Construction Finally Takes To Tech Amid Rising Supply Costs, Lower Productivity
The construction world is incorporating more technology into projects than ever before to adapt and get jobs done during the coronavirus pandemic, but productivity has slowed and supply costs have risen, new reports released this week show.
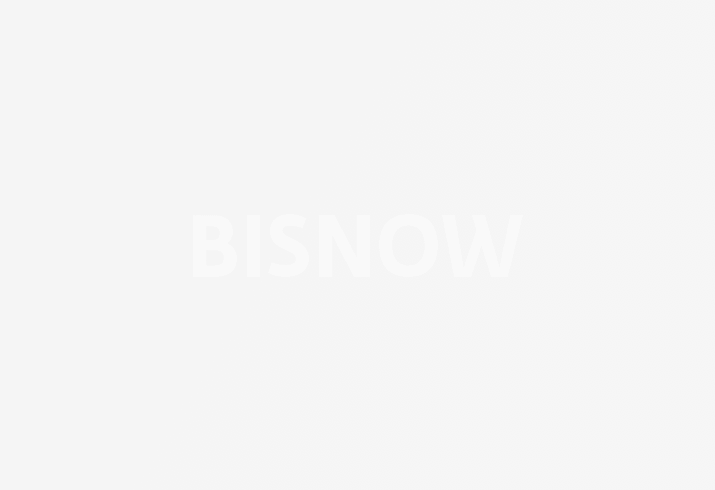
Construction firms nationwide have been using technology to close the efficiency gap caused by increased safety precautions and limited manpower on sites, according to a new report released by JLL this week. Meanwhile, supply chain delays have made some key supplies, such as lumber, more expensive as the cost of labor dips, a new report by Hoar Construction shows.
“Just the adaptability of our industry in the face of such change and changing regulation, we’ve proven to be a very resilient group of workers in the field over the past eight months,” Hoar Construction Division Vice President Will Watson said in an interview. “We found our industry is a resilient one and one that has been deemed essential by society.”
Several forms of technology have become more common across construction sites as the industry attempts to do more work remotely and on-the-ground work more safely and efficiently.
“The urgency and severity of the pandemic condensed technology adoption that likely would have taken three years at a normal pace into a single year,” JLL Construction Research Senior Analyst Henry D’Esposito wrote in a JLL report on the State of Construction technology published this week.
The report analyzed technology adoption rates across tens of thousands of projects nationwide. It found that more projects are using digital collaboration tools such as construction management software Procore. There has also been an uptick in building information modeling and computer-aided design, which provide 2D and 3D design models that outline each layer of a project from the foundation to the smallest electrical details.
Scanning technology that collects imagery and data of a site, such as Matterport and OpenSpace, has also been on the rise as more and more parts of the design and construction process are done remotely.
More workers are using wearable technology, like Triax Technologies, that can monitor worker safety and promote efficiency on a site to increase productivity.
“In the past, there has always been the question of why aren’t construction firms adopting tech faster,” D’Esposito, who has been tracking construction technology for years, said in an interview this week. “This has been the big catalyst event … once you’ve done the hard part of adopting these technologies, you start to see the returns … and once you have that, you’re not going to go back."
But not all technology saw an increase in adoption. Modular construction, which is most frequently used in the hospitality sector, has seen setbacks as the asset class suffers and new projects slow, D’Esposito said.
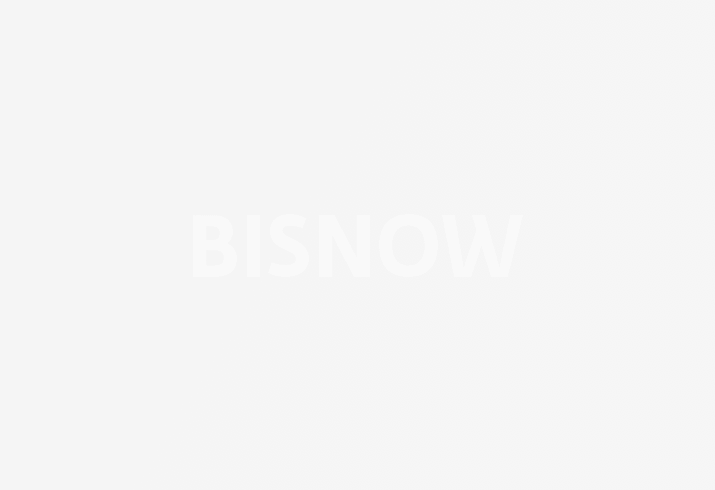
As the use of technology has grown, the industry has had to adjust to a socially distanced world with fewer new project starts than before.
On one construction site in Charlotte, North Carolina, schedule changes and new safety protocols cost a project 12 minutes per worker in an overall workday every day, or a 2% productivity reduction, according to Hoar Construction's report. Over the course of a year, the cost was 16,000 hours in total.
The demand for lumber has skyrocketed amid the pandemic as the number of home renovations and projects surges, Watson said. In April, the cost of lumber was $260 per thousand-foot board. Five months later, in September, that rate had nearly tripled to $948, Hoar found.
Plywood, asphalt, concrete, appliances, plumbing fixtures, heaters, gypsum, builder’s hardware and general millworks also all rose in price, according to the report.
“In the short term, that puts pressure on the cost of projects,” Watson said.
Not all material costs have risen, though. The price of sheet metal, light fixtures, nails, copper wire and power wire have all gone down. The cost of labor has also gone down as fewer large projects come to market.
“On recent project bids, we have started to see more competition, and with it more competitive pricing, in trades because most companies don’t have a stable backlog,” the report states. “As these companies continue to burn off their backlog, the cost of labor is decreasing.”
The labor force has taken a huge hit over the past eight months. In New York, jobs in the sector declined by 38,000 year-over-year in September, according to the state’s Department of Labor. Still, there is a shortage of skilled workers nationally, Watson said, and this will continue to be a problem after the pandemic.
“On a go-forward basis, the pandemic has done nothing to kind of cure some short-term labor issue we have in the industry,” Watson said. “Construction is a highly skilled craft, we still have a labor problem in construction even now when you see unemployment rising across the country in other industries.”