for export — for developers in the U.S., Weissman said.
Whole products like windows may not be the only building component that could see delays as a result of Russia’s invasion of Ukraine, Savills Executive Vice President and Head of Industrial Services Gregg Healy said.
“The majority of Ukraine’s exports are metals, which go into pipes, impacting the construction market,” Healy said.
Ukraine is the 13th-largest producer of steel in the world, supplying factories in China and elsewhere with raw materials to produce pipes. Ukraine is also the fifth-largest producer of iron ore, making it a key player in steel production — which cannot happen without iron ore pellets.
But Healy said developers are unlikely to face big jumps in cost, because steel is produced in dozens of other countries around the world by multinational firms used to keeping product costs stable through moments of geopolitical uncertainty.
“There’s going to be an increase in cost, but I think it will be pretty minimal,” he said.
Some developers waiting for deliveries from Ukraine are now facing uncertain timelines, as the invasion by Russian troops closed roads, ports and freight trains. Delays to window installations can mean pushing a project back by anywhere from six months to a year, leaving them unable to enclose their buildings and increasing costs that are eventually passed down to consumers.
Urban Standard Capital’s NYC developments narrowly escaped that fate, Weissman said: The windows for one project, 378 Broome St. in NoLiTa, shipped on Wednesday — less than 24 hours before the Russian invasion began.
NYC construction projects looking for window suppliers may look toward slightly higher-cost products coming from outside of Eastern Europe, potentially seeking to omit the region from their supply chain altogether.
“We want to better understand the potential exposure for Belarus, too,” Weissman said. “If you’re a lender or developer, you want to understand what you’re financing. Do you really want to take the risk?”
NYC developers facing delays may pay a heavier price than those in other regions, which have experienced larger gains in rents and housing prices, and demand for building development, over the past two years.
“In certain markets in the Southeast — like Texas, Florida — where prices have jumped significantly, that’s allowed developers to recoup costs and retain price margins. But in NYC, it’s still below Covid pricing, so margins are getting eaten,” Weissman said. “In our lending business, universally, of the developers who have projects starting within the last five years, almost everyone is losing money.”
While the calculations around risk may have changed over the past two years, Healy said, so have developers’ understandings of their supply chains — leaving them better positioned to adapt.
“The supply chain challenges have dramatically impacted the way companies look at where they should locate their manufacturing facilities and how much supply they should have on hand,” he said. “Speed to market is critical. The companies that are going to succeed in the new economy are the ones that learned something and are making significant changes to their supply chains to be prepared for next time.”